COOK ERV Evaporator Coil Supplement User Manual
Erv evaporator coil supplement, Installation, operation, and maintenance manual, Energy recovery ventilator
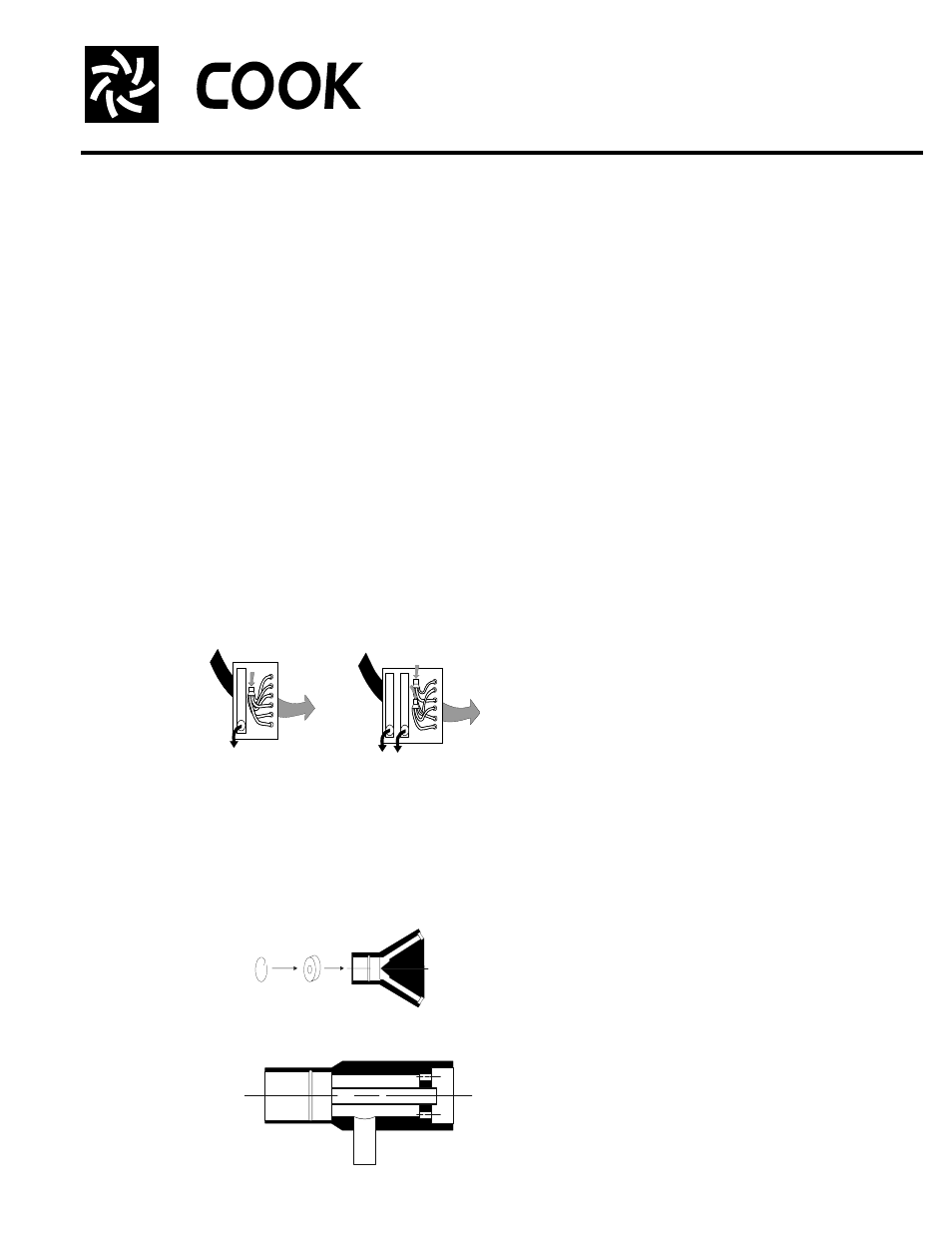
ENERGY RECOVERY VENTILATOR
INSTALLATION, OPERATION, AND MAINTENANCE MANUAL
This publication contains supplemental installation, opera-
tion and maintenance instructions for an ERV-with optional
evaporator coil.
Carefully read this publication and the installation, opera-
tion, and maintenance instruction for standard units of the
ERV- Energy Recovery Ventilators publication prior to any
installation or maintenance procedure.
Loren Cook catalog,
ERV
, provides additional information
describing the equipment, fan performance, available accessories,
and specification data.
