Ramsey Winch RPH-30000T-117 User Manual
Page 15
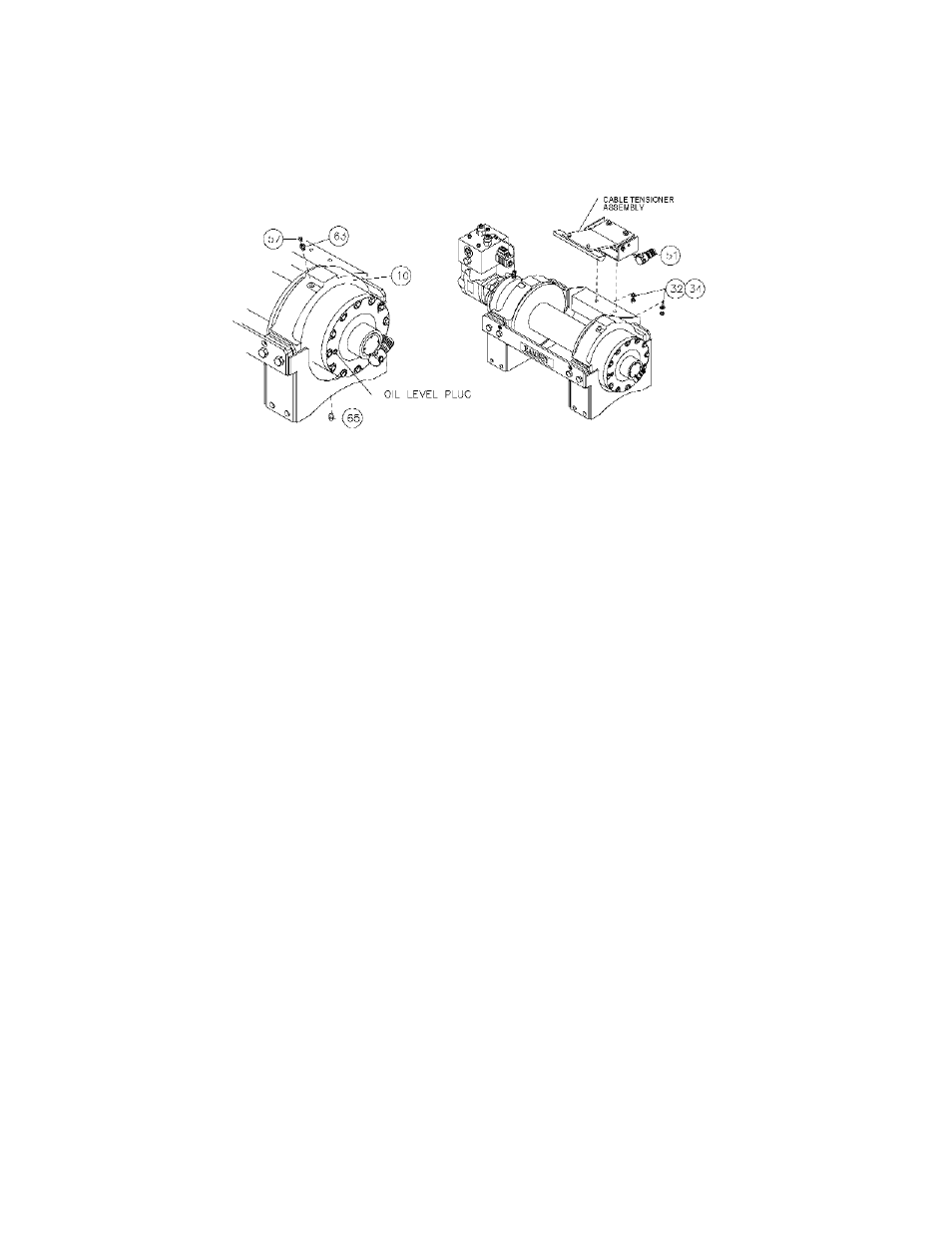
15. Apply Permatex to threads of plug (item #65). Thread plug into tapped hole in bottom of gear housing end
bearing (item #10). Pour approx. 2.50 pints of SAE 80W-140 oil into end bearing. Check oil level by
removing oil level plug noted below. Insert relief fitting (item #57) and thread reducer (item #63) into end
bearing at oil fill hole. Install tensioner assembly to winch frame, center the tension bar between the drum
flanges with a scale or tape measure and tighten the mounting hardware (item #32 & #34) to 75 ft-lbs.
each.
Install winch and connect hydraulic lines and install cable.
WARNING: The cable tensioner is not intended to be energized on a bare drum. Before applying
air to the cable tensioner, engage the clutch and run the winch in the reel in direction winding one
full wrap of cable on the drum. This prevents damage to the cable tensioner.
16. Check proper operation of clutch by applying air pressure to clutch air cylinder to disengage clutch. Verify
that winch freespools. Re-engage clutch. A loud noise should be heard when clutch engages. Winch drum
should not freespool.
17. Operate winch forward and reverse to verify that drum rotates.
18. Unwind cable by rolling it out along the ground to prevent kinking. Securely wrap end of wire rope, oppo-
site hook, with plastic or similar tape to prevent fraying.
Insert the end of cable, opposite hook end, into the hole in drum barrel. Secure cable to drum barrel,
using setscrew furnished with winch. TIGHTEN SETSCREW SECURELY.
Engage the clutch and carefully run the winch in the “reel-in” direction. Keeping tension on end of cable,
spool about five wraps of cable onto the drum and stop. Using a hammer, tap these five wraps tightly over
against the cable anchor flange side of the cable drum. Finish winding all the cable onto the cable drum.
As cable winds onto the drum, watch the tensioner. Tensioner must be free to move without obstruction to
function properly. If tensioner touches any surrounding structure, correct the problem.
CAUTION: DO NOT EXCEED 80 PSI AIR PRESSURE TO THE AIR TENSIONER ACTUATORS.
13