Dwyer 8B User Manual
Page 14
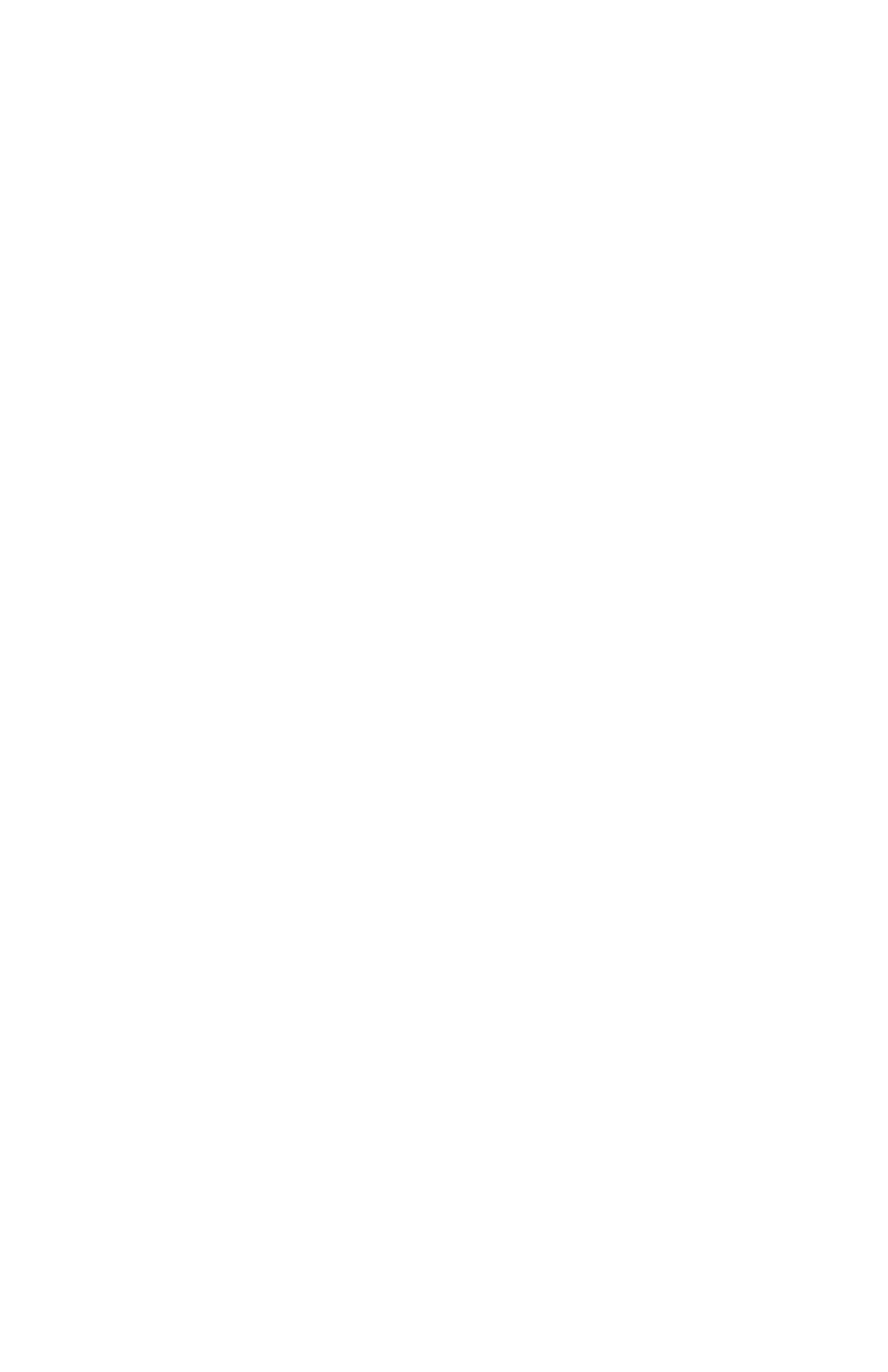
Page 14
PROGRAMMING AND OPERATION FOR PID
Theory of Operation
The PID method of control is based on the individual tuning of proportional band values,
integral time values, and derivative time values to help a unit automatically compensate for
changes in a control system. The proportional band is the range around the set point in
which the control’s proportioning takes place. The control increases or decreases the output
proportionately to the process temperature’s deviation from the set point. The integral time
eliminates undershoot and overshoot of the set point by adjusting the proportioning control
based on the amount of deviation from the set point during steady state operation. The
derivative time eliminates undershoot and overshoot by adjusting the proportioning control
based on the rate of rise or fall of the process temperature. The integral deviation offset
correction (ioFn) improves the speed in which the process value reaches the set point value.
If this parameter is set to zero, the output will be zero when the process value is equal to the
set point value. If the integral time parameter is used only to eliminate steady state error, it
may take a long time to reach the set point because it needs time to accumulate the error.
This parameter defines the default output level on start up. When the integral time is set at
0, then the proportional derivative offset correction (PdofF) would replace the integral
deviation offset correction, but serves the same function.
Program Set Up
In order to use the PID function in the B series controllers, the Control Mode will have to be
set to PID in the Initial Setting Menu. After changing the Control Mode, the PID parameters
can be accessed in the Regulation Menu. The PID parameters can either be programmed
manually or they can be set by the controller using the auto tune function. The auto tune will
use trial and error to tune the PID parameters to give the control the most precise control.
Since the time to accurately tune the control may differ depending on the process, the
controller can also be manually tuned to known PID values prior to running auto tune. The
Run/Stop parameter must be set to run in order to start auto tuning.
The B series controller has four user-defined profiles (PID0 to PID3) of PID values along with
an auto selection function (PID4). Each set of PID values includes a set point value (Svn),
proportional band (Pn), integral time (in), derivative time (dn), and integral deviation setting
(iofn). If PID4 is selected, the controller will pick which set of user defined parameters to use
based on how close the set point value of the profile is to the current process value.