KB Electronics KBVF-48 User Manual
Page 22
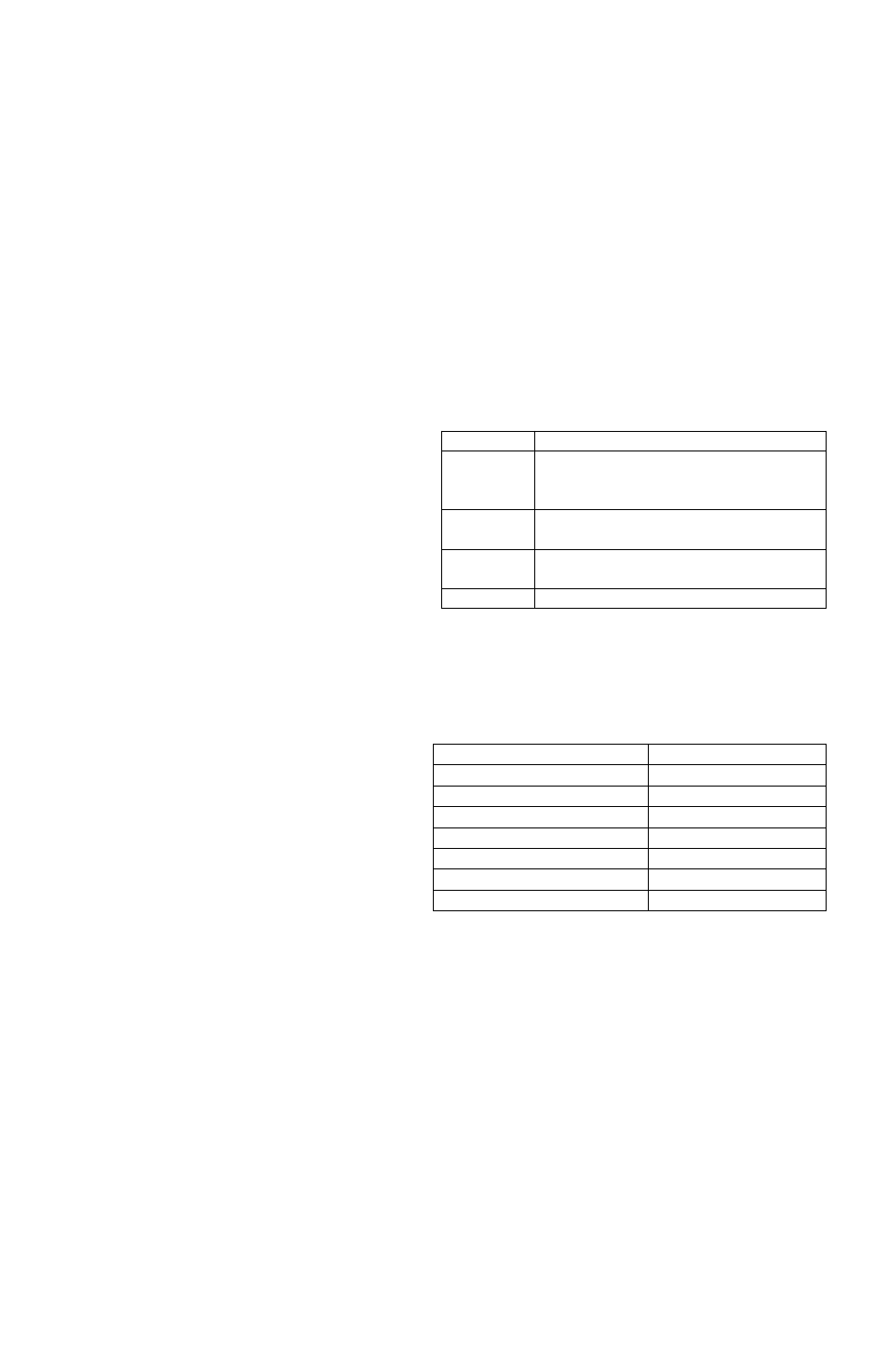
10 AC LINE FUSING
This drive does not contain AC line fuses. Most electrical codes require that each ungrounded conductor
contain circuit protection. Do not fuse neutral or ground connections. It is recommended to install a fuse
(Littelfuse 326, Buss ABC, or equivalent) or a circuit breaker in series with each ungrounded conductor. Do
not fuse motor leads. For the recommended fuse size, see Table 2, on page 11.
