HMC Electronics 29324 Loctite E-60NC Hysol 2-Part Epoxy Adhesive, Potting Compound User Manual
Hysol® product e-60nc, Technical data sheet
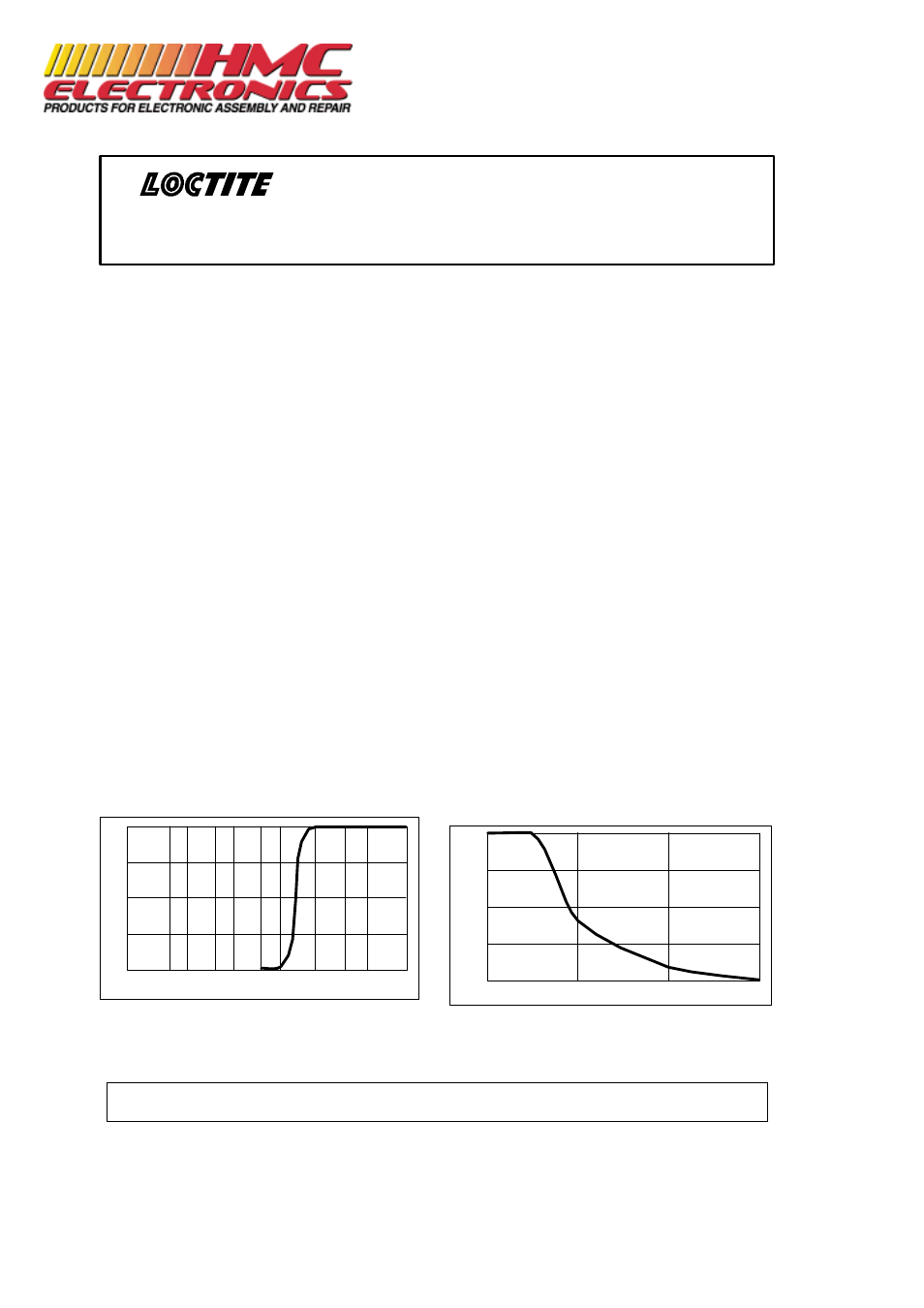
Technical Data Sheet
Rocky Hill, CT 06067-3910
Telephone: (860) 571-5100
1001 Trout Brook Crossing
FAX: (860) 571-5465
NOT FOR PRODUCT SPECIFICATIONS.
