Thermal considerations with baseplate – GE Industrial Solutions QPW050-060 Series User Manual
Page 18
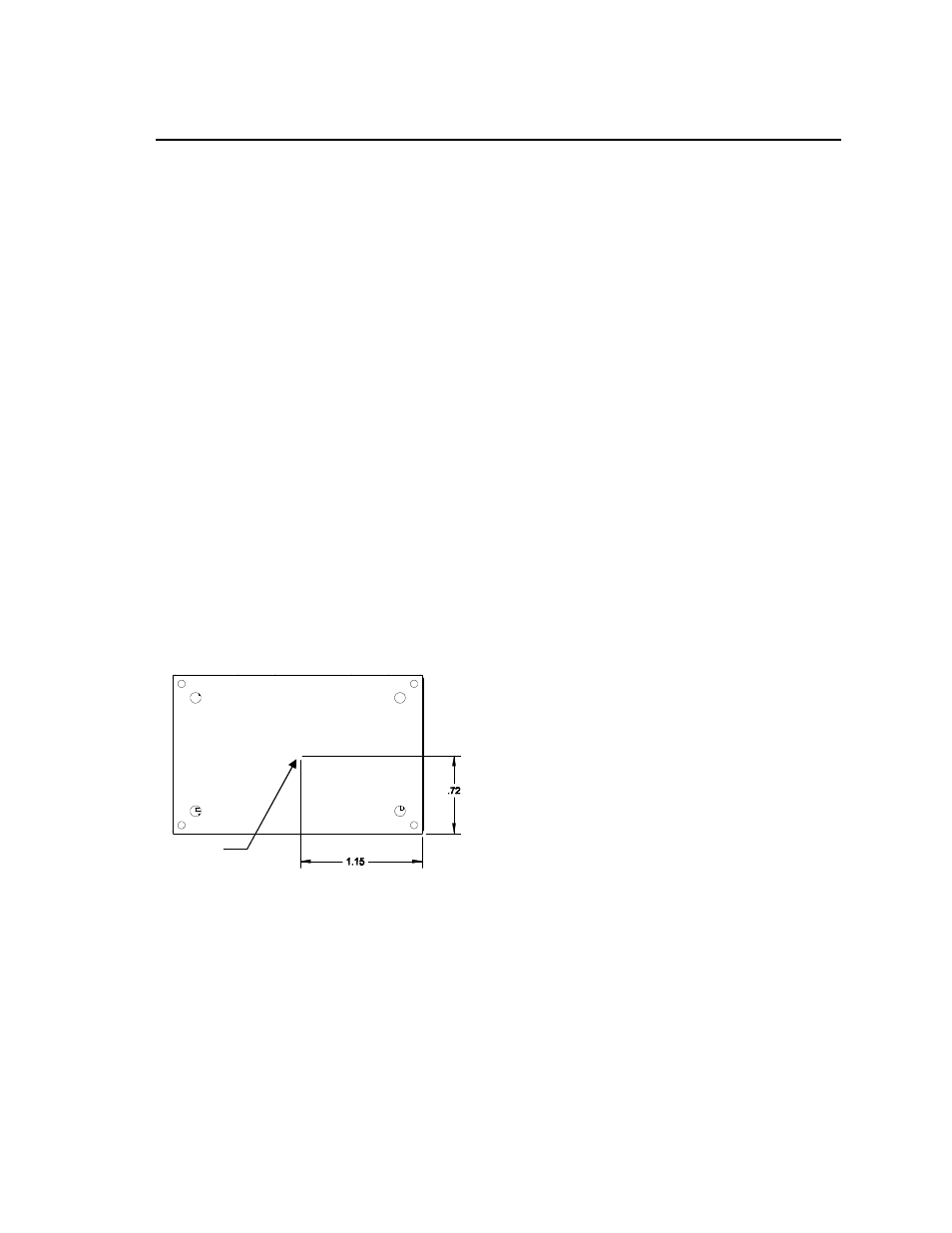
Data Sheet
February 2, 2011
QPW050/060 Series Power Modules; DC-DC converters
36-75Vdc Input; 1.2Vdc to 3.3Vdc Output
LINEAGE
POWER
18
Thermal Considerations with
Baseplate
The baseplate option (-H) power modules are
constructed with baseplate on topside of the open
frame power module. The baseplate includes quarter
brick through-threaded, M3 x 0.5 mounting hole
pattern, which enable heat sinks or cold plates to
attaché to the module. The mounting torque must not
exceed 0.56 N-m (5 in.-lb.) during heat sink assembly.
This module operates in a variety of thermal
environments; however, sufficient cooling should be
provided to help ensure reliable operation.
Considerations include ambient temperature, airflow,
module power dissipation, and the need for increased
reliability. A reduction in the operating temperature of
the module will result in an increase in reliability. The
thermal data presented here is based on physical
measurements taken in a wind tunnel.
Heat-dissipating components are mounted on the
topside of the module and coupled to the baseplate
with thermal gap material. Heat is removed by
conduction, convection and radiation to the
surrounding environment. Proper cooling can be
verified by measuring the thermal reference
temperature (T
ref
). Peak temperature (T
ref
) occurs at
the position indicated in Figure 51. For reliable
operation this temperature should not exceed 95ºC
temperature threshold.
Figure 51. T
ref
Temperature Measurement
Location for QPW-H baseplate option
The output power of the module should not exceed
the rated power for the module as listed in the
Ordering Information table.
Although the maximum Tref temperature of the power
modules is 95 °C, you can limit this temperature to a
lower value for extremely high reliability. Please refer
to the Application Note “Thermal Characterization
Process For Open-Frame Board-Mounted Power
Modules” for a detailed discussion of thermal aspects
including maximum device temperatures.
Heat Transfer via Convection
Increased airflow over the module enhances the heat
transfer via convection. Following derating figures
shows the maximum output current that can be
delivered by each module in the respective orientation
without exceeding the maximum T
ref
temperature
versus local ambient temperature (T
A
) for natural
convection through 2m/s (400 ft./min).
Note that the natural convection condition was
measured at 0.05 m/s to 0.1 m/s (10ft./min. to 20
ft./min.); however, systems in which these power
modules may be used typically generate natural
convection airflow rates of 0.3 m/s (60 ft./min.) due to
other heat dissipating components in the system. The
use of Figures 2 - 4 are shown in the following
example:
Example
What is the minimum airflow and heat sink size
necessary for a QPW050A0F-H operating at VI = 48
V, an output current of 30A, and a maximum ambient
temperature of 70 °C in transverse orientation.
Solution:
Given: VI = 48V
Io = 30A
TA = 70 °C
To determine airflow (V) and heatsink size (Use
Figures 52 - 53):
There are couple of solution can be derived from
below derating figures.
1) Baseplated with 0.25” heatsink in natural
convection (V= 0 m/sec) environment.
2) No baseplate required when operated with
airflow of 200 LFM (V = 1m/sec).
T
ref