Ge energy, 6a austin microlynx, Ii: non-isolated dc-dc power modules – GE Industrial Solutions 6A Austin MicroLynx II User Manual
Page 19: Data sheet, Surface mount information