For additional safety information, refer to AMCA Publication
410-96,
Safety Practices for Users and Installers of Industrial and
Commercial Fans
.
All of the publications listed above can be obtained from Loren
Cook Company by phoning (417)869-6474, extension 166; by FAX
at (417)832-9431; or by e-mail at [email protected].
For information on special equipment, contact Loren Cook Com-
pany Customer Service Department at (417)869-6474.
Mounting
1.
Position the coil such that the suction header is at the enter-
ing air-side of the coil and the distributor tubes are at the leaving
air-side of the coil. This orientation provides counterflow heat
exchange which is required for proper coil performance.
2.
The suction connection is located at the bottom of the coil
when properly installed.
3.
See Figure 1 - Evaporator Coils.
Coil Types
1.
Model EN
coils are used for
applications where
capacity control is
not required. Sin-
gle or multiple dis-
tributors are available depending on the number of circuits
required. Model EN evaporators utilize dual suction connections
when multiple distributors are used.
2.
EJ coils come with interlaced circuiting. This form of capac-
ity control utilizes two distributors with each feeding every other
tube in the first row of the coil. Each distributor has a separate
suction connection.
Installation
1.
Inspect the
refrigerant distrib-
utor and verify that
the nozzle is in
place. The nozzle
is generally held in
place by a retain-
ing ring or it is an
integral part of the
distributor itself
(see Figure 2 -
Distributor). If a
hot gas bypass kit
was ordered with
the coil, the nozzle
Retainer
Ring
Nozzle
Distributor
Figure 2 - Distributor
Figure 3 - Hot
Gas Bypass Kit
ERV Evaporator Coil Supplement
EN
EJ
Figure 1 - Evaporator Coils
will be located in it rather than the distributor (see Figure 3 - Hot
Gas Bypass Kit).
2.
All field brazing and welding should be performed using high
quality materials and an inert gas purge (such as nitrogen) to
reduce oxidation of the internal surface of the coil.
3.
If a hot gas bypass kit was ordered with the coil install it now.
Complete installation instructions are in the box that contains the
hot gas bypass kit. Align the side port with the hot gas line prior to
brazing into place.
4.
Connect the suction line and suction connection.
5.
Install the expansion valve. Follow the expansion valve manu-
facturer’s recommendations for installation to avoid damaging the
valve. If the valve is externally equalized, use a tubing cutter to cut
off the plugged end of the factory installed equalizer line. Next, use
a de-burring tool to remove any loose metal from the equalizer line
and attach it to the expansion valve. If the valve is internally equal-
ized, the factory installed equalizer line can be left as is or it can be
cut back and sealed.
6.
The expansion valve’s remote sensing bulb should be
securely strapped to the horizontal run of the suction line at the 3 or
9 o’clock position and insulated.
7.
Connect the liquid line to the expansion valve. Pressurize the
coil, expansion valve assembly and suction connection to 100 psig
with dry nitrogen or other suitable gas. The coil should be left pres-
surized for a minimum of 10 minutes.
8.
If the coil holds pressure, the hook-up can be considered leak
free. If the pressure drops by 5 psi or less, repressurize the coil and
wait another 10 minutes. If the pressure drops again, there are
more than likely one or more small leaks, which should be located
and repaired. Pressure losses greater than 5 psi would indicate a
larger leak, which should be isolated and repaired. Be sure to check
valves and fittings as potential sites for leakage or bleed. If the coil
is found to be leaking, contact your local representative. Unautho-
rized repair of the coil may void the coil’s warranty (see warranty
policy on back cover).
9.
Use a vacuum pump to evacuate the coil and any intercon-
necting piping that has been open to atmosphere. Measure the vac-
uum in the piping using a micron gauge located as far from the
pump as possible (the vacuum at the pump will be greater than the
rest of the system). Evacuate the coil to 500 microns or less then
close the valve between the pump and the system. If the vacuum
holds to 500 microns or less for one minute, the system is ready to
be charged or refrigerant pumped down in another portion of the
system can be opened to the coil. A steady rise in microns would
indicate that moisture is still present and that the coil should be fur-
ther vacuumed until the moisture has been removed.
10.
Failure to obtain a high vacuum is indicative of a great deal
of moisture or a small leak. Break the vacuum with a charge of dry
nitrogen or other suitable gas and recheck for leaks (soapy water
works well). If no leaks are found, continue vacuuming the coil until
the desired vacuum is reached.
11.
All field piping must be self-supporting.