Campbell Scientific 4WFBS120, 4WFBS350, 4WFBS1K 4 Wire Full Bridge Terminal Input Modules User Manual
Page 12
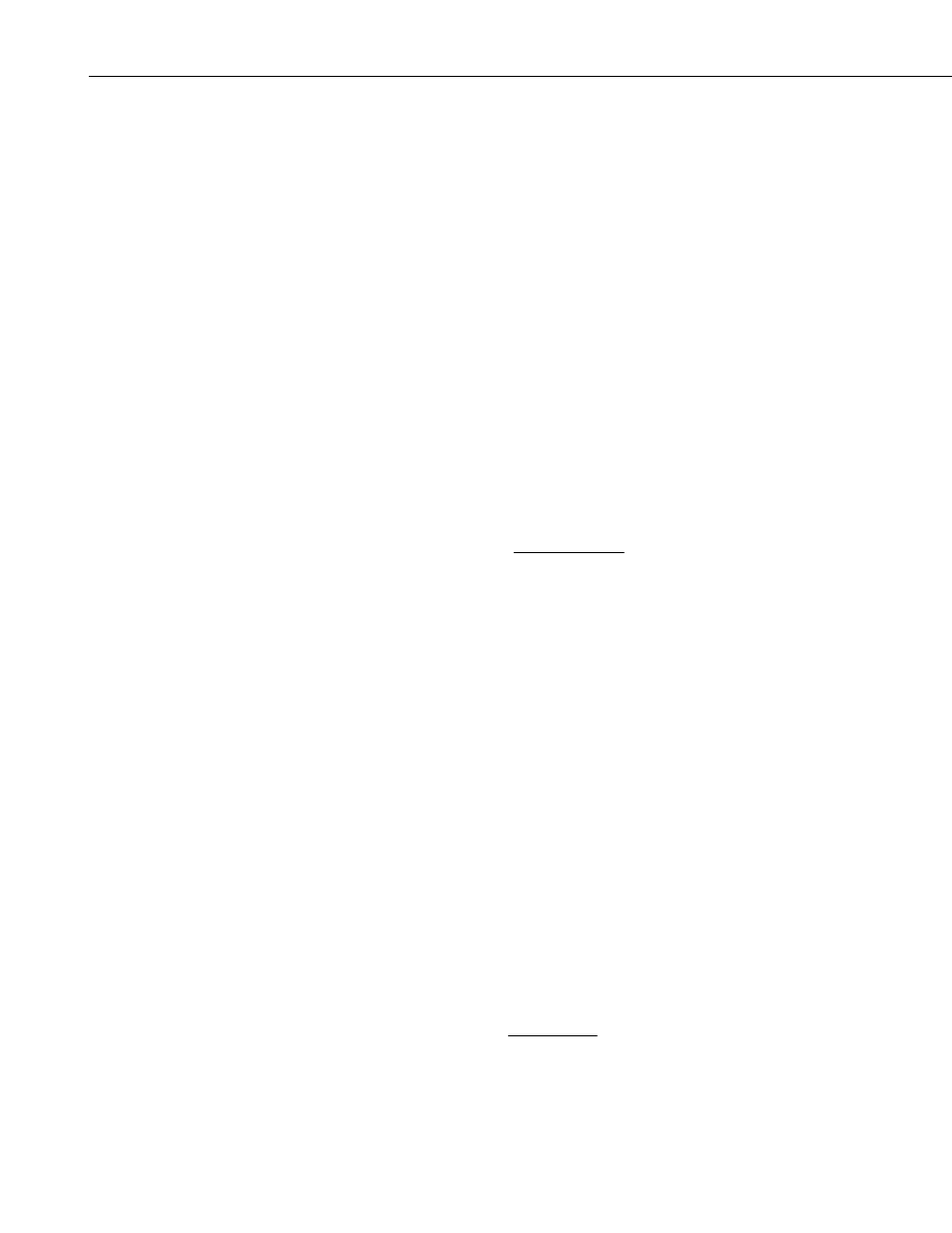
4WFBS120, 4WFBS350, 4WFBS1K 4 Wire Full Bridge Terminal Input Modules (TIM)
Although this requires a 4WFBS module for each strain gage, it is important
because placing relays internal a Wheatstone bridge strain system is
discouraged. Any change in resistance of the multiplexer’s relay contacts
would result in a corresponding change in the bridge’s output voltage.
Changes in contact resistance can be induced by temperature fluctuations,
oxidation, environmental conditions, and normal wear of contact surfaces. The
specification for the relays that are used in our multiplexers state that initial
contact resistance will be less than 100 milliohms (AM16/32B). There is not a
specification for change in contact resistance for the relays because there are so
many variables that affect contact resistance. Test reports exist for various test
conditions that show contact resistance changing over time by 10 to 20 milli-
Ohms. These tests were performed using static test temperatures, so it is safe
to assume that real world conditions would result in larger resistance shifts.
When strain gauges are used in the Wheatstone bridge, small changes in
contact resistance result in large apparent strains. To understand the error that
can be introduced from allowing the relay contacts to be internal of the
Wheatstone bridge, let us assume that the two relays carrying the current from
the strain gage vary by 20 milliohms (40 milliohm total variance or ΔR
G
= 40
mΩ ). Inserting this into equation 3.3, using a 120 ohm strain gage with a gage
factor of 2 results in an apparent strain of about 167
με.
(
)
Ω
×
=
120
2
167
με
V
out
ex
/
Ω
Ч
Ч
04
.
0
10
1
6
4.1.2 Quarter Bridge Strain with 3 Wire Element Calculations
As noted in Section 3, in real life applications the Wheatstone bridge starts out
unbalanced. The strain gauge is never perfectly at its nominal resistance even
prior to installation. The installation process can lead to even more deviation
from this nominal state. In addition, lead resistance can cause an initial
apparent strain reading. To remove this initial offset, a zero measurement can
be made with the gauge installed. This zero measurement can be incorporated
into the datalogger program and subsequent measurements can report strain
relative to this zero basis point.
Strain is calculated in terms of the result of the full bridge measurement. This
result is the measured bridge output voltage divided by the bridge excitation
voltage
V
. (The actual result of the full bridge instruction is the
millivolts output per volt of excitation,
1000
⋅V
out
/ V
ex
) The result of the zero
measurement,
1000
0
⋅V
V
out
ex
/
can be stored and used to calculate future
strain measurements. The change in the full bridge measurement from the zero
state, V
r
, is used in the calculation of the strain.
V
V
V
V
V
r
out
ex
out
ex
=
−
(
/
) (
/
)
0
4.1.1
Using V
r
from equation 4.1.1, the strain is calculated using equation 4.1.2.
ε
=
−
4
1 2
V
GF
V
r
r
(
)
4.1.2
The calculations are covered in more detail in Section 4.5.
6