4 tool storage operation, 5 pls operation (optional) – PA Industries Edge Servo Roll Feed SRF-100/125/200/300/400/500/600 - Operation Manual User Manual
Page 5
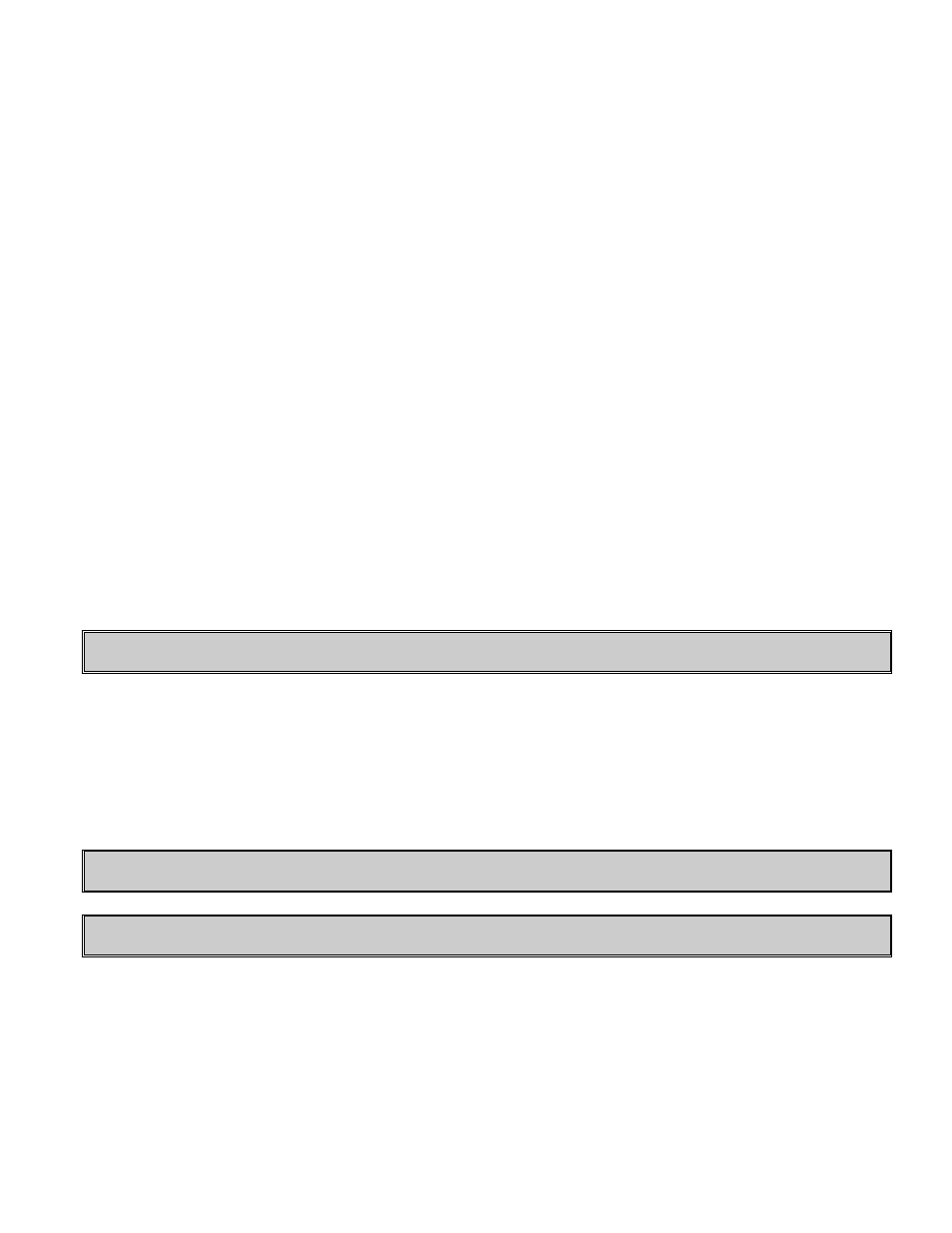
ULTRA EDGE SERVO ROLL FEED 2/14/
2003
5
The result is an accurately positioned strip exactly 11.138 inches from its starting point. This entire process happens
in milliseconds.
2.4 TOOL STORAGE OPERATION
The tool storage feature allows for storing of parameters that are different from tool to tool. It takes just a few seconds
to activate feeding parameters associated with a certain tool number. Maximum 200 tools can be stored. Tools are
organized by Tool number, which is user definable and can contain up to 7 digits.
Each tool consists of the following parameters:
-Length;
- Batch Count;
- Speed;
- Dwell;
- Accel;
- Decel;
- Feed Cam “On”;
- Feed Cam “Off”;
- Reset Cam “On”;
- Reset Cam “Off”;
- Pilot Release Cam “On”;
- Pilot Release Cam “Off”;
- Aux1. Cam “On”;
- Aux1. Cam “Off”;
- Aux2. Cam “On”;
- Aux2. Cam “Off”;
- Aux3. Cam “On”;
- Aux3. Cam “Off”;
NOTE: Cam settings are available only with PLS version of software.
Consider the tool storage as a part of the servo drive’s NVRAM memory that is dedicated to storing information of all
the existing tools. In order to run a tool, it must be activated. Tool activation is an internal drive procedure of making
a copy of the tool, and placing it in a different memory location. This copy, not the tool in the tool storage, is used to
perform material feeding. “Tool #NNN is active” means only that the feed running parameters are copied from this
tool.
A tool in the tool storage area and its copy, are edited independently, with the difference, that only two of the copy’s
parameters are accessible – Length and Batch Count. These are accessible from the Operator screen. In order to edit
the rest of the parameters of the tool, the tool in tool storage must be edited, and then, reactivated.
NOTE: Deleting an active tool from the tool storage causes deletion of its copy as well.
NOTE: An active tool remains active after power recycling.
2.5 PLS OPERATION (OPTIONAL)
The PLS, Programmable Limit Switch consists of an intelligent encoder and the cable that connects the encoder to
the servo drive. The encoder is mounted on the press and its shaft is coupled or belted to the crankshaft with a one to
one (1:1) ratio. On every power-up, the encoder turns into the intelligent mode (for approximately 10 msec) to read
its actual position and store it in the servo drive.
The encoder then turns into the incremental mode, sending the count signals to the servo drive proportionally to the
angle of the move (1024 counts per revolution). The servo drive software, having the start point position of the