Wire the drive in accordance with the National Electrical Code requirements and other local codes that may
apply to the application.
11 DRIVE OPERATION
11.1 START-UP PROCEDURE – After the drive has been properly setup (jumpers and trimpots set to the
desired positions) and wiring completed, the startup procedure can begin. If the AC power has been
properly brought to the drive, the power (PWR) LED will be illuminated green. The status (ST) LED will
indicate drive status, as described in Section 11.2. To remove and install the Finger-Safe Cover, see
Section 5, on page 14.
11.2 FAULT RECOVERY – The drive monitors
four faults (Undervoltage, Overvoltage,
Short Circuit at the motor (phase-to-
phase), I
2
t). Table 5 describes how the
drive will automatically start (factory
setting) after the fault has cleared.
Application Note – In Manual Start
Mode, the drive must be manually
reset for any fault. Use the Manual
Start Switch, as described in Section
9.6, on page 20. Also see Section
12.2, on page 23.
11.3 RESTARTING THE DRIVE AFTER AN
I
2
t FAULT HAS CLEARED – The drive
can be restarted after an I
2
t Fault has
cleared by any of the following meth-
ods.
Note: If an I
2
t Fault occurs, the motor
may be overloaded. Check the motor
current with an AC RMS responding
ammeter. Also, the CL setting may be
set too low. See Section 13.7, on
pages 25 and 26.
1 Disconnect and reconnect the AC
power (approximately 15 seconds).
The “ST” LED must change from quick flashing red to flashing red/yellow.
2 Setting the Main Speed Potentiometer to zero (fully counterclockwise).
Note: In order to be able to reset the drive by setting the Main Speed Potentiometer to zero, it is
necessary to have the MIN Trimpot set to zero (fully counterclockwise).
3 Open and close the Enable switch or contact. See Section 9.8, on pages 20 and 21.
12 DIAGNOSTIC LEDS
The drive contains two diagnostic LEDs to display the drive’s operational status. See Figure 5, on page 13,
for the location of the “PWR” and “ST” LEDs.
22
Notes: 1. Slow Flash = 1 second on and 1 second off. Quick Flash = 0.25
second on and 0.25 second off. 2. In Manual Start Mode, when the Overload
is removed, before the I
2
t times out and trips the drive, the “ST” LED will
flash green. 3. In Manual Start Mode, when the Undervoltage or Overvoltage
condition is corrected, the “ST” LED will flash Red / Yellow / Green.
TABLE 5 – FAULT RECOVERY & RESETTING THE DRIVE*
Fault
Automatic Start Mode (Factory Setting)
Undervoltage
Drive will automatically start
after the bus voltage returns to the operational level
or when the drive is first turned on (power up).
Overvoltage
Drive will automatically start
after the bus voltage returns to the operational level.
Short Circuit
Drive will automatically start
after the short circuit is removed.
I
2
t
Drive must be manually restarted.
* The fault must be cleared before the drive can be reset.
TABLE 6 – DRIVE OPERATING CONDITION &
STATUS LED INDICATOR
Drive Operating Condition
Flash Rate
1
and LED Color
Normal Operation (Run)
Slow Flash Green
Overload (120% – 160% Full Load)
Steady Red
2
I
2
t (Drive Timed Out)
Quick Flash Red
Short Circuit
Slow Flash: Red
Undervoltage
Quick Flash Red / Yellow
3
Overvoltage
Slow Flash Red / Yellow
3
Stop
Steady Yellow