0 rs-485 protocol, Rs-485 protocol – Detcon 1000_CO2 User Manual
Page 23
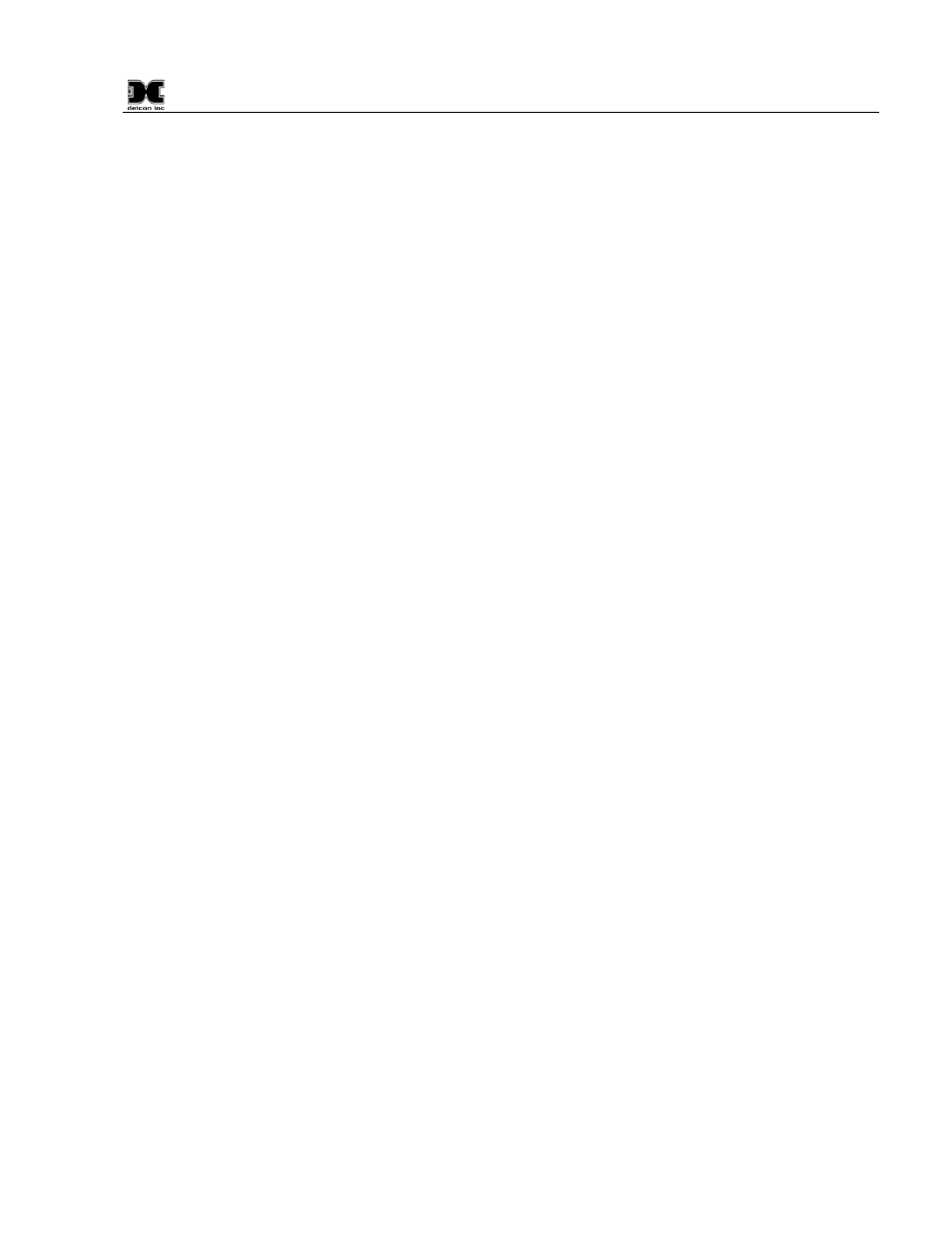
Model 1000 CO2
Model 1000 CO2 Instruction Manual
Rev. 2.2
Page 19 of 28
The following conditions will cause a calibration fault:
1 - Zero calibration cannot converge.
2 - Auto span cannot converge (too noisy or too unstable).
3 - Span gas is not applied before 1 minute elapses.
Fail-Safe/Fault Supervision
Model IR-640/IR-642 MicroSafe™ sensors are programmed for fail-safe operation. All of the fault conditions
listed below will activate the fault relay, illuminate the fault LED, cause the mA output to drop to zero (0mA),
and cause the display to read its corresponding fault condition.
Memory Error
If the processor can’t save values to memory, the display will indicate: “MEMORY ERROR”.
Zero Fault
If the sensor should drift below -10% of range, the display will indicate: “ZERO FAULT”.
Lamp Fault
If the lamp signal is lost, the display will indicate: “LAMP FAULT.2”.
Reference Peak High Fault
If the reference peak signal is too high (>3600), the display will indicate: “SIGNAL FAULT.31”.
Active Peak High Fault
If the active peak signal is too high (>3600), the display will indicate: “SIGNAL FAULT.32”.
Reference Peak Low Fault
If the reference peak signal is too low (<500), the display will indicate: “SIGNAL FAULT.41”.
Active Peak Low Fault
If the active peak signal is too low (<500), the display will indicate: “SIGNAL FAULT.42”.
Reference Peak to Peak Low Fault
If the reference peak to peak signal is too low (<200), the display will indicate: “SIGNAL FAULT.51”.
Active Peak to Peak Low Fault
If the active peak to peak signal is too low (<200), the display will indicate: “SIGNAL FAULT.52”.
10.0 RS-485 Protocol
Detcon MicroSafe™ sensors feature Modbus™ compatible communications protocol and are addressable via
rotary dipswitches for multi-point communications. Other protocols are available. Contact the Detcon factory
for specific protocol requirements. Communication is two wire, half duplex 485, 9600 baud, 8 data bits, 1 stop
bit, no parity, with the sensor set up as a slave device. A master controller up to 4000 feet away can
theoretically poll up to 256 different sensors. This number may not be realistic in harsh environments where
noise and/or wiring conditions would make it impractical to place so many devices on the same pair of wires.
If a multi-point system is being utilized, each sensor should be set for a different address. Typical address
settings are: 01, 02, 03, 04, 05, 06, 07, 08, 09, 0A, 0B, 0C, 0D, 0E, 0F, 10, 11, etc.
In most instances, RS-485 ID numbers are factory set or set during installation before commissioning. If
required, the RS-485 ID number can be set via rotary dipswitches located on the preamp circuit board.