Lubrication - fan bearings, Lubrication - motor bearings, Motor services – COOK IMH User Manual
Page 6: Changing shaft speed, Replacing pulleys and belts, Maximum rpm
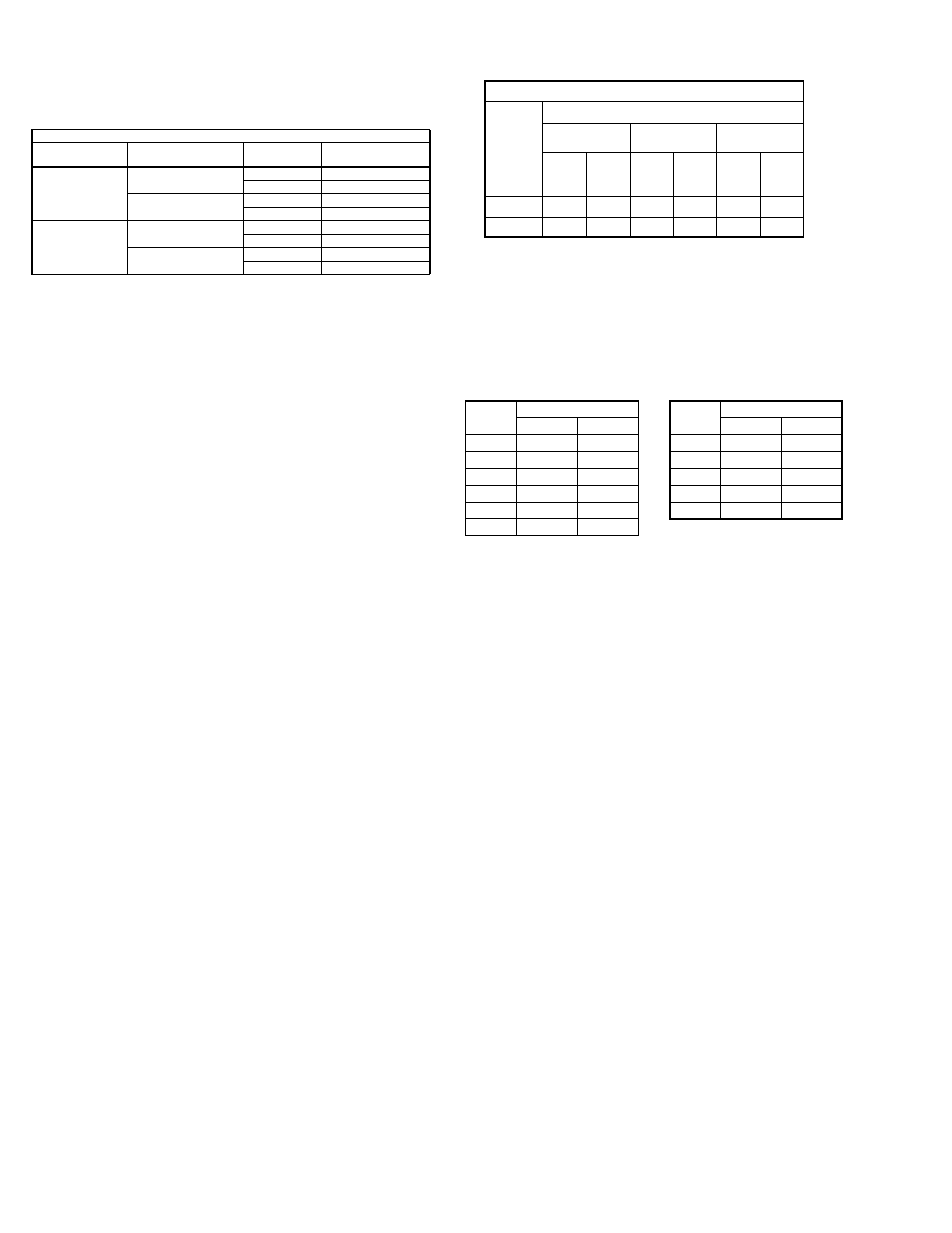
6
Removing dust and grease on motor housing assures
proper motor cooling. Removing dirt from the wheel
and housing prevent imbalance and damage.
Lubrication - Fan Bearings
Greasable fan bearings are lubricated through a grease
fitting on the bearing and should be lubricated by the
schedule, Conditions Chart.
For best results, lubricate the bearing while the fan is in
operation. Pump grease in slowly until a slight bead forms
around the bearing seals. Excessive grease can burst
seals thus reducing bearing life.
In the event the bearing cannot be seen, use no more
than three injections with a hand-operated grease gun.
