Cashco POSR-1 User Manual
Page 7
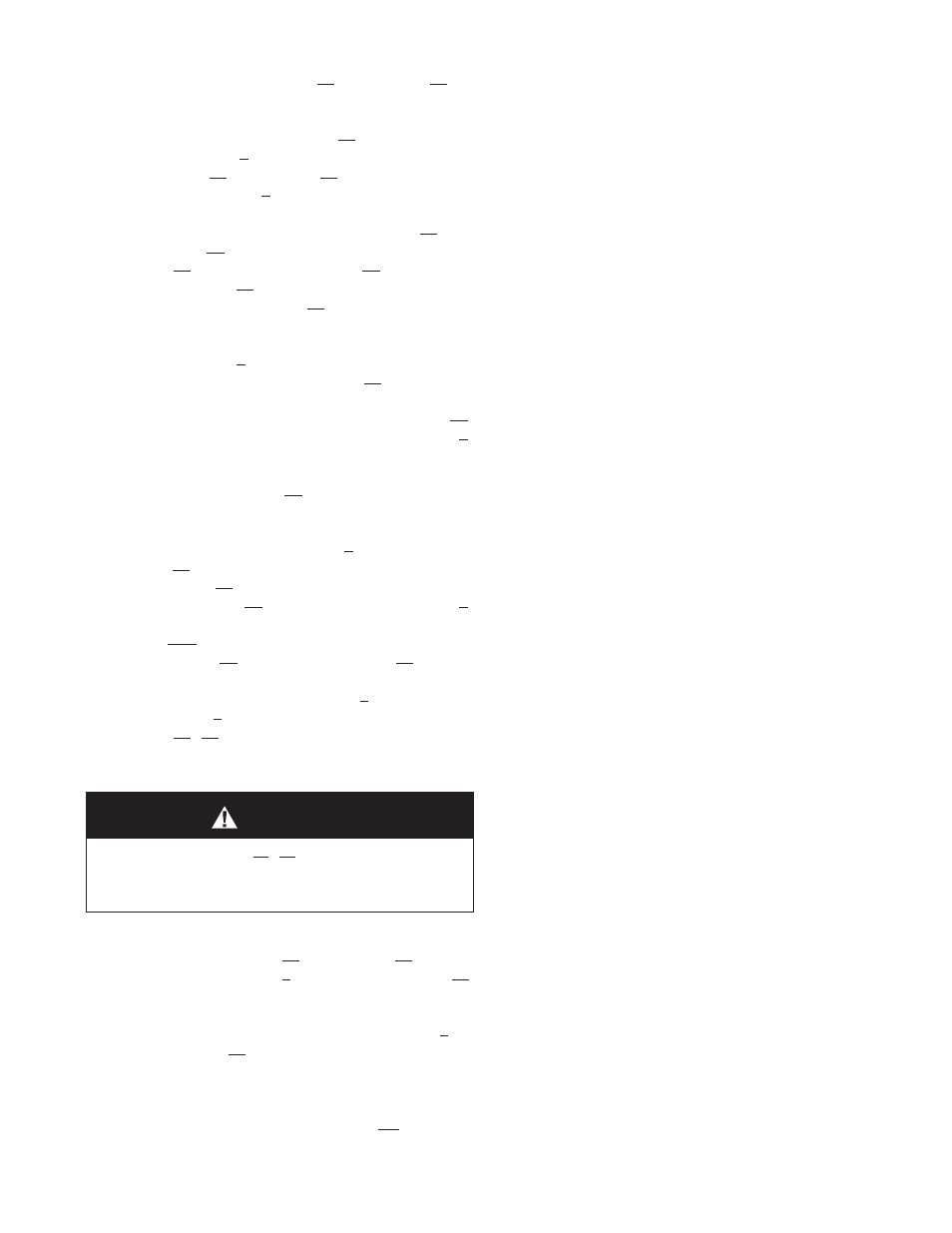
IOM-POSR-1
7
38. Place the two nuts (18) onto bolts (17) of
above, and fi nger-tighten.
