Operation – COOK ERV User Manual
Page 9
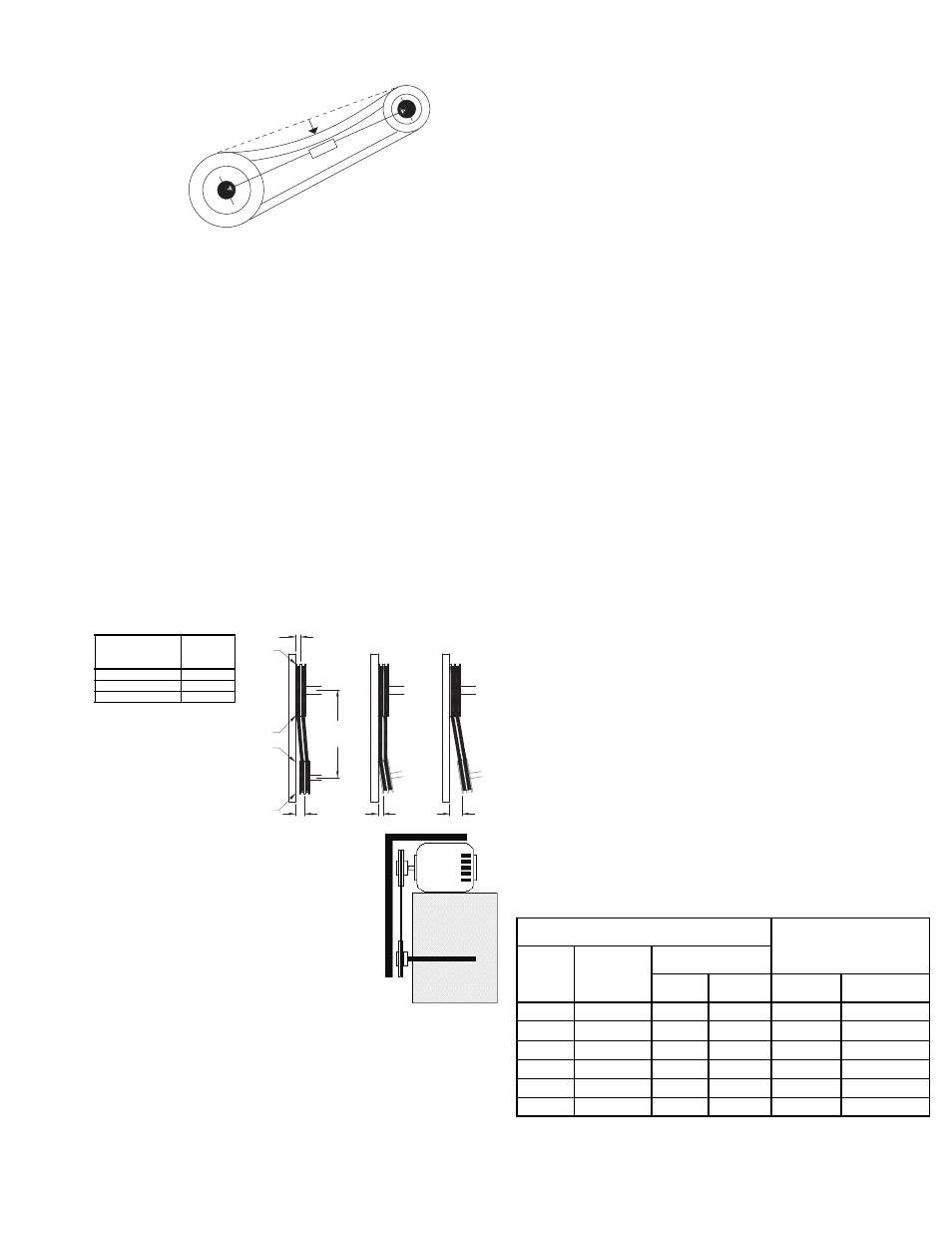
9
1 foot
1/4 inch
Belt and Pulley Installation
Belt tension is determined by the sound the belts make
when the fan is first started. Belts will produce a loud squeal
which dissipates after the fan is operating at full capacity. If
the belt tension is too tight or too loose, lost efficiency and
possible damage can occur.
