Introduction, Construction features – Graymills Liftkleen L-Series OMI User Manual
Page 5
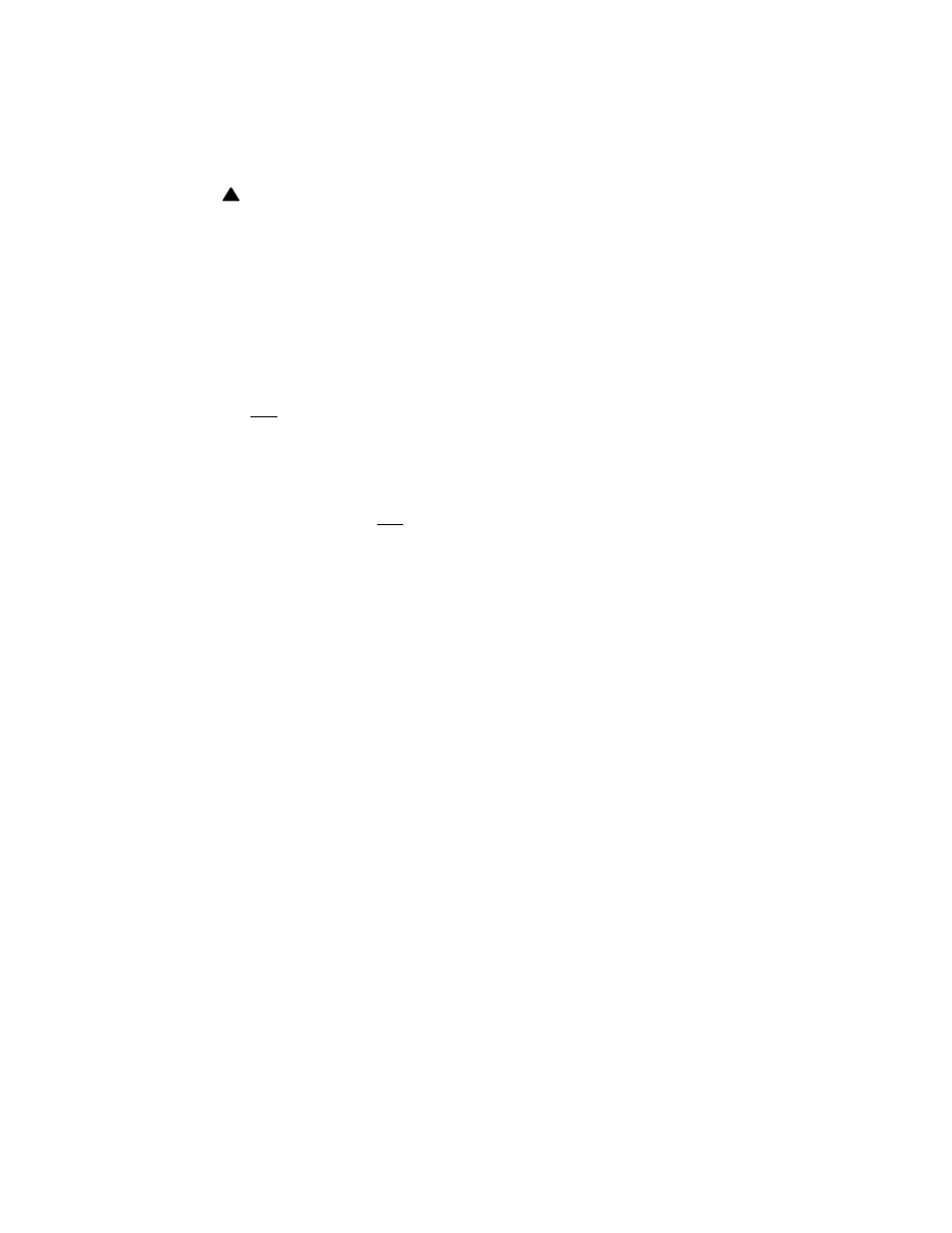
Cleaning solutions may irritate skin and eyes.
If splashed in eyes, flush thoroughly with
water with lids open. Consult Material Safety
Data Sheet (MSDS) and a physician. Always
wear appropriate safety items such as gloves,
apron, safety glasses or goggles.
CAUTION
When cleaning, be sure parts are fully drained
of any flammable or corrosive materials. Even
small amounts could cause a hazardous
situation.
All Liftkleen models are shipped pre-wired and
need only be connected to the proper
electrical supply (see nameplate for electrical
requirements). This is the responsibility of the
customer and should be done by qualified per-
sonnel. Graymills is not responsible for any
damage caused by incorrect supply wiring.
Tanks should be cleaned out on a regular
basis to prevent sludge from building up
around heaters. Failure to do so could result in
damage to the heaters. Graymills is not
responsible for such damage.
INTRODUCTION
The Graymills Liftkleen is a heavy-duty multi-
function, commercial type parts cleaner designed
for both industrial and automotive applications. It
is available for use with either heated aqueous or
solvent cleaning solutions. Seven basic tank sizes
are offered ranging from 170 gallon capacity to
667 gallons in capacity (see Table 1 for
dimensional data). A pneumatic lift platform is
provided on all models.
A number of optional features are available to
tailor the unit to a specific cleaning application.
• Superflo Pumping Unit with an output of up to
10,000 gallons per hour.
• Filtration system for the cleaning solution.
• Roller conveyor platform (instead of standard
grate), loading and unloading conveyors.
• Cleaning cycle and heater timers.
• Anti-Tie Down Device
• Three 4.5 KW electric, immersion type
heaters and insulated tank depending on
model.
• Steam heat
!
CONSTRUCTION FEATURES
The general arrangements of the Models LKR and
LKD Liftkleen assemblies, including optional
features, are shown in Figures 1 and 2. The
following paragraphs describe specific
construction details.
• TANK ASSEMBLY
The Liftkleen was designed to withstand the
rugged demands of heavy-duty industrial and
automotive parts cleaning. The tank is leak-
tested after welding. The bottom of the tank
utilizes double wall construction and is
supported by four channels. Openings are
provided to facilitate moving the Liftkleen with
a fork-lift truck. A 1-1/2” NPT drain is located
in the bottom of the tank to which permanent
drain connections can be attached. An
overflow port is part of the tank assembly and
is intended for use with heated models only.
A water fill port is located in the rear of the
tank (see Figure 8) and consists of 3/4” NPT
pipe nipple. On optional heated models, the
tank sides and cover are insulated with 1”
thick polystyrene foam (equal to two-plus
inches of fiberglass).
• PLATFORM AND LIFTER ASSEMBLY
The Platform and Lifter Assembly are
designed to handle loads specified for the
particular model of Liftkleen (see Table 2).
The platform consists of an angle iron frame
which supports an open steel grate. The lifter
assembly is made up of a channel weldment,
platform support weldment, four support
rollers with needle bearings and hardened
shafts, and a pneumatic cylinder. (Air
consumption data can be found in Table 3).
The rollers and bearings on all Model LKR
and LKD units are located outside the tank
and therefore never immersed in the cleaning
solution. This helps keep moving parts
lubricated. The standard open steel grate of
the platform assembly can be replaced with
the optional roller conveyor platform.
• PUMP ASSEMBLY
The Superflo Pumping Unit Assembly, an
available option on all Model LKR and LKD
units, is capable of providing 10,000 gallons
per hour of flow and provides exceptional
liquid agitation for quicker, more effective
parts cleaning. It is especially effective on
parts containing holes. The pump is a
centrifugal unit and is driven by an electric
motor.
4