Star Water Systems VPH SERIES User Manual
Page 4
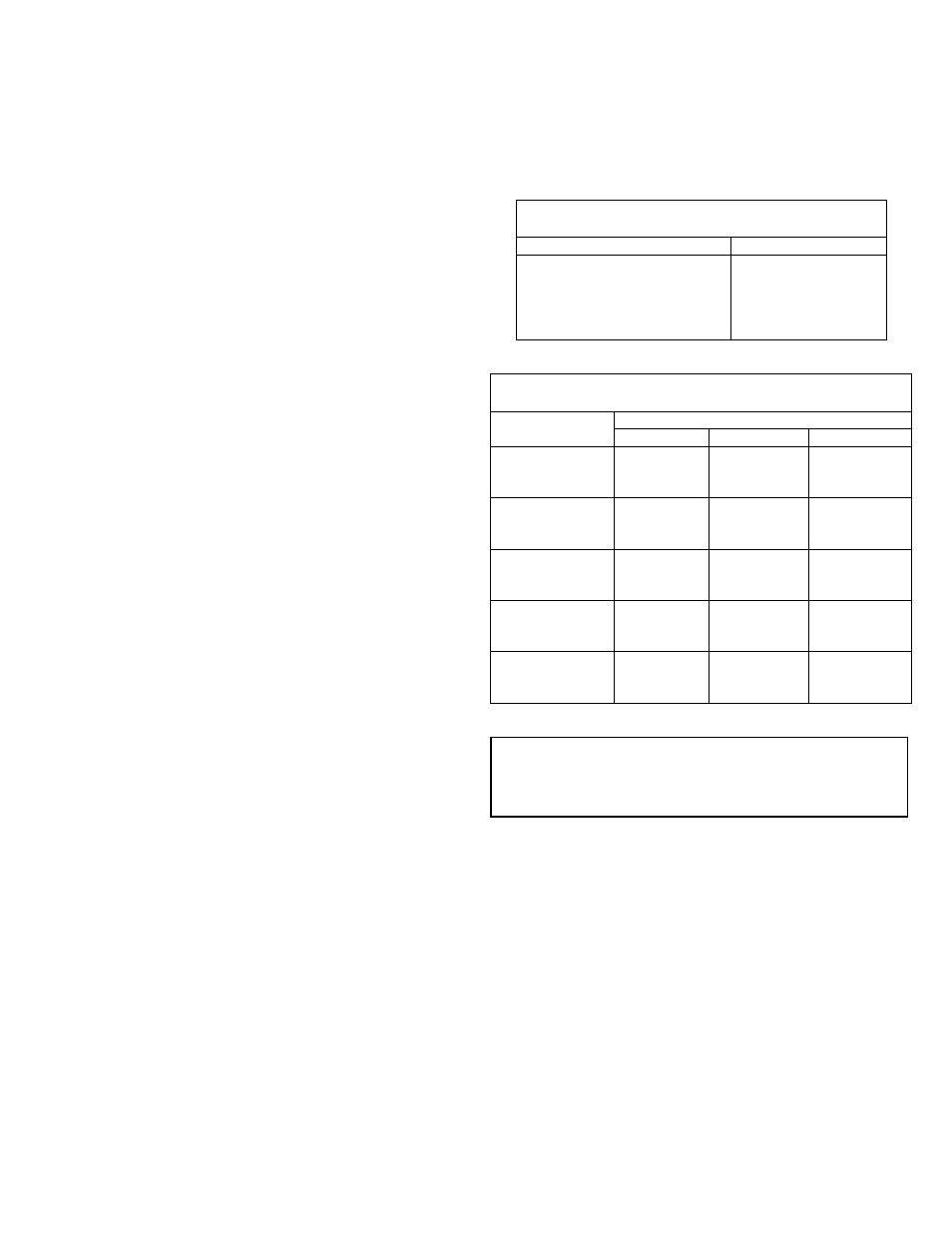
4
95 North Oak Street • Kendallville, IN 46755 • 260-347-1600 © Copyright 2013. All rights reserved.
II. Deep Well (Single Pipe System)
Application - Where the inside diameter of well is 2, 2-1/2 or
3 inches (See Illustration A & B).
