R82 beverage regulators, Warning – Norgren U.L. Listed Beverage Regulators User Manual
Page 14
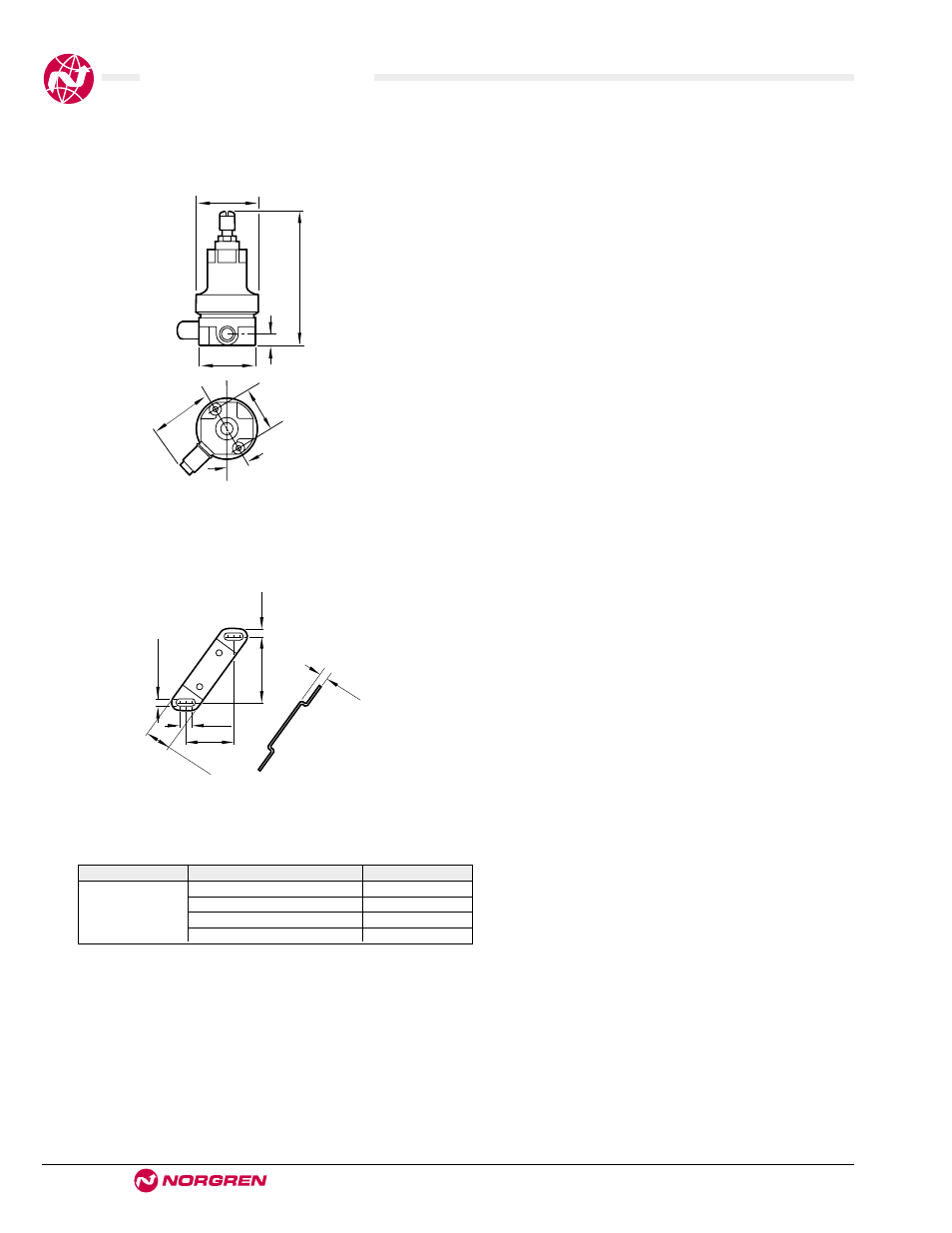
R82 Beverage Regulators
Littleton, CO USA
Phone 303-794-2611
Fax 303-795-9487
ALE-12-14
All Dimensions in Inches (mm)
Mounting Holes (2 Places)
0.18" (4.6 mm) dia. by 0.39" (10 mm) deep.
Use 10-32 thread forming screws.
1.90 (48)
4.75 (121)
2.10 (53)
0.40 (10)
30
°
1.66 (42)
2.07 (53)
R82 Regulator
0.28 (7) Typ
2.75 (70)
0.31 (8)
Typ
2 (51)
1.03 (26)
0.31
(8)
0.5 (13)
5095-51 Strap Type Bracket
Service Kits
Item
Type
Part number
Service kits
Diaphragm, relieving
570-51
Valve cartridge and seal
5086-55
Kit, major
6309-04 *
Relief valve and seal
5779-56 †
* Kit contains diaphragm, slip ring, valve cartridge, and o-rings.
† Relief valve is marked 60 PSIG RELIEF VALVE and has a brass
body with a natural (silver colored) aluminum end cap.
WARNING
Beer dispensing systems must be designed,
installed, and operated in accordance with the
applicable guidelines such as the proposed Section
9.7, Draught Beer Dispensing Equipment and
Related Components (Seventh Draft dated October
17, 1980), of ANSI-ASME F2.1-1975, Food, Drug
and Beverage Equipment or subsequent revisions.
1. Pressure relief valves of sufficient capacity must
always be used in the secondary (outlet) lines
downstream of each pressure regulator, whether
as an integral part of the regulator, as is the case
with Norgren Model R82 Regulator, or separately
installed elsewhere in the outlet lines. Do not
remove or attempt to adjust, plug, block or
otherwise defeat the purpose of the relief valve.
Do not replace a relief valve with any but an
identical model. The relief valve used on the R82
regulator is preset and marked 60 PSIG RELIEF
VALVE. Replace only with the same 60 psig relief
valve, part number 5779-56. The end cap on the
5779-56 relief valve is color coded silver for visual
identification. Failure to provide a pressure relief
valve of sufficient capacity to hold outlet pressure
below the lowest working pressure rating of any
piece of equipment installed in the outlet lines can
result in equipment damage and/or personal
injury.
2. A back flow check valve must always be installed
at the regulator or at each manifold outlet in liquid
dispensing applications to prevent reverse flow
through the regulator and possible introduction of
liquids and other contaminants into the regulator.
3. Regulators must not be used where temperature
or pressure may exceed those specified in the
Technical Data paragraph.
4. The accuracy of the indication of pressure gauges
can change, both during shipment (despite care in
packaging) and during the service life. If a
pressure gauge is to be used in conjunction with
these products and if inaccurate indications may
be hazardous to personnel or property, the gauge
should be calibrated before initial installation and
at regular intervals during use. For gauge
standards refer to ANSI B40.1.
5. These regulators are not intended for use in life
support systems, soft drink carbonator systems,
with soft drink product (syrup) containers, or
industrial cylinder gas systems.