Surface requirements, Variable circumstances, Checking for dryness – USG Levelrock Floor Underlayment Finished Floor User Manual
Page 4
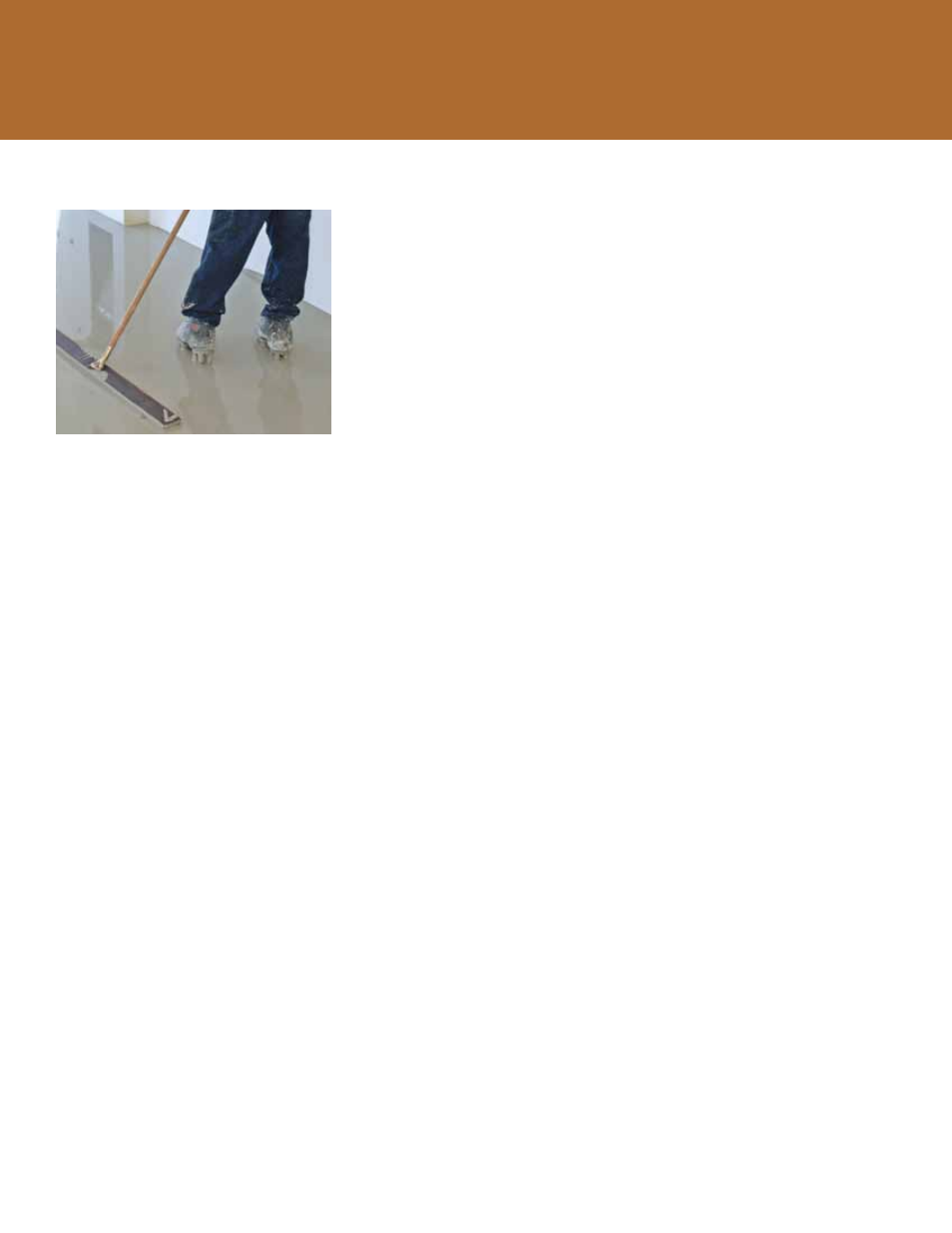
Surface requirements
responsible for ensuring that they are met .