THE TECHNICAL DATA CONTAINED HEREIN ARE INTENDED AS REFERENCE ONLY.
PLEASE CONTACT LOCTITE CORPORATION QUALITY DEPARTMENT FOR ASSISTANCE AND RECOMMENDATIONS ON SPECIFICATIONS FOR THIS PRODUCT.
ROCKY HILL, CT FAX: +1 (860)-571-5473 DUBLIN, IRELAND FAX: +353-(1)-451 - 9959
Hysol® Product E-60NC
formerly Durabond E-60NC
Industrial Version, August 2001
PRODUCT DESCRIPTION
LOCTITE
®
Hysol
®
Product E-60NC is a flowable, industrial
grade epoxy potting compound with extended work life. Once
mixed, the two-part epoxy cures at room temperature to form a
rigid, black encapsulant that is non-corrosive to metallic
components on PC Boards and electronic assemblies. The
fully cured epoxy provides excellent environmental and
chemical resistance, and acts as an electrical insulator.
TYPICAL APPLICATIONS
Designed for bonding, potting and encapsulating electrical
components which are sensitive to corrosion. Used in
electronic applications, for component attachment to boards,
housing assembly and potting.
PROPERTIES OF UNCURED MATERIAL
Resin
Typical
Value
Range
Chemical Type
Epoxy
Appearance
Black liquid
Specific Gravity @ 25°C
1.10
1.0 to 1.2
Viscosity @ 25
°
C, mPa.s (cP)
6,200
5,200 to 7,200
Flash Point (TCC),
°
C (
°
F)
>93 (>200)
Hardener
Typical
Value
Range
Chemical Type
Amine
Appearance
Pale yellow liquid
Specific Gravity @ 25°C
1.00
0.9 to 1.1
Viscosity @ 25
°
C, mPa.s (cP)
13,000
12,000 to 14,000
Flash Point (TCC),
°
C (
°
F)
>93 (>200)
Mixture
Typical Value
Appearance
Black Opaque
Specific Gravity @ 25°C
1.05
Mix Ratio (R:H) by Weight
100 to 91
by Volume
1 to 1
TYPICAL CURING PERFORMANCE
Cure speed
The graph below shows the shear strength developed over
time on abraded, acid etched aluminum lap shears with an
average bondline gap of 3 to 9 mils and tested according to
ASTM D-1002.
Cure Time, Hours @25°C
5min 10min 30min 1hr
3hr
6hr
24hr
72hr
0
25
50
75
100
% of Full Strength on Aluminum
1week
1month
Curing Properties
(@ 25
°
C unless noted)
Typical Value
Working Life, minutes
60
Tack Free time, minutes
180
TYPICAL PROPERTIES OF CURED MATERIAL
(@ 25
°
C unless noted)
Physical Properties
Typical Value
Dielectric Strength, Volts/Mil
550
Tensile Strength ASTM D638, psi
6,800
Tensile Elongation ASTM D-638, %
8
Hardness ASTM D-1706, Shore D
85
Glass Transition Temperature, Tg,
°
C
55
PERFORMANCE OF CURED MATERIAL
Shear Strength vs Substrate
(Substrates cured for 5 days @ 22
°
C)
Substrate
Typical Value
Lapshear
N/mm
2
(psi)
Grit-Blasted Steel
18.1
2630
Aluminum (Abraded/Acid Etched, 3 to 9 mil gap)
21.4
3110
Aluminum (Anodized)
7.9
1150
Stainless Steel
7.8
1130
Polycarbonate
5.9
850
Nylon
1.3
190
Wood (Fir)
11.1
1610
Block Shear
N/mm
2
(psi)
PVC
4.6
670
ABS
6.5
940
Epoxy
14.8
2140
Acrylic
1.2
180
Glass
13.9
2020
TYPICAL ENVIRONMENTAL RESISTANCE
Hot Strength
Test procedure :
ASTM D-1002
Substrate:
Abraded, acid etched aluminum
Bondline gap, mils:
3 to 9
Cure procedure:
12 hours at 65
°
C & 4 hours at 22
°
C
Tested at temperature.
0
25
50
75
100
% RT Strength
Temperature, °C
150
100
50
Documentation Provided By HMC Electronics
33 Springdale Ave. Canton, MA 02021
(800) 482-4440