Bryant 582A User Manual
Page 8
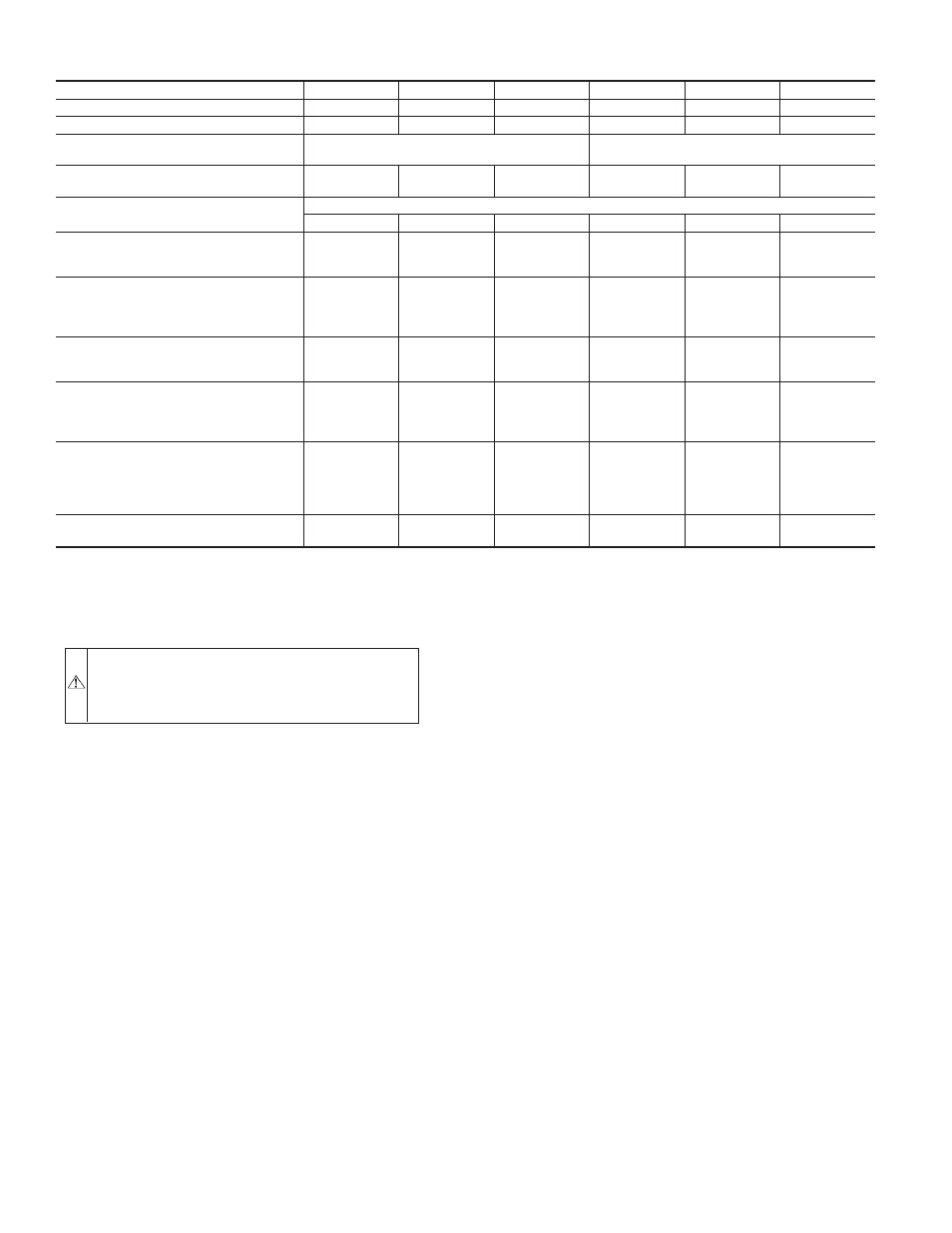
NOTE:
Low NO
x
requirements apply only to natural gas instal-
lations.
CAUTION:
The venting system is designed to ensure
proper venting. The flue hood assembly must be installed
as indicated in this section of the unit installation instruc-
tions.
Install the flue hood as follows:
1. This installation must conform with local building codes
and with the National Fuel Gas Code (NFGC), ANSI
Z223.1 (in Canada, CAN/CGA B149.1, and B149.2) or
NFPA (National Fire Protection Association) latest revi-
sion. Refer to Provincial and local plumbing or wastewater
codes and other applicable local codes.
2. Remove flue hood from shipping location (inside the
blower compartment). Place vent cap assembly over flue
panel. Orient screw holes in vent cap with holes in the flue
panel.
3. Secure flue hood to flue panel by inserting a single screw on
the right side and the left side of the hood.
VIII.
