Cutting data considerations, Wet or dry machining – Sandvik Coromant Threading User Manual
Page 43
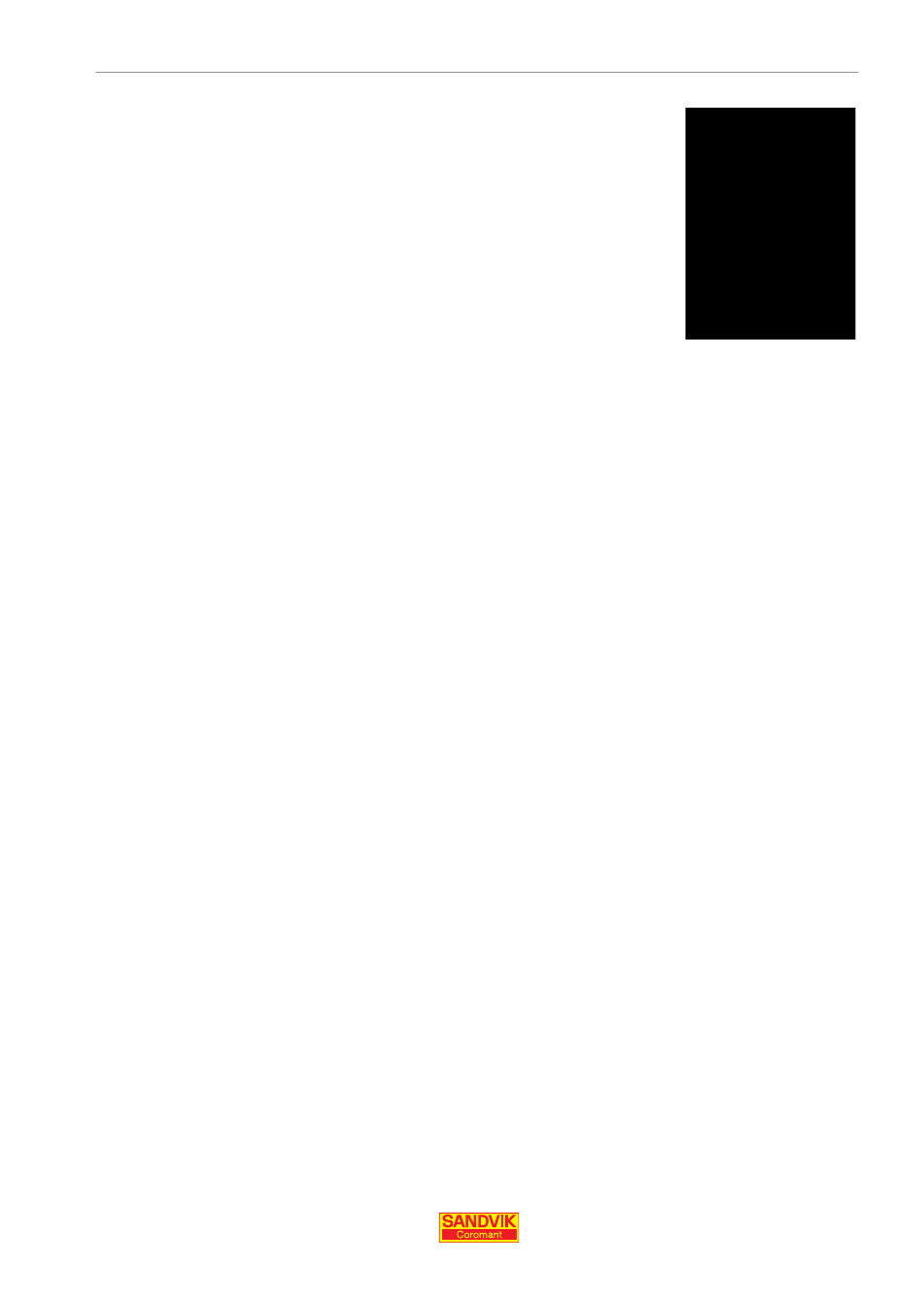
43
2. Applications – Thread milling
Cutting data considerations
• In internal applications, a
e
is increased relative to straight cutting,
which reduces the chip thinning effect.
• In external applications, the radial depth becomes much smaller
and a higher cutting speed can be used.
• CoroMill® Plura cutters have a larger surface contact area than
end mills of equal length, and often a less favourable length-
to-diameter ratio. This can be compensated by reducing a
e
and
performing one or two extra passes.
• Conventional end mills and CoroMill Plura thread milling cutters
can use the same cutting speed.
• For CoroMill 327 and CoroMill 328, use the general recommenda-
tions for grooving and slotting.
• The entering angle for the nose radius is 90°. Since this is the
most sensitive part of the insert, h
ex
calculations should be made
using entering angle 90°.
For cutting data and values see chapter 5, Technical reference
(page 88) or use the Sandvik Coromant threading calculator/Plu-
raGuide.
Wet or dry machining
Machining dry is always recommended as cutting fl uid emphasizes
temperature variations at entry and exit, creating thermal cracks.
Cutting fl uid can be benefi cial on certain occasions, such as when
fi nishing stainless steels/aluminium, machining HRSA or machin-
ing cast iron (to reduce toxic dust). However, it is most benefi cial to
evacuate chips using compressed air.