KB Electronics KBVF-48 User Manual
Page 10
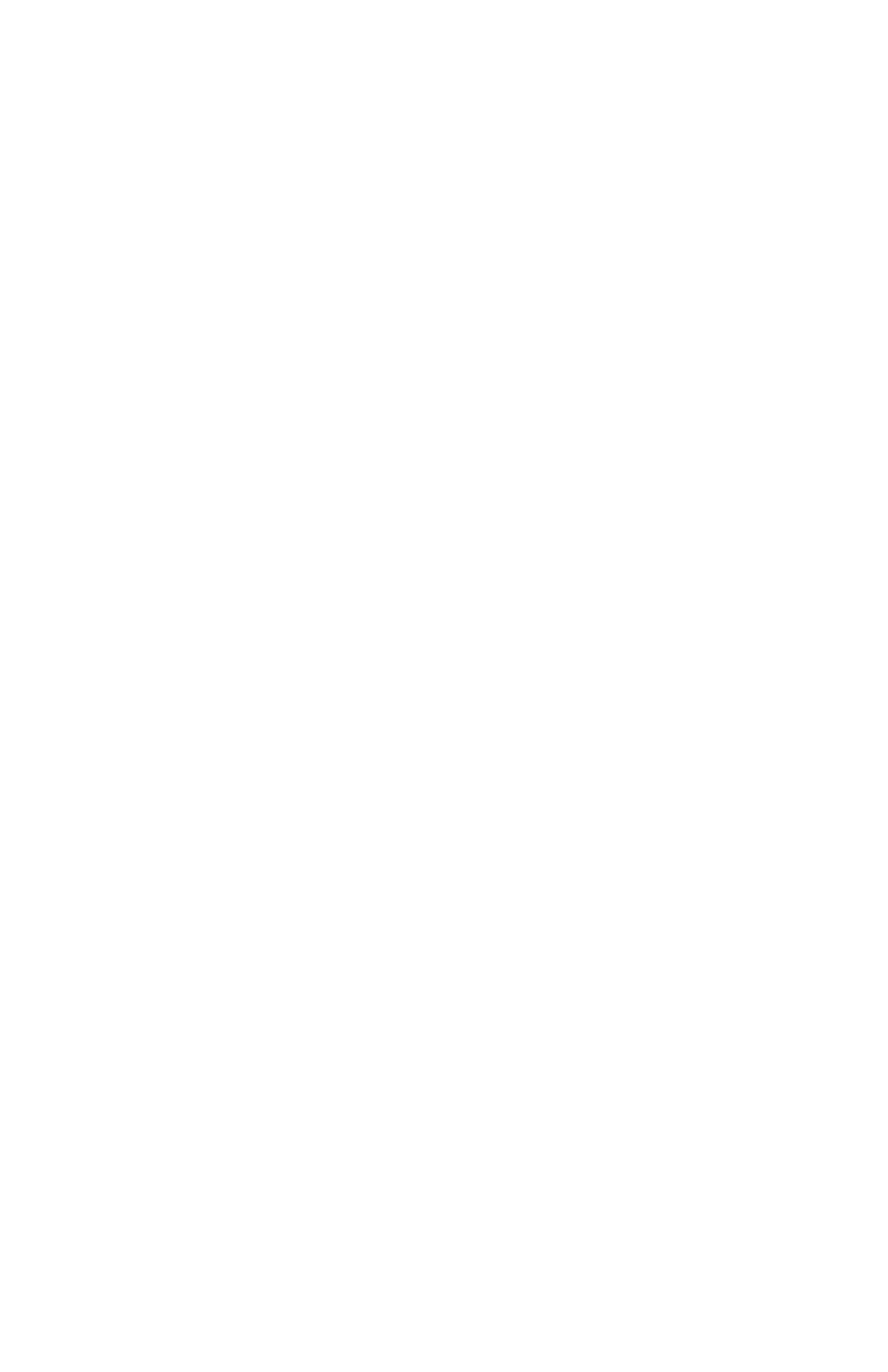
3.2
PERFORMANCE FEATURES
• Power Start™ – Provides more than 200% starting torque which ensures startup of high
frictional loads.
• Slip Compensation with Static Auto-Tune and Boost – Provides excellent load regulation over a
wide speed range.
• Speed Range – 60:1
3.3
PROTECTION FEATURES
• Motor Overload (I
2
t) with RMS Current Limit – Provides motor overload protection which prevents
motor burnout and eliminates nuisance trips. UL approved as an electronic overload protector for
motors. See Section 4.2, on pages 13 and 14. Also see Section 13.7, on pages 25 and 26.
• Electronic Inrush Current Limit (EICL™) – Eliminates harmful inrush AC line current during startup.
• Short Circuit – Prevents drive failure if a short circuit occurs at the motor (phase-to-phase).
• Regeneration – Eliminates nuisance tripping due to high bus overvoltage caused by rapid decelera-
tion of high inertial loads.
• Undervoltage and Overvoltage – Shuts down the drive if the AC line input voltage goes above or
below the operating range.
• MOV Input Transient Suppression.
• Microcontroller Self Monitoring and Auto-Reboot.
3.4
TRIMPOT ADJUSTMENTS
• Minimum Speed (MIN on Models KBVF-27, 29 and OFFSET on SIVFR of Models KBVF-45, 48)
Sets the minimum speed of the motor. See Section 13.1, on page 23.
• Maximum Speed (MAX) – Sets the maximum speed of the motor. See Section 13.2, on page 23.
• Acceleration (ACC) – Sets the amount of time for the motor to accelerate from zero speed to full
speed. See Section 13.3, on page 24.
• Deceleration (DEC/B) – Sets the amount of time for the motor to decelerate from full speed to zero
speed. See Section 13.4, on page 24.
• Slip Compensation (COMP) – Maintains set motor speed under varying loads. See Section 13.5,
on page 24.
• Boost (DEC/B) – In 50 Hz mode, the trimpot automatically becomes Adjustable Boost, which can
be used to set the Volts/Hz Curve for 50 Hz motors to obtain maximum performance. In 50 Hz
Mode, the deceleration time is automatically set to the same as the acceleration time. See Section
13.6, on page 25.
• Current Limit (CL) – Sets the current limit (overload) which limits the maximum current (torque) to
the motor. See Section 13.7, on pages 25 and 26.
3.5
OPTIONAL ACCESSORIES
• SIVFR – Signal Isolator and Run/Fault Relay (Part No. 9597) – Provides isolation between a
non-isolated signal voltage (0 to ±2.5 thru 0 to ±25 Volts DC) or current source (4 – 20 mA DC) and
the drive. Can be used in unidirectional or in bidirectional mode. Run/Fault Relay Output Contacts
are also provided, which can be used to turn on or off equipment or to signal a warning if the drive
is put into the Stop Mode or a fault has occurred. Mounts on the end of the drive. This option is
built-in on models KBVF-45, 48.
• Multi-Speed Board (Part No. 9503) – Provides multi-speed operation using external contacts or a
PLC. Mounts on the end of the drive. For Models KBVF-27, 29 only. Also available factory installed
on Models KBVF-45, 48 – contact our Sales Department.
• Programming Kit (Part No. 9582) – Includes DownLoad Module™ (DLM) handheld programming
device which uploads and downloads drive programs, PC to DLM serial communication cable, DLM
to inverter communication cable, and PC Windows® based Drive-Link™ communication software.
10