Do not change the pulley pitch diameter to change ten-
sion. This will result in a different fan speed than desired.
a. Loosen motor plate adjustment screw and move motor
plate in order that the belts can easily slip into the
grooves on the pulleys. Never pry, roll, or force the
belts over the rim of the pulley.
b. Slide the motor plate back until proper tension is
reached. For proper tension a deflection of approxi-
mately 1/4” per foot of center distance should be
obtained by firmly pressing the belt. Refer to Figure 1.
c. Lock the motor plate adjustment nuts in place.
d. Ensure pulleys are properly aligned. Refer to Figure 2.
Pulley Alignment
Pulley alignment is
adjusted by loosening
the motor pulley set-
screw and by moving the
motor pulley on the motor shaft.
Figure 2 indicates where to measure the
allowable gap for the drive alignment toler-
ance. All contact points (indicated by
WXYZ) are to have a gap less than the tol-
erance shown in the table. When the pul-
leys are not the same width, the allowable
gap must be adjusted by half of the differ-
ence in width (As shown in A & B of Figure
2). Figure 3 illustrates using a carpenter’s
square to adjust the position of the motor pulley until the
belt is parallel to the longer leg of the square.
Final Installation Steps
a. Inspect fasteners and setscrews, particularly fan
mounting and bearing fasteners, and tighten accord-
ing to the recommended torque shown in the table
Recommended Torque for Setscrews/Bolts.
b. Inspect for correct voltage with voltmeter.
c. Ensure all accessories are installed.
d. If applicable, ensure fan is secured to ductwork.
Operation
Pre-Start Checks
a. Lock out all the primary and secondary power
sources.
b. Ensure fasteners and setscrews, particularly those
used for mounting the fan, are tightened.
c. Inspect belt tension and pulley alignment on blowers.
d. Inspect belt tension on energy wheel drive belt.
e. Inspect motor wiring.
f. Ensure belt touches only the pulleys.
g. Ensure fan and ductwork are clean and free of debris.
h.Ensure rotor moves freely by hand. If not, recheck the
seal to determine whether or not it is binding and if so
adjust seals following the sealcheck instructions.
i. Ensure motor rotation is correct by detaching the belts
from the drive sheave and bumping the motor. The
sheave should be rotating in the direction such that the
belt will result in rotation per the exterior markings. If
not, rewire the motor.
j. Ensure the air flow orientation matches up to design by
looking at the identification markings on the cassette
and/or refer to the general arrangement drawing to
check the four duct connections to the unit.
k. Close and secure all access doors.
l. Restore power to the fan.
Changing Fan Speed
The motor/blower combinations on ERV sizes 1500 and
up are equipped with variable pitch pulleys. To change the
fan speed, perform the following:
a. Loosen setscrew on driver (motor) pulley and remove
key, if equipped.
b. Turn the pulley rim to open or close the groove facing.
If the pulley has multiple grooves, all must be adjusted
to the same width.
c. After adjustment, inspect for proper belt tension.
Speed Reduction
Open the pulley in order that the belt rides deeper in
the groove (smaller pitch diameter).
Speed Increase
Close the pulley in order that the belt rides higher in the
groove (larger pitch diameter). Ensure that the RPM limits
of the fan and the horsepower limits of the motor are main-
tained.
Figure 2
Figure 3
Figure 1
OFFSET
ANGULAR
OFFSET/ANGULAR
A
W
X
Y
Z
B
CENTER
DISTANCE
(CD)
GAP
GAP
Tolerance
Center Distance
Maximum
Gap
Up thru 12”
1/16”
12” up through 48
1/8”
Over 48”
1/4”
Recommended Torque for Setscrews/Bolts (IN/Lb)
Setscrews
Hold Down Bolts
Size
Key Hex
Across
Flats
Recommended
Torque
Min.
Max.
Size
Wrench
Torque
No.10
3/32”
28
33
3/8”-16
240
1/4”
1/8”
66
80
1/2”-13
600
5/16”
5/32”
126
156
5/8”-11
1200
3/8”
3/16”
228
275
3/4”-10
2100
7/16”
7/32”
348
384
7/8”- 9
2040
1/2”
1/4”
504
600
1”- 8
3000