1 general data – INFICON HPG400-SP ATM to High-Vacuum Gauge (Profibus) User Manual
Page 6
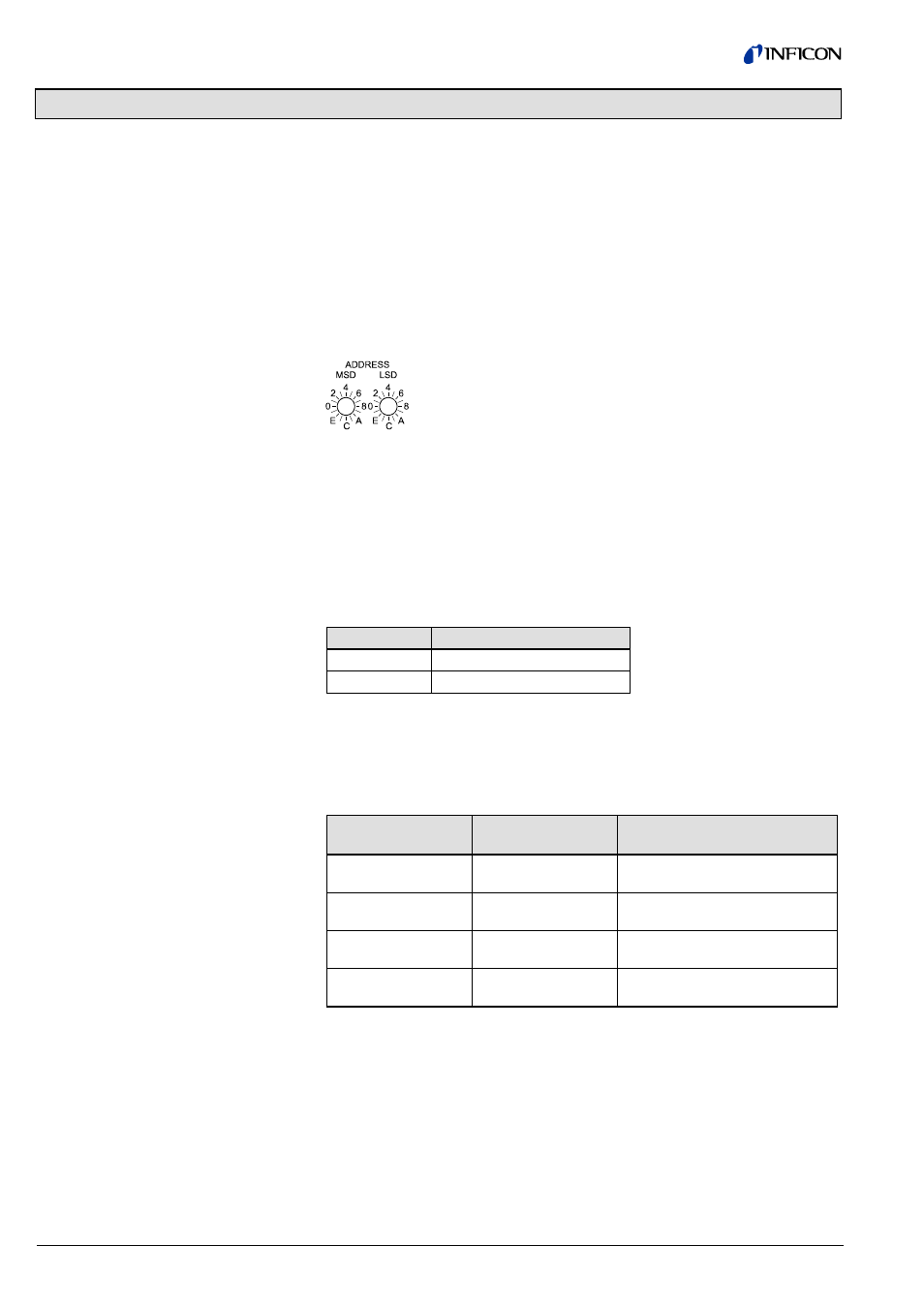
6
tira36e1-a (0310) BPG/HPG400 v1.cp
1 General Data
The gauge supports all data rates defined in the EN 50170 standard (
→ [8]) up
to 12 Mbaud. Automatic data rate setting is supported. Alternatively, a fixed data
rate can be selected.
The device address (
node address) must be set via two rotary switches when the
gauge is installed.
For unambiguous identification of the gauge in a Profibus environment, a node
address is required. The node address setting is made on the gauge.
The node address (0 … 125
dec
) is set in hexadecimal form
(00 … 7D
hex
) via the "ADDRESS" switches. The "MSD" switch is
used for setting the high-order address nibble and the "LSD"
switch for defining the low-order address nibble.
The node address is polled by the firmware when the gauge is switched on. If the
setting deviates from the stored value, the new value is taken over into the
NVRAM. If a value >7D
hex
(>125
dec
) is entered, the node address setting currently
stored in the device remains valid. However, the address can be set via the
Profibus master with the "Set Slave Address" service. This address setting will be
stored in the EEPROM of the gauge.
The ident numbers assigned to the gauges by the PNO (
→ [7]) are:
Gauge
Ident number (hexadecimal)
BPG400-SP
06A9
HPG400-SP
06A8
Depending on the standard telegrams used (
→ section "Cyclic Message Tele-
grams"), the following configuration data have to be transmitted to the gauge during
the configuration phase:
Standard telegram
Master
⇒ Slave
Standard telegram
Slave
⇒ Master
Configuration data
-
2
0x44, 0x84, 0x05, 0x05, 0x05,
0x03
-
3
0x44, 0x86, 0x05, 0x05, 0x05,
0x08
1
4
0xC6, 0x87, 0x8c, 0x0A, 0x0A,
0x05, 0x05, 0x05, 0x03
1
5
0xC6, 0x87, 0x8E, 0x0A, 0x0A,
0x05, 0x05, 0x05, x08
1.1 Data Rate
1.2 Device Address
1.3 Ident Number
1.4 Configuration Data