A. Attach foot valve directly to bottom of ejector assembly
(tail pipe not used on single pipe installations). Ejector
is to be submerged 10 to 15 feet below pumping water
level, making certain foot valve is at least five feet from
bottom of well.
B. Attach foot valve and packer ejector to suction pipe
(presoak packer leathers for approximately two hours).
Start the assembly down the well. Some force may be
required to push the packer down the casing.
C. As each section is lowered, check for leaks by pouring
water into the suction pipe.
D. Attach well adapter to suction pipe, lower over casing top
and tighten adapter flange.
E. If pump is offset from the well, run suction and pressure
pipes from well to pump, using piping of the same
diameter as the suction tapping (1-1/4”) and pressure
tapping (1” of the pump. For long offset distances, refer
to Chart I for the proper pipe size.
F. Unions in suction and discharge piping near pump and
well will aid in servicing. Leave enough surrounding
room so that wrenches can be used without difficulty.
III. Pressure Tank Hook Up
A. Standard vertical pressure tanks require an air volume
control to ensure the proper air-to-water ratio in
the pressure tank. The air volume control tubing is
connected to the 1/4” tapping on the pump case (see
Illustration E).
B. Air-E-Tainer tanks are equipped with a diaphragm or
bladder that keeps the air and water from mixing. Since
these tanks are factory precharged with air, an air
volume control is not required.
C. On vertical tank installations, galvanized steel or plastic
pipe can be used to connect the pump to the tank. To
assist in servicing, place shut-off valve and union in line
between pump and tank (See Illustration E).
D.
DO NOT install a check valve between pump and
pressure tank. This will cause the pressure switch to
malfunction.
IV. Wiring
A. All jet pump motors are suitable for use with 60 cycle
A.C. current only. Pumps with 3/4 thru 1-1/2 HP motors
are connected for 230 volt service.
B. All pumps (3/4 thru 1-1/2 HP) are dual voltage and may
be field connected for either 115 or 230 volt service.
C. Check the motor nameplate diagram if a voltage change
is required. Always use the higher voltage when
possible.
Your pump motor has built-in thermal overload that protects
the motor against burnout from overload of low voltage,
high voltage and other causes. The device is automatic
and resets itself once the temperature has dropped to a
safe point. Frequent tripping of the device indicates trouble
in the motor or power lines, and immediate attention is
needed. The device should never be tampered with, and
unless trouble is located and corrected, motor failure can
eventually be expected.
CHART II-A
RECOMMENDED WIRE AND FUSE SIZES
MAX. FUSE CAPACITY
WIRE GAUGE
15A
20A
30A
45A
60A
14
12
10
8
6
CHART II-B
RECOMMENDED WIRE SIZES
Distance From
Motor To Meter
HP Rating of Single Phase Motors
3/4
1
1-1/2
0-50’
115V
230V
12 GA
14 GA
12 GA
14 GA
12 GA
14 GA
50-100’
115V
230V
12 GA
14 GA
12 GA
14 GA
12 GA
14 GA
100-150’
115V
230V
12 GA
14 GA
10 GA
14 GA
10 GA
12 GA
150-200’
115V
230V
10 GA
14 GA
10 GA
12 GA
8 GA
12 GA
200-300’
115V
230V
8 GA
14 GA
8 GA
12 GA
6 GA
10 GA
CAUTION: Never examine, make wiring changes or
touch the motor before disconnecting the main elec-
trical supply switch. The thermal device may have
opened the electrical circuit.
D. Undersize wiring can cause motor failure (low voltage),
frequent cutout of motor overload protector, television
interference and even fire. Make certain the wiring
is adequately sized (Chart II-B), well insulated and
connected to a separate circuit outside the house in case
of fire. For added safety, the pump and motor should be
securely grounded to the well casing or to a separate
ground rod driven eight feet into the ground. Consult
local codes before attempting a wiring installation.
NOTE: Charts II-A and II-B assume copper wire to be
installed.
E. When fusing the pump service entrance box, consult
Chart II-A for proper fuse size. Use only the fuse that is
stipulated for your particular installation. Never use one
larger. Service should never be reinstated to the pump
motor by attempting to circumvent a blown fuse by any
other means.