Wiring – Rockwell Automation 20D-P2-DG03 DriveGuard Safe Torque Off Option for PowerFlex 700S Phase II and 700L Drives User Manual
Page 25
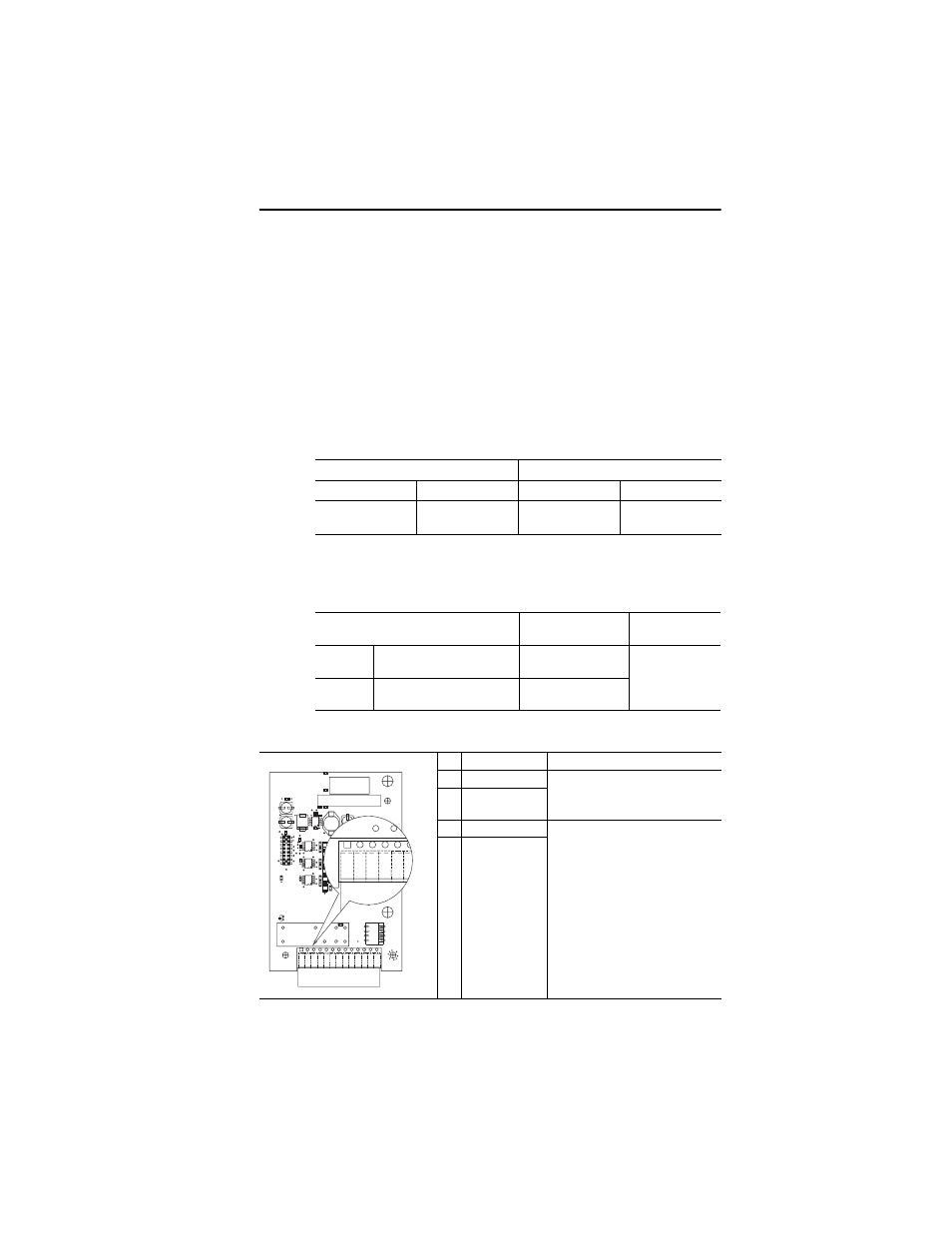
Rockwell Automation Publication 20D-UM007G-EN-P - March 2012
25
Installation and Wiring Chapter 2
Wiring
Important points to remember about wiring:
•
Always use tinned copper wire.
•
Wire with an insulation rating of 600V or greater is recommended.
•
Control wires should be separated from power wires by at least 0.3 meters
(1 foot).
•
All control wires should be shielded cable with the shield earthed on one
end of the cable.
Table 1 - DriveGuard Safe Torque Off Option Terminal Block Specifications
Table 2 - Wire Types
Table 3 - DriveGuard Safe Torque Off Option Terminals Description
Wire Size Range
(1)
(1) Maximum / minimum that the terminal block will accept - these are not
recommendations.
Torque
Maximum
Minimum
Maximum
Recommended
1.5 mm
2
(16 AWG)
0.14 mm
2
(26 AWG)
0.25 N•m
(2.2 lb•in)
0.22 N•m
(1.9 lb•in)
Wire Type(s)
Description
Minimum
Insulation Rating
Unshielded Per US NEC or applicable
national or local code
NOT RECOMMENDED 300V,
60 degrees C
(140 degrees F)
Shielded
Multi-conductor shielded cable
such as Belden 8770(or equiv.)
0.750 mm
2
(18AWG),
3 conductor, shielded.
No. Signal
Description
1
+24V DC
Connections for user-supplied power
to energize coil.
33.3 mA typical, 55 mA maximum.
2
24V Common
3
Monitor - N.C.
Normally closed contacts for
monitoring relay status.
Maximum Resistive Load:
250V AC / 30V DC / 50 VA / 60 Watts
Maximum Inductive Load:
250V AC / 30V DC / 25 VA / 30 Watts
4
Common - N.C.
1 2 3 4 5 6 7 8 9 10
13
12
11
B A R C O D E L A B E L
A S S E M B LY
I D L A B E L
1 2 3 4 5 6