39. Place remaining bolts (17) through spring
cham ber (2) bolt hole openings. Engage all
nuts (18) onto bolts (17) along un der neath
side of body (1) fl ange and fi nger-tighten.
40. Remove the two upside-down bolts (17) and
nuts (18) and rotate to position of other bolts
(17). Place nameplate tag (21) over one of
the bolts (17) before replacing into bolt hole.
Fin ger-tighten nuts (18).
41. Observe through opening in top of spring
cham ber (2) to ensure the concentricity of the
recess in the spring button (16) with the top
opening. It may be necessary to use an awl
or similar tool to realign the spring button (16)
as much as possible. The spring cham ber (2)
is not tightened down, and may be temporar-
ily “shifted” to help ensure alignment for the
adjusting screw (19) en gage ment.
42. Place lubricant onto the upper exposed threads
of the spring chamber’s (2) ad just ing screw
(19) opening. Place lu bri cant onto the ad just ing
screw (19) lower-end threads. Engage adjust-
ing screw (19) back into spring cham ber (2)
by rotating CW (viewed from above). Engage
only until resistance is made with the range
spring (15) via the spring button (16).
43. Realign the spring chamber (2) fl ange with the
body (1) fl ange, and wrench-tighten bolting
(17, 18) in an al ter nat ing, crossing pattern.
Final tightening should be done with a torque
wrench to 15 ft.-lbs. (20 N-M).
sem bly including interconnecting nipple (19),
tubing (21), and tubing fi ttings (20).
D. Main Valve (MV):
1. Securely install the body (1) in a vise with the
loading chamber (2) directed upwards.
2. Draw or embed a match mark between body
(1) casting and spring chamber (2) casting
along fl anged area.
3. Remove all cap screws (14) and nuts (15).
4. Remove loading chamber (2), diaphragms
(12), diaphragm gaskets (13) and pusher
plate (11). Clean body (1) and diaphragm
(12) fl ange surface.
5. Rotate cap screws (10) CCW to remove, lift
shield plate (9) out of body (1) cavity.
6. Remove body (1) from vise, rotate body (1)
with body cap (4) directed upwards and re-
secure body (1) in vise.
7. Loosen and remove body cap (4) using a hex
head wrench with a lever length of at least 15"
inches. The wrench should be rapped with a
hammer to loosen.
8. Remove piston spring (6), piston (3.2) and
cylinder (3.1). Inspect parts for excessive wear,
especially at seat surfaces. Replace if worn.
9. Remove the cylinder gasket (8) and clean
contacting surface in body (1).
10. Clean fl at mating surfaces of body (1) to body
cap (4) shoulder.
11. Clean debris from within body (1) cavity and
all parts to be reused.
12. Reinstall a new cylinder gasket (8). Use the
cylinder (3.1) to fi rmly and evenly press the
gasket (8) into place. Gasket surfaces maybe
lightly coated with pipe sealant prior to in stal-
la tion.
13. Ensure cylinder (3.1) is concentrical within the
body (1) opening. Slide the piston (3.2) into
the cylnder (3.1).
14. Place piston spring (6) into piston cavity.
15. Apply pipe thread sealant to body cap (4)
threads and screw into body (1). When body
WARNING
Never replace bolting (17, 18) with just any bolting if
lost. Bolt heads and nuts are marked with spec i fi ca tion
identifi cation markings. Use only proper grades as re-
placements.
44. Continue CW rotation (viewed from above) of
ad just ing screw (19) until locknut (20) touches
spring chamber (2). Back adjusting screw (19)
out by rotating CCW (viewed from above) two
revolutions. This position will ap prox i mate the
pressure setpoint prior to dis as sem bly if the
locknut (20) is only loosened two revolutions
as directed in article 2. previous, this sub-
section.
45. Pressure leak test pilot valve (PV) assembly
when rejoined with the main valve (MV) as-