Operation, Inspection, Maintenance – COOK Propeller Upblast User Manual
Page 4: Lubricants
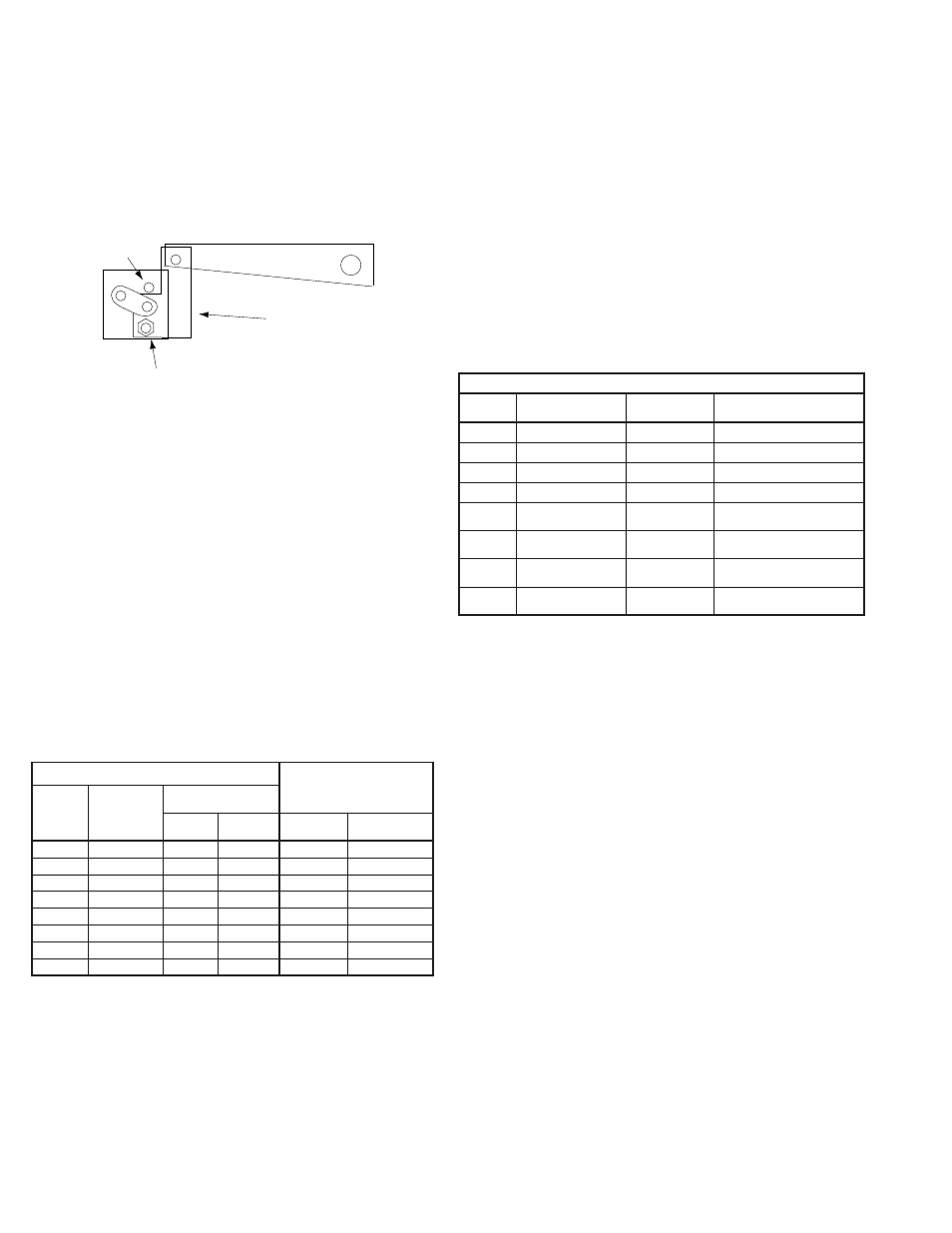
4
TUB
/
SUB
/
SUBH Additional Installation Steps
The damper actuator arms are safety bolted at the factory
to prevent damage or personnel injury during handling and
installation. The bolt must be removed for the damper actu-
ator to operate correctly. Refer to Figure 4.
• Remove Bolt “A” from each of the damper arms.
• Be sure that linkage hook “B” is in contact with bolt “C” to
prevent excessive load on the fusible link.
