Cadweld, Rail grounding connections – joint head bonds – ERICO CADWELD Rail Grounding Connections – Joint Head Bonds User Manual
Page 2
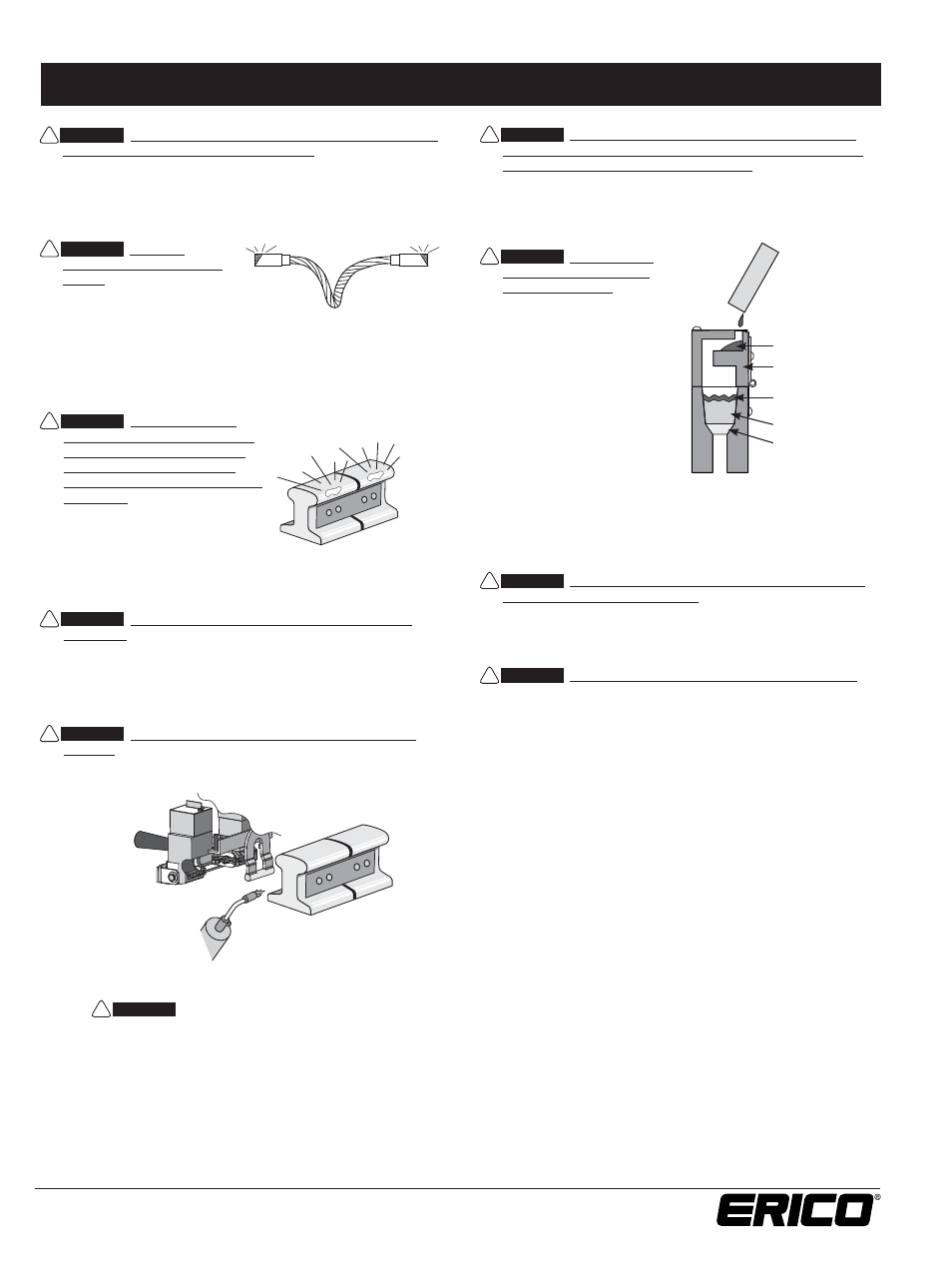
!
WARNING:
The area of the rail where the head bond will be applied
and the bond terminals must be clean and dry. Failure to comply
can cause poor bonding, excessive weld porosity, and/or spewing molten
welding material with the potential for serious burns to the worker.
2. Use abrasive cloth or wire brush on the bond terminals if needed to
remove surface oxidation.
