Appendix, B.5 description of pi parameters – Lenze SCF frequency inverter User Manual
Page 61
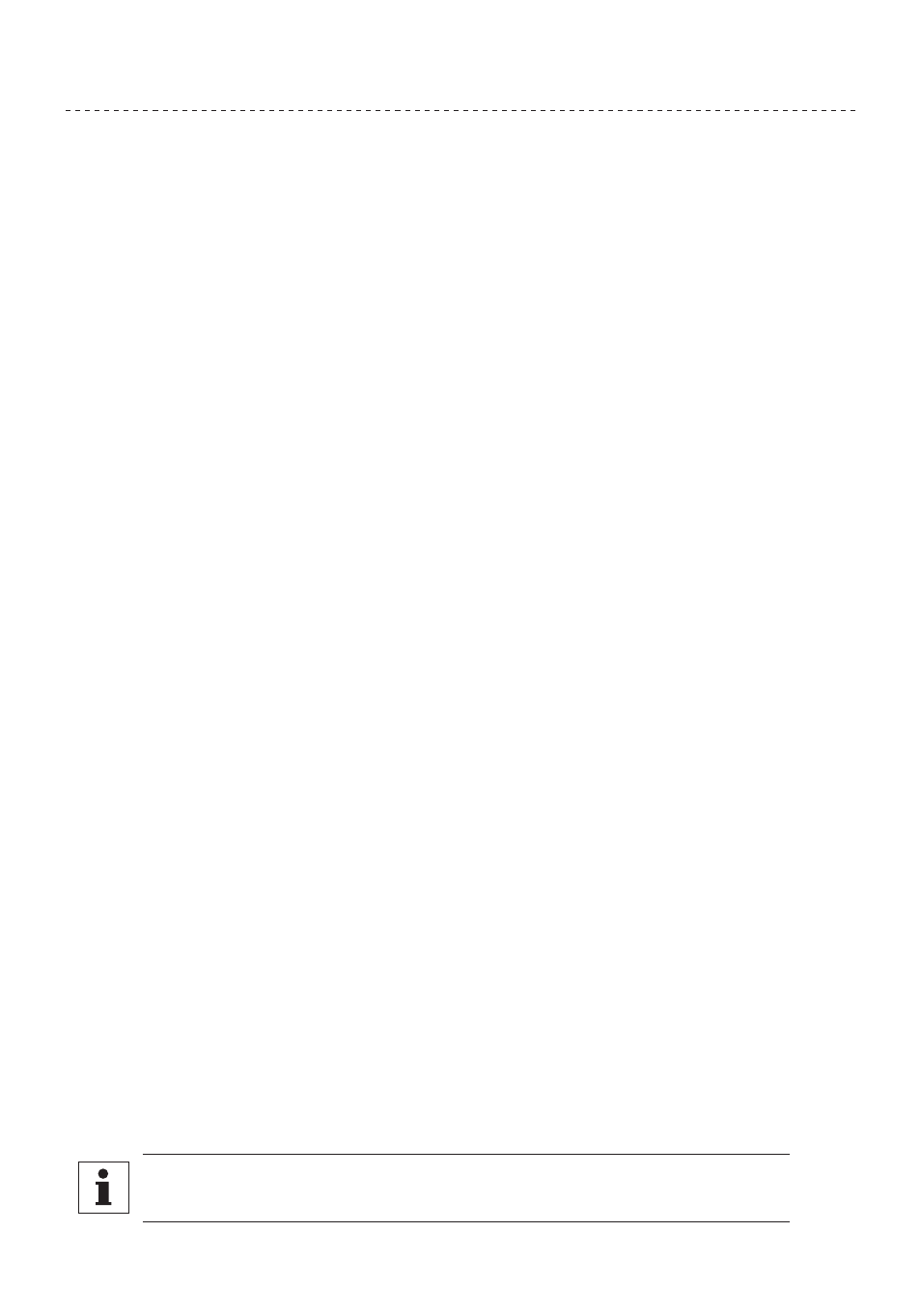
Lenze 13466146 EDBSF01 v24 EN
61
Appendix
B.5
Description of PI Parameters
P10
TB-13A FUNCTION SELECT
12
KEYPAD SETPOINT: This option has been added so that the
p
and
q
buttons on the front of
the drive can be used as the PI setpoint reference source. Closing TB-13A to TB-2 will enable
the PI mode and the
p
and
q
buttons can be used to select the desired process setpoint.
P11
TB-13B FUNCTION SELECT
09
KEYPAD SETPOINT: This option has been added so that the
p
and
q
buttons on the front of
the drive can be used as the PI setpoint reference source. Closing TB-13B to TB-2 will enable
the PI mode and the
p
and
q
buttons can be used to select the desired process setpoint.
P12
TB-13C FUNCTION SELECT
10
KEYPAD SETPOINT: This option has been added so that the
p
and
q
buttons on the front of
the drive can be used as the PI setpoint reference source. Closing TB-13C to TB-2 will enable
the PI mode and the
p
and
q
buttons can be used to select the desired process setpoint.
P61
PI MODE
This parameter must be set to match the type of system and the type of feedback signal used. A
direct acting system is one that requires the motor speed to increase as the feedback signal decreases,
while a reverse acting system requires the motor speed to decrease as the feedback signal decreases.
01
DISABLED
Disables the PI function to allow standard drive operation.
02
NORMAL 4-20 mA
Enables the PI function for a direct-acting system with a 4-20 mA
feedback signal.
03
NORMAL 0-10 VDC
Enables the PI function for a direct-acting system with a 0-10 VDC
feedback signal.
04
REVERSE 4-20 mA
Enables the PI function for a reverse-acting system with a 4-20 mA
feedback signal.
05
REVERSE 0-10 VDC
Enables the PI function for a reverse-acting system with a 0-10 VDC
feedback signal.
When PI is disabled, the drive will operate in an OPEN LOOP mode, responding directly to a speed
reference source selected using STANDARD SPEED SOURCE (Parameter 05) or terminals TB-13A, 13B,
and/or 13C).
P62
MIN FEEDBACK
This parameter should be set to the value of the process variable that corresponds to the minimum
transducer feedback signal (0 VDC or 4 mA). See the example below.
P63
MAX FEEDBACK
This parameter should be set to the value of the process variable that corresponds to the maximum
transducer feedback signal (10 VDC or 20 mA). See the example below.
Example: A 0-100 psi transducer outputs 4 mA at 0 psi and 20 mA at 100 psi. Set MIN FEEDBACK to
0, and set MAX FEEDBACK to 100. The setpoint will then be adjustable between 0 and 100.
NOTE
If a reverse-acting feedback device is being used, MIN FEEDBACK should be set to the
maximum process value, and MAX FEEDBACK should be set to the minimum process value.