INSTALL GAS PIPING
The gas supply pipe enters the unit through the access hole
provided. The gas connection to the unit is made to the 1/2-in. FPT
gas inlet on the manual shutoff or gas valve.
Install a gas supply line that runs to the heating section. Refer to
Table 3 and the NFGC for gas pipe sizing. Do not use cast-iron
pipe. It is recommended that a black iron pipe is used. Check the
local utility for recommendations concerning existing lines. Size
gas supply piping for 0.5 in. wg maximum pressure drop. Never
use pipe smaller than the 1/2-in. FPT gas inlet on the unit gas
valve.
For natural gas applications, the gas pressure at unit gas connection
must not be less than 4.0 in. wg or greater than 13 in. wg while the
unit is operating. For propane applications, the gas pressure must
not be less than 7.0 in. wg or greater than 13 in. wg at the unit
connection.
An 1/8-in. NPT plugged tapping, accessible for test gage connec-
tion, must be installed immediately upstream of the gas supply
connection to the gas valve.
When installing the gas supply line, observe local codes pertaining
to gas pipe installations. Refer to the NFGC ANSI Z223.1-1988
NFPA latest edition (in Canada, CAN/CGA B149.1, (2)-M86). In
the absence of local building codes, adhere to the following
pertinent recommendations:
1. Avoid low spots in long runs of pipe. Grade all pipe 1/4 in.
in every 15 ft to prevent traps. Grade all horizontal runs
downward to risers. Use risers to connect to heating section
and to meter.
2. Protect all segments of piping system against physical and
thermal damage. Support all piping with appropriate straps,
hangers, etc. Use a minimum of one hanger every 6 ft. For
pipe sizes larger than 1/2 in., follow recommendations of
national codes.
3. Apply joint compound (pipe dope) sparingly and only to
male threads of joint when making pipe connections. Use
only pipe dope that is resistant to action of liquefied
petroleum gases as specified by local and/or national codes.
Never use Teflon tape.
4. Install sediment trap in riser leading to heating section (See
Fig. 9). This drip leg functions as a trap for dirt and
condensate.
5. Install an accessible, external, manual main shutoff valve in
gas supply pipe within 6 ft of heating section.
6. Install ground-joint union close to heating section between
unit manual shutoff and external manual main shut-off
valve.
TABLE 1—PHYSICAL DATA—UNIT 582A (CONTINUED)
UNIT SIZE 582A
048090
048115
048130
060090
060115
060130
NOMINAL CAPACITY (ton)
4
4
4
5
5
5
OPERATING WEIGHT (lb.)
415
415
415
450
450
450
COMPRESSORS
Quantity
Scroll
1
Reciprocating
1
REFRIGERANT (R-22)
Quantity (lb.)
6.0
6.0
6.0
8.0
8.0
8.0
REFRIGERANT METERING DEVICE
Orifice ID (in.)
Acutrol Device
.032
.032
.032
.030
.030
.030
CONDENSER COIL
Rows...Fins/in.
Face Area (sq ft)
1...17
12.3
1...17
12.3
1...17
12.3
2...17
12.3
2...17
12.3
2...17
12.3
CONDENSER FAN
Nominal Cfm
Diameter (in.)
Motor Hp (Rpm)
3600
22
¼ (1100)
3600
22
¼ (1100)
3600
22
¼ (1100)
3600
22
¼ (1100)
3600
22
¼ (1100)
3600
22
¼ (1100)
EVAPORATOR COIL
Rows...Fins/in.
Face Area (sq ft)
3...15
4.7
3...15
4.7
3...15
4.7
4...15
4.7
4...15
4.7
4...15
4.7
EVAPORATOR BLOWER
Nominal Airflow (Cfm)
Size (in.)
Motor Hp (Rpm)
1600
11 X 10
3/4 (1075)
1600
11 X 10
3/4 (1075)
1600
11 X 10
3/4 (1075)
2000
11 X 10
1.0 (1075)
2000
11 X 10
1.0 (1075)
2000
11 X 10
1.0 (1075)
FURNACE SECTION*
Burner Orifice No. (Qty...Drill Size)
Natural Gas
Burner Orifice No. (Qty...Drill Size)
Propane Gas
3...38
3...46
3...33
3...42
3...31
3...41
3...38
3...46
3...33
3...42
3...31
3...41
RETURN-AIR FILTERS (in.)†
Throwaway
24 X 30
24 X 30
24 X 30
24 X 30
24 X 30
24 X 30
* Based on altitude of 0 to 2000 ft.
† Required filter sizes shown are based on the larger of the ARI (Air Conditioning and Refrigeration Institute) rated cooling airflow or the heating airflow velocity of 300
ft/minute for throwaway type or 450 ft/minute for high-capacity type. Air filter pressure drop for non-standard filters must not exceed 0.08 in. wg.
—8—