The best and easiest way to accelerate the
drying process (after allowing 3 hours for
setting) is by putting a fan on the floor and
cracking the windows (even in winter) to
ensure good air movement and air exchange .
If the HVAC system in the building is
operational, that should be turned on as
well . However, this is not always possible
(especially in new construction) because
of the concern for construction dust being
blown throughout the building .
If poor drying conditions are encountered
(i .e . high humidity), then strong consideration
should be given to utilizing mechanical
desiccating ventilators such as those
manufactured by Polygon Group US —
formerly Munters — (polygongroup .us) . In all
cases, the use of fans is still recommended .
Remember that raising the temperature
without air movement will not be beneficial . In
fact, certain types of heaters such as forced
air space heaters, will actually increase
the environmental moisture level . After the
L
eveLrock
pour has been completed, the
responsibility for maintaining the proper
drying environment rests with the general
contractor . The applicator should advise
the general contractor in writing about the
importance of proper ventilation .
variable circumstances
The normal drying times listed are under
ideal conditions . As noted, underlayment
thickness, higher humidities, lower
temperatures and poor air flow will lengthen
drying times .
Other situations that affect drying times are:
leaks in roofs; lack of a permanent roof,
windows or doors; and windows left open
during storms which result in flooding of the
floor—all of which have a potential negative
effect on drying .
The standard recommendations regarding
environmental conditions for L
eveLrock
specifically state permanent windows, doors
and a roof must be in place prior to the
installation of L
eveLrock
floor underlayment .*
Where jobsite conditions are not as specified,
(windows get broken, doors left open or roofs
leak), then any water covering a L
eveLrock
floor underlayment should be removed as
soon as possible . In most cases, a first
wetting of a L
eveLrock
underlayment will not
affect the serviceability of the floor, assuming
that it is allowed to dry properly . Repeated or
continuous exposure to water however, can
be detrimental . When in doubt, contact your
L
eveLrock
/a
Lcorp
Network representative .
More importantly, after a flooding incident,
recognize that the floor has now taken up
more free water and therefore standard
drying times no longer apply . Again, good air
circulation and fresh air exchange are critical
to helping the floor dry quickly .
Note *L
eveLrock
®
CSD
®
e
arLy
e
xpoSure
™
floor underlayment is
the exception to this rule .
checking for Dryness
Neither floor coverings nor any primer/
sealers should be installed until it can be
determined the L
eveLrock
floor underlayment
has dried . Likewise, non-breathable crack
isolation membranes should not be installed
until the underlayment is dry . The best way to
determine this is by use of a GE
®
Protimeter
moisture meter (ge-mcs .com) . Two different
models are acceptable for this purpose: the
Surveymaster and the Aquant .
The entire floor should be surveyed to identify
those spots which are taking longer to dry .
Typically, a reading of 180 or less on the
Protimeter moisture meter indicates less than
1% moisture content and suitable dryness
of the floor . There can be slight variance
between meters and that is why USG has
supplied its field quality personnel as well as
the L
eveLrock
applicators with standards to
help calibrate the Protimeter moisture meter
and determine where that “true dryness”
level exists on a given instrument . USG has
conducted an extensive investigation of
various moisture meters and found the
Protimeter to work the best for testing
dryness of L
eveLrock
floor underlayments .
This meter uses radio frequency technology
for checking dryness . There are various other
meters that use probes and other types of
technology, but none has provided results as
consistent as the Protimeter .
Please strictly observe the manufacturer’s
instructions regarding the proper operation,
maintenance and calibration of all moisture
meters .
Additional methods for checking for dryness
include:
· Tape an 18 in . x 18 in . (457 mm x 457
mm) section of 6-mil vinyl plastic (as
per ASTM D4263) to the surface of the
underlayment and seal the edges .
· Lay a 24 in . x 24 in . high-density,
smooth rubber mat on the underlayment
surface and weigh down .
The underlayment is considered dry if there
is no discoloration (darkening) of the
underlayment or condensation on the test
covering after 16 hours . Perform additional
tests if necessary .
Perform tests in critical areas such as high
underlayment thickness or in an area of
poor air flow . More than one test may be
necessary .
■
4