Cashco C-CS User Manual
Page 3
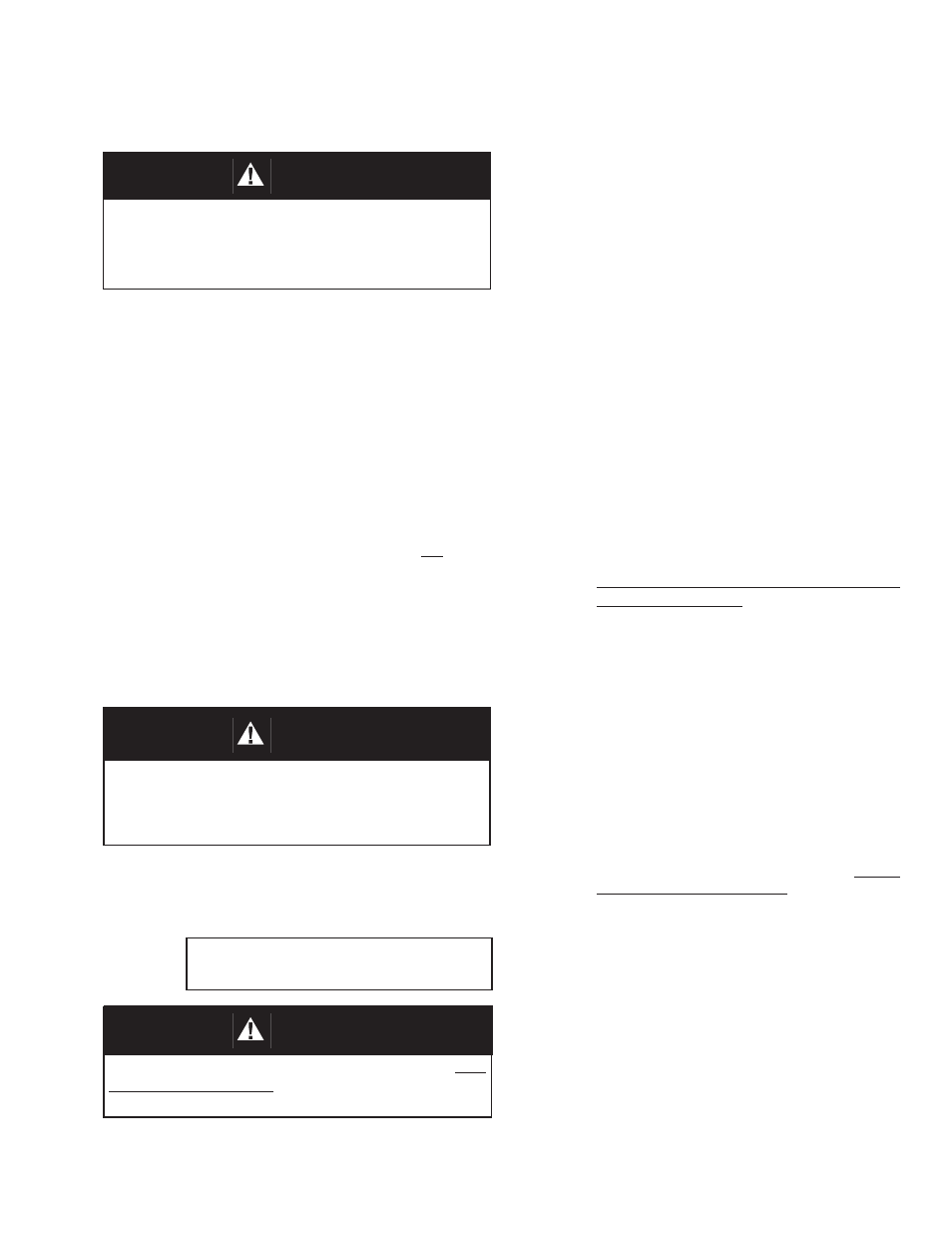
IOM-C-CS
3
4. Pull hitch pin (21) and lift up on handle (6) to
remove.