Before lubricating, the grease nipple and immediate
vicinity should be thoroughly cleaned without the use of
high pressure equipment. The grease should be supplied
slowly as the bearing rotates until fresh grease slips past
the seal.
Excessive pressure should be avoided to prevent seal
damage.
Exceptions to the greasing interval chart:
• Periodic Applications (any break of one week or
more): it is recommended that full lubrication be performed
prior to each break in operation.
• Higher Temperature: it is recommended to halve the
intervals for every 30
°F increase in operating temperature
above 120
°F not to exceed 230°F for standard bearings;
High Temperature bearings (optional) can operate up to
400
°F.
• Vertical Shaft: it is recommended that the intervals
should be halved.
Loren Cook Company uses petroleum lubricant in a lith-
ium base. Other types of grease should not be used unless
the bearings and lines have been flushed clean. If another
type of grease is used, it should be a lithium-based grease
conforming to NLGI grade 2 consistency.
A NLGI grade 2 grease is a light viscosity, low-torque,
rust-inhibiting lubricant that is water resistant. Its tempera-
ture range is from -30
°F to +200°F and capable of intermit-
tent highs of +250
°F. For temperatures above 250°F
Mobiltemp SHC 32 is recommended.
Lubrication - Motor Bearings
Motors are provided with prelubricated bearings. Any
lubrication instructions shown on the motor nameplate
supersede instructions below.
Motor bearings without provisions for relubrication will
operate up to 10 years under normal conditions with no
maintenance. In severe applications, high temperatures or
excessive contaminates, it is advisable to have the mainte-
nance department disassemble and lubricate the bearings
after 3 years of operation to prevent interruption of service.
For motors with provisions for relubrication, follow inter-
vals of the table below.
Motors are provided with a polyurea mineral oil NGLI #2
grease. All additions to the motor bearings are to be with
a compatable grease such as Exxon Mobil Polyrex EM
and Chevron SRI.
The above intervals should be reduced to half for verti-
cal shaft installations.
Motor Services
Should the motor prove defective within a one-year
period, contact your local Loren Cook representative or
your nearest authorized electric motor service represen-
tative.
Changing Shaft Speed
All belt driven fans with motors up to and including 5 HP
(184T max.) are equipped with variable pitch pulleys. To
change the fan speed, perform the following:
a. Loosen setscrew on driver (motor) pulley and
remove key, if equipped.
b. Turn the pulley rim to open or close the groove fac-
ing. If the pulley has multiple grooves, all must be
adjusted to the same width.
c. After adjustment, inspect for proper belt tension.
Speed Reduction
Open the pulley in order that the belt rides deeper in
the groove (smaller pitch diameter).
Speed Increase
Close the pulley in order that the belt rides higher in
the groove (larger pitch diameter). Ensure that the
RPM limits of the fan and the horsepower limits of the
motor are maintained.
Replacing Pulleys and Belts
a. Remove pulleys from their respective shafts.
b. Clean the motor and fan shafts.
c. Clean bores of pulleys and coat the bores with heavy
oil.
d. Remove grease, rust, or burrs from the pulleys and
shafts.
Relubrication Intervals
Service
Conditions
NEMA Frame Size
Up to and
including 184T
213T-365T
404T and larger
1800 RPM
and less
Over
1800 RPM
1800 RPM
and less
Over
1800 RPM
1800 RPM
and less
Over
1800 RPM
Standard
3 yrs.
6 months
2 yrs.
6 months
1 yr.
3 months
Severe
1 yr.
3 months
1 yr.
3 months
6 months
1 months
Maximum RPM
Unless otherwise noted wheel construction for standard duty and heavy duty
is the same. *Standard duty, **Heavy duty
Unit
Size
Maximum RPM
Unit
Size
Maximum RPM
SD*
HD**
SD*
HD**
70
3742
6236
190
1389
2315
90
2934
4889
210
1256
2093
110
2397
3994
230
1146
1910
130
2026
3377
260
1016
1693
150
1755
2924
290
908
1513
170
1547
2579
Lubrication Conditions Chart
Fan Class
Fan Status
Shaft Size
Maximum Interval
(operational hrs)
Standard Duty
Normal Conditions
(Clean, Dry & Smooth)
> 2”
7,500
< 2”
1,000
Extreme Conditions
(Dirty/Wet/Rough)
> 2”
1,500
< 2”
200
Heavy Duty
Normal Conditions
(Clean, Dry & Smooth)
> 2”
3,000
< 2”
500
Extreme Conditions
(Dirty/Wet/Rough)
> 2”
500
< 2”
100