!
CADWELD
®
Rail Grounding Connections – Joint Head Bonds
Refer to the mold tag for applicable instruction sheets.
IPRGJ_B
IPRGJ_B R1074IS10WWEN PUR0312
!
!
!
!
FIGURE 4
CAUTION:
The bond
terminals must have a bright
surface. Failure to comply with
this may result in a less than
optimal weld. See Figure 4.
WARNING:
The area of the rail
head to be bonded must be lightly
ground to a bright fi nish with no
visible scratch marks or gouges
(normal uniform fi nishing marks are
acceptable). Failure to observe this may
result in visible scratches or gouges due
to overly aggressive grinding that are
potential crack initiators and that may
lead to rail breaks causing derailment
accidents with property damage, injury
and death to others. See Figure 5.
3. Lightly grind the rail surface using an ERICO approved grinding wheel
that is self-cleaning or a CADWELD
®
brand Rail Head and Web Cleaner
(Part SBB394C). Grinding wheels with resin binders tend to leave a
surface
fi lm that may contaminate the surface, interfering with the
achievement of an optimum bond and causing weld porosity.
FIGURE 5
FIGURE 6
CAUTION:
Grinding must not be done more than 4 hours prior
to bonding. If the time lapse is longer, suffi cient contaminating rust may
re-form requiring additional grinding. Failure to observe this may result in
a less than optimum bond.
4. Dry the mold and rail by heating them to about 250°F (120°C) with
a small propane torch.
WARNING:
The rail and mold must both be warmed to drive off
moisture. Failure to observe this may result in weld spatter with the
potential for serious burn injury, and a less than optimum bond with
excessive porosity. See Figure 6.
!
!
!
!
WARNING:
Rebonding over the application of an earlier bond is
only permissible in areas of minimal stress such as the head of the
rail within the confi nes of the joint/splice bar! Remove the original
bond by grinding down to a smooth layer of parent rail steel. The new bond
can then be made in the same location as the previous bond. Failure to
observe this may result in a rail break leading to property damage, injury
or death to others.
FIGURE 7
Disk
Welding Material
1/2 Starting Material
Crucible Cover
1/2 Starting Material
CAUTION:
Install only the
specifi ed welding material
in the mold crucible. Use
only the welding material
size that is specifi ed on the
mold. ERICO brand of welding
material (F80) is formulated
specifi cally for use with rail
steels; it is packaged in a blue
tube with a yellow cap. Dump
all of the welding material into
the crucible, then carefully tap
the tube on a hard surface to
loosen the starting material
from the bottom of the tube
and distribute half on top of
the welding material, close
the mold cover, and pour the remainder in the opening of the mold cover.
See Figure 7. Failure to comply may result in diffi culty getting the reaction
started and/or an unacceptable weld.
CAUTION:
Avoid direct eye contact with the “fl ash” of light from
the ignition of the starting material.
5. Position yourself upwind of the mold, on the fi eld side of the rail.
Place the tip of the fl int igniter at the cover opening and ignite.
Remove the igniter quickly to prevent fouling.
CAUTION:
Allow 15 seconds for mold cooling after the reaction.
This will permit the molten metal to solidify. Then carefully disengage
the welder device and pull the mold straight back from the rail. Failure
to observe this may result in mold damage and its premature scrapping.
Molds can generally be re-used up to 50 times.
6. Carefully open the mold cover and break up the slag in the crucible
using the blade of the mold cleaning tool. Dump the slag from the
crucible and remove slag from the taphole using the curved end of
the mold cleaner. Dump slag in the ballast, not onto the ties.
7. Check the molds for breakage or residual slag before proceeding
with the next weld.
Note: If you have any questions or require further instructions, or would
like training, contact ERICO at 1-800-447-7245.
WARNING:
1. Connections should not be made to load bearing rail steel other than at the neutral axis of the rail or at the head of the rail within
the
confi nes of the joint/splice bar.
2. All connections to rail steel should only be made where the rails are fully supported, or to rail that is non-load bearing in its use.
3. The welding material size for the connection to rail steel should not be greater than 250 grams (which, in general, corresponds
to a maximum cable size of 500 kcmil (240 mm
2
).
Copyright ©2010, 2012 ERICO International Corporation. All rights reserved.
CADDY, CADWELD, CRITEC, ERICO, ERIFLEX, ERITECH, and LENTON are registered trademarks of ERICO International Corporation.
www.erico.com
2