5. Loosen and remove clamp nuts (13B), wash-
ers (13D), bolts (13C) and clamps (13A). See
Figure 1.
6. Place matchmarks between body (1) and
spring chamber (2) to assist in fi nal ori en ta-
tion when re as sem bled. Lift spring chamber
(2) vertically up and off of body (1) and above
guide post (27) to remove. Note alignment of
spring button (4) tabs (ears) with respect to
slot guides inside spring chamber (2).
7. Remove bearing (26). Lift up and remove ad-
just ing screw cap (25.7) and dowel pin (25.8)
as sem bly. NOTE: May need to tap lightly on
O.D. of adjusting screw (25.6) to free Dowel
pin (25.8) from adjusting screw (25.6).
NOTE: The two guide seals (25.9) may/may
not be extracted with as sem bly (25.7,25.8).
Re move guide seals (25.9).
8. Lift up to remove the ad just ing screw (25.6 )
and spring but ton (4) as an as sem bly. NOTE:
Do not rotate or re move spring button (4) from
ad just ing screw (25.6). Re move spring (7) and
lay aside.
9. Secure the pres sure plate assembly (27,28
and 29) at the “fl ats” near the base of pressure
plate (28). Grasp the lower portion of the plug
(14) by the “fl ats”, which protrudes from the
body (1) inlet, with soft-jawed pliers or soft-
jawed vice and pro ceed to turn CCW (viewed
from above) for dis as sem bly. NOTE: Main tain
fi rm grasp of plug (14). After dis en gage ment,
plug (14) could fall out of body (1) and damage
seating surface area. Remove plug (14).
10. Remove pressure plate assembly (27,28 and
29) and lay aside. NOTE: The travel of the
guide post (27) has been factory set. Do not
loosen or adjust the hex nut (29) on pres sure
plate assembly (27,28,29).
11a. For Model C-CS :
Remove diaphragm (17), O-ring (16), dia-
phragm gas ket (15) and body (1).
11b. For Model C-CS with Opt.-11:
Remove diaphragm (17), diaphragm gaskets
(15), O-ring (18), seal (19), push er plate (20),
O-ring (16) and body (1).
12. Inspect plug (14) and seating surface of body
(1) for excessive wear. Replace all worn
parts.
A. General:
1. Maintenance procedures here in af ter are
based upon removal of the regulator unit from
the pipeline where installed.
2. Refer to Figure 2 for basic regulator item
num ber reference ( ) and description.
B. Diaphragm – Trim Replacement:
1. Securely install the regulator in a soft-jawed
vise with the spring chamber (2) di rect ed up-
wards. Ensure that the body (1) is not held in
the vise by the Tri-clamp
®
fi tting con nec tions.
The regulator may be held in the vise with
fl ats on the plug (14). If this method is used,
ensure that the plug (14) is in contact with the
seating area of the body (1) and the face of
the inlet fl ange of the body (1) is resting on
the vise.
SECTION VI
2. Relax range spring (7) by turning handle (6)
CCW (viewed from above) until rotation stops.
Count and record the number of rev o lu tions
in the box below:
VI. MAINTENANCE
Number of revolutions required to relax
range spring: ________
3. Remove socket head set screw (30) CCW
from top end of guide post (27).
SYSTEM UNDER PRES SURE. Prior to per form ing
any maintenance, isolate the reg u la tor from the
sys tem and relieve all pressure. Failure to do so
could result in personal injury.
WARNING
SPRING UNDER COMPRESSION. Relieve all
spring (7) compression prior to removing clamp
(13). Failure to do so may result in fl ying parts that
could result in personal injury.
WARNING
CAUTION
Do not apply spring load or operate regulator with
hitch pin (21) removed from top of guide post (27 ).
Pre ma ture di a phragm failure will re sult.