Installation checklist – Rockwell Automation 20C-DG01 PowerFlex 700H AC Drive Safe Torque Off Option User Manual
Page 22
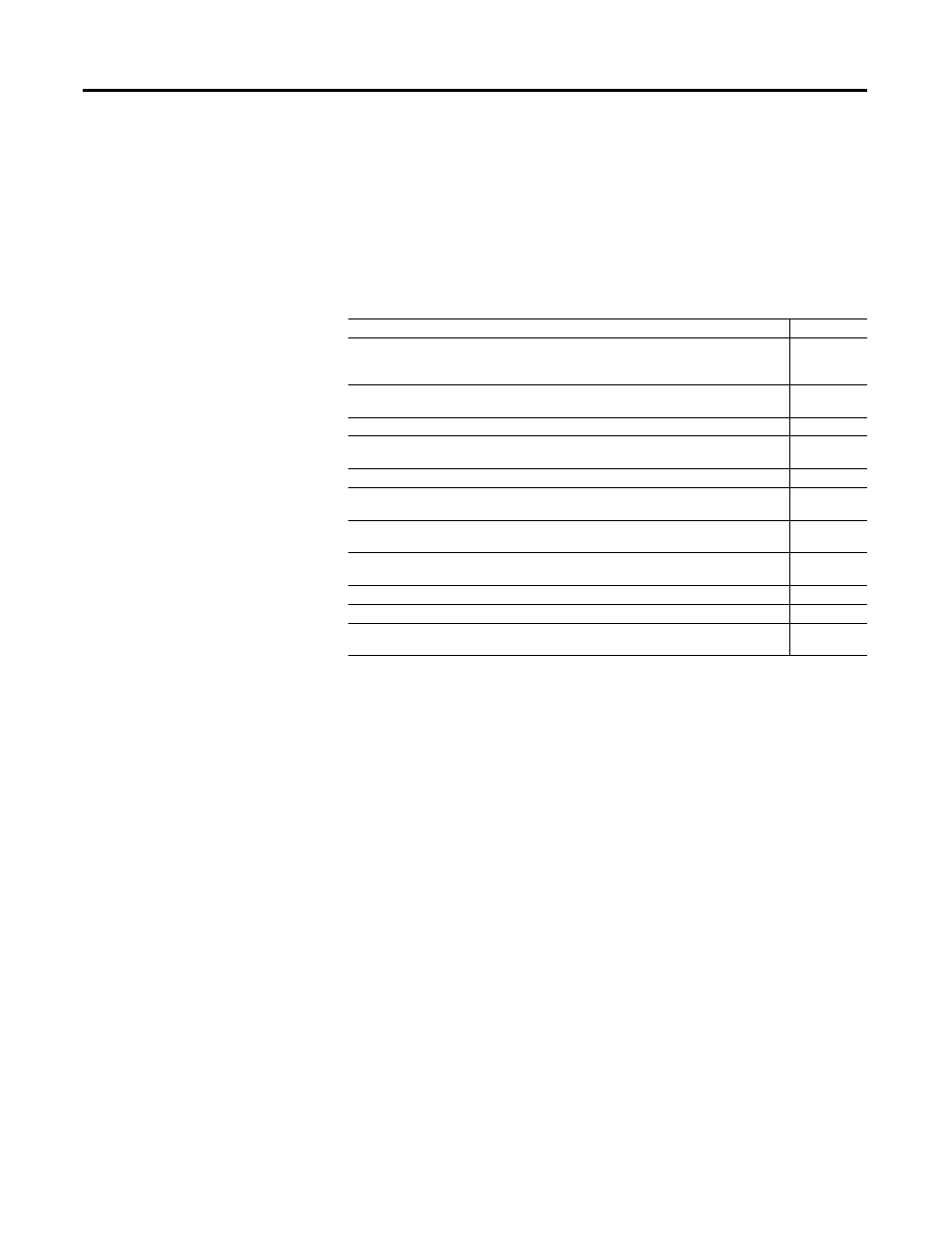
22
Rockwell Automation Publication 20C-UM001B-EN-P - June 2011
Chapter 2 Installation and Wiring
4.
Both “Gate Disable” bits, 10 in [Fault Config1] and 15 in [Alarm
Config1], are set:
The Gate Disable fault takes precedence.
Installation Checklist
The following items must be completed when installing and configuring the Safe
Torque Off option for PowerFlex 700H drives.
Item Description
✓ Complete
A risk assessment has been performed to determine whether the specifications of this
device are suitable for all foreseeable operational and environmental characteristics
of the machine to which it is to be fitted.
The safety switch and/or safety relay used is EN ISO 13849-1 PL d/Category 3 and
EN60947-5-1:1997 annex K compliant.
The reset function is edge sensitive.
In an IGBT fault situation, the safety system has been designed to allow the shaft of
the permanent magnet motor to rotate up to 360 degrees / pole of the motor.
The cabling has been installed to be EMC compliant.
The safety system has been designed so that enabling the drive through the Safe
Torque Off inputs will not lead to an unexpected start of the drive.
Only an approved PowerFlex 700H drive(s) and safety components have been used in
this installation.
The PowerFlex 700H control board, VB00561, revision H, or newer is installed in the
drive (see label on control board).
Revision 2.001, or higher, of firmware is installed in the drive.
Regular intervals have been planned to check the safety function for proper operation.
All information and instructions in this manual have been read, understood and
completed.