Safety category 3 performance definition, Stop category definitions – Rockwell Automation 20D-P2-DG03 DriveGuard Safe Torque Off Option for PowerFlex 700S Phase II and 700L Drives User Manual
Page 11
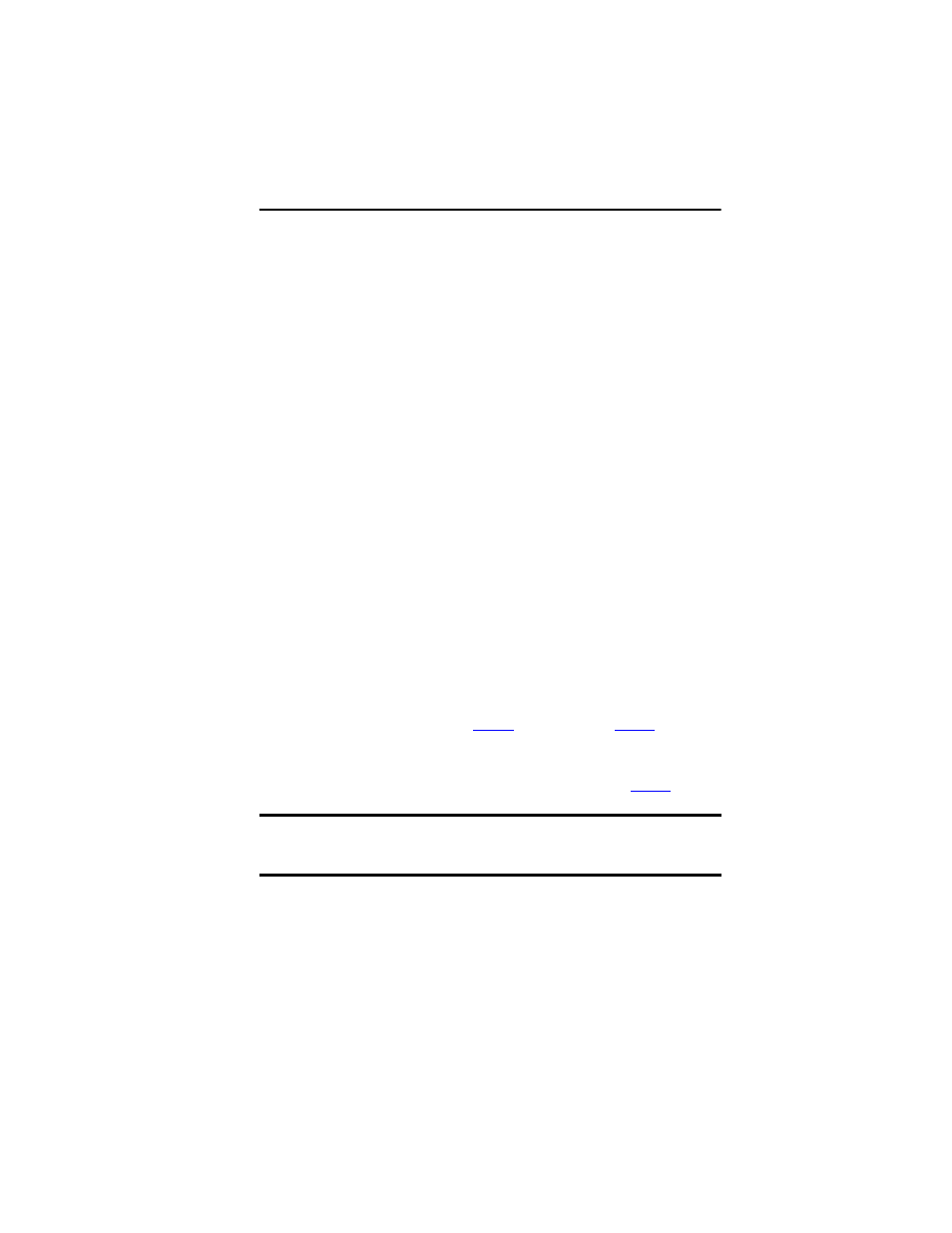
Rockwell Automation Publication 20D-UM007G-EN-P - March 2012
11
General Description Chapter 1
Safety Category 3 Performance Definition
To achieve Safety Category 3 according to EN ISO 13849-1:2008, the
safety-related parts have to be designed such that:
•
the safety-related parts of machine control systems and/or their protective
equipment, as well as their components, shall be designed, constructed,
selected, assembled, and combined in accordance with relevant standards
so that they can withstand expected conditions.
•
well tried safety principles shall be applied.
•
a single fault in any of its parts does not lead to a loss of safety function.
•
some but not all faults will be detected.
•
the accumulation of undetected faults can lead to loss of safety function.
•
short circuits in the external wiring of the safety inputs is not one of the
faults that can be detected by the system, therefore, according to DIN EN
ISO 13549-2, these cables must be installed so as to be protected against
external damage by cable ducting or armor.
Stop Category Definitions
The selection of a stop category for each stop function must be determined by
a risk assessment.
•
Stop Category 0 is achieved with immediate removal of power to the
actuator, resulting in an uncontrolled coast to stop. See “Description of
Operation” Example 1 on
and Example 2 on
.
•
Stop Category 1 is achieved with power available to the machine actuators
to achieve the stop. Power is removed from the actuators when the stop is
achieved. See “Description of Operation” Example 3 on
.
IMPORTANT
When designing the machine application, timing and distance should
be considered for a coast to stop (Stop Category 0 or Safe Torque Off).
For more information regarding stop categories, refer to EN 60204-1.