The damper arms will not operate unless this bolt is
removed. This bolt should be replaced before any mainte-
nance or repair work is started.
Operation
Pre-Start Checks
a. Lock out all the primary and secondary power sources.
b. Inspect fasteners and setscrews, particularly those
used for mounting the unit, and tighten if necessary.
c. Inspect belt tension and pulley alignment. (Remember,
if belt tension is correct, a loud squeal occurs as the fan
increases to full power.)
d. Inspect motor wiring.
e. Ensure the belt touches only the pulleys.
f. Rotate the propeller to ensure it does not rub against the
base.
g. Ensure fan and ductwork are clean and free of debris.
h. Test the fan to ensure the rotation of the propeller is the
same as indicated by the rotation label.
i. Close and secure all access doors.
j. Restore power to unit.
Start Up
Turn the fan on. In variable speed units, set the fan to its
lowest speed. Inspect for the following:
• Direction of rotation.
• Excessive vibration.
• Unusual noise.
• Bearing noise.
• Improper belt alignment or tension (listen for a continu-
ous squealing noise).
Bolt C
Linkage
Bolt A
Figure 4 - SUBH Safety Bolt Removal
Hook B
Recommended Torque for Setscrews/Bolts (IN/LB.)
Setscrews
Hold Down Bolts
Size
Key Hex
Across
Flats
Recommended
Torque
Min.
Max.
Size
Wrench
Torque
No.10
3/32”
28
33
3/8”-16
240
1/4”
1/8”
66
80
1/2”-13
600
5/16”
5/32”
126
156
5/8”-11
1200
3/8”
3/16”
228
275
3/4”-10
2100
7/16”
7/32”
348
384
7/8”- 9
2040
1/2”
1/4”
504
600
1”- 8
3000
5/8”
5/16”
1104
1200
1-1/8” - 7
4200
3/4”
3/8”
1440
1800
1-1/4” - 7
6000
• Improper motor amperage or voltage.
If a problem is discovered, immediately shut off the
fan. Lock out all electrical power and check for the
cause of the trouble. Refer to Troubleshooting, page 6.
Inspection
Inspection of the fan should be conducted at the first 30
minute, 8 hour and 24 hour intervals of satisfactory opera-
tion. During the inspections, stop the fan and inspect as per
the chart below.
30 Minute Interval
Inspect bolts, setscrews, and motor mounting bolts.
Adjust and tighten as necessary.
8 Hour Interval
Inspect belt alignment and tension. Adjust and tighten as
necessary.
24 Hour Interval
Inspect belt tension. Adjust and tighten as necessary.
Maintenance
Establish a schedule for inspecting all parts of the fan.
The frequency of inspection depends on the operating con-
ditions and location of the fan.
Inspect fans exhausting corrosive or contaminated air
within the first month of operation. Fans exhausting con-
taminated air (airborne abrasives) should be inspected
every three months. Clean the propeller and air inlets if
material build-up is excessive. Excessive build-up can
cause imbalance and failure of the propeller.
Regular inspections are recommended for fans exhaust-
ing non-contaminated air.
It is recommended the following inspections be con-
ducted twice per year.
• Inspect bolts and setscrews for tightness. Tighten as
necessary.
• Inspect belt wear and alignment. Replace worn belts
with new belts and adjust alignment as needed. See
Belt and Pulley Installation, page 2.
• Bearings should be inspected as recommended in the
Conditions Chart.
• Inspect for cleanliness. Clean exterior surfaces only.
Removing dust and grease on motor housing assures
proper motor cooling.
Lubricants
Loren Cook Company uses petroleum lubricant in a lith-
ium base conforming to NLGI grade 2 consistency. Other
Conditions Chart
RPM
Temperature
Fan
Status
Greasing
Interval
100
Up to 120°F
Clean
6 to 12 months
500
Up to 150°F
Clean
2 to 6 months
1000
Up to 210°F
Clean
2 weeks to 2 months
1500 Over
210°F
Clean
Weekly
Any
Speed
Up to 150°F
Dirty
1 week to 1 month
Any
Speed
Over 150°F
Dirty
Daily to 2 weeks
Any
Speed
Any Temperature
Very Dirty
Daily to 2 weeks
Any
Speed
Any Temperature
Extreme
Conditions
Daily to 2 weeks