Payload interfaces, Payload fairing, 50” standard minotaur i fairing – Orbital Minotaur I User Manual
Page 41: Payload dynamic design envelope
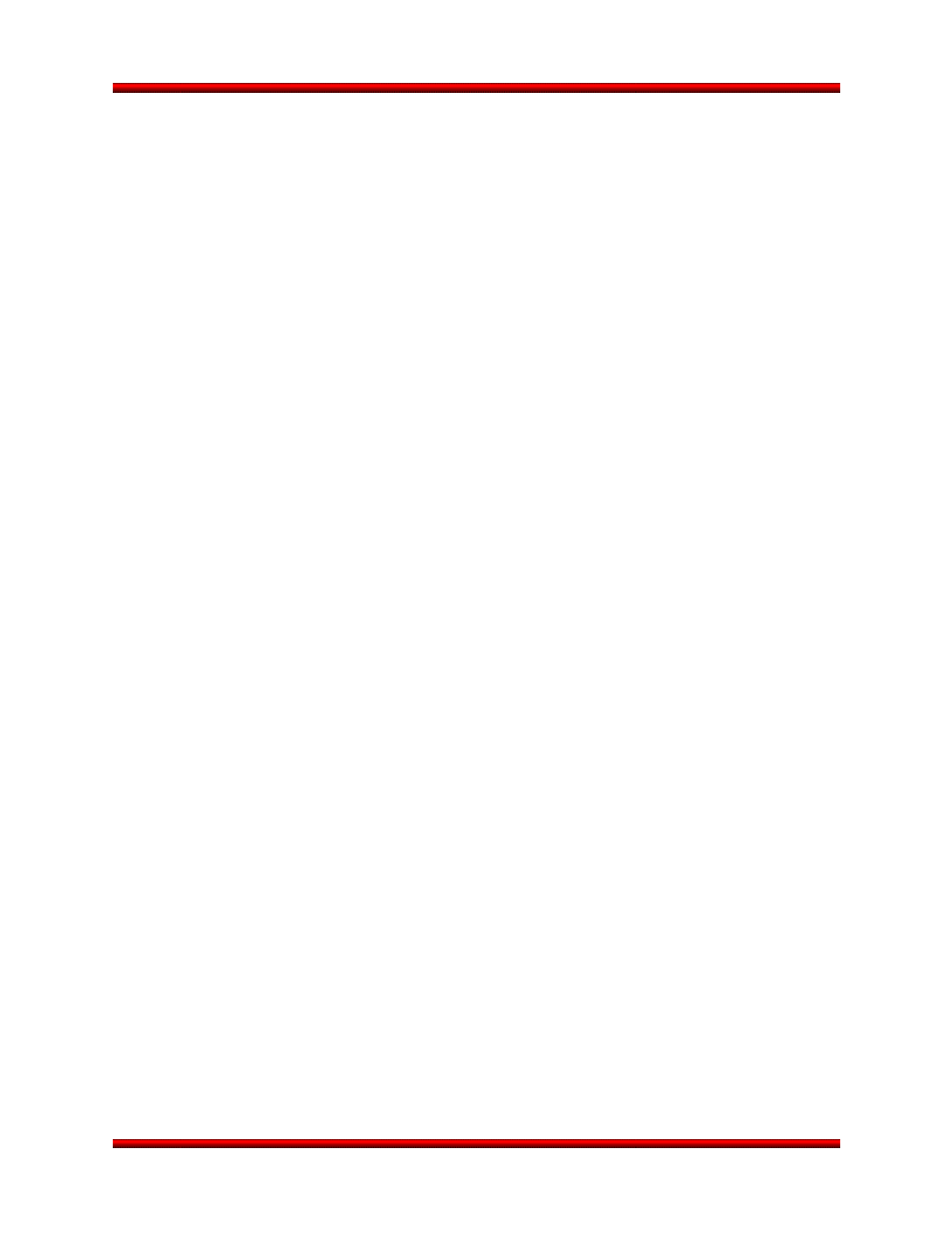
Minotaur I User’s Guide
Section 5.0 – Payload Interfaces
5. PAYLOAD INTERFACES
This section describes the available mechanical, electrical and Launch Support Equipment (LSE)
interfaces between the Minotaur I launch vehicle and the payload.
5.1. Payload Fairing
5.1.1. 50” Standard Minotaur I Fairing
The standard payload fairing consists of two graphite composite halves, with a nosecap bonded to one of
the halves, and a separation system. Each composite half is composed of a cylinder and an ogive
section. The two halves are held together by two titanium straps, both of which wrap around the cylinder
section, one near its midpoint and one just aft of the ogive section. Additionally, an internal retention bolt
secures the two fairing halves together at the surface where the nosecap overlaps the top surface of the
other fairing half. The base of the fairing is separated using a frangible joint. During Flight, fairing
separation involves first initiating the separation nut which releases the internal retention bolt at the nose
of the fairing, then initiating bolt cutters which release the two titanium straps. Next, the frangible joint is
severed which allows each half of the fairing to then rotate on hinges mounted on the Stage 3 side of the
interface. A contained hot gas generation system is used to drive pistons that force the fairing halves
open. All fairing deployment systems are non-contaminating.
5.1.1.1. Payload Dynamic Design Envelope
The fairing drawing in Figure 5.1.1.1-1 shows the maximum dynamic envelopes available for the payload
during powered flight. The dynamic envelopes shown account for fairing and vehicle structural deflections
only. The payload contractor must take into account deflections due to spacecraft design and
manufacturing tolerance stack-up within the dynamic envelope. Proposed payload dynamic envelope
violations must be approved by Orbital via the ICD.
No part of the payload may extend aft of the payload interface plane without specific Orbital approval.
These areas are considered stay out zones for the payload and are shown in Figure 5.1.1.1-1. Incursions
to these zones may be approved on a case-by-case basis after additional verification that the incursions
do not cause any detrimental effects. Vertices for payload deflection must be given with the Finite
Element Model to evaluate payload dynamic deflection with the CLA. The payload contractor should
assume that the interface plane is rigid; Orbital has accounted for deflections of the interface plane. The
CLA will provide final verification that the payload does not violate the dynamic envelope.
Release 3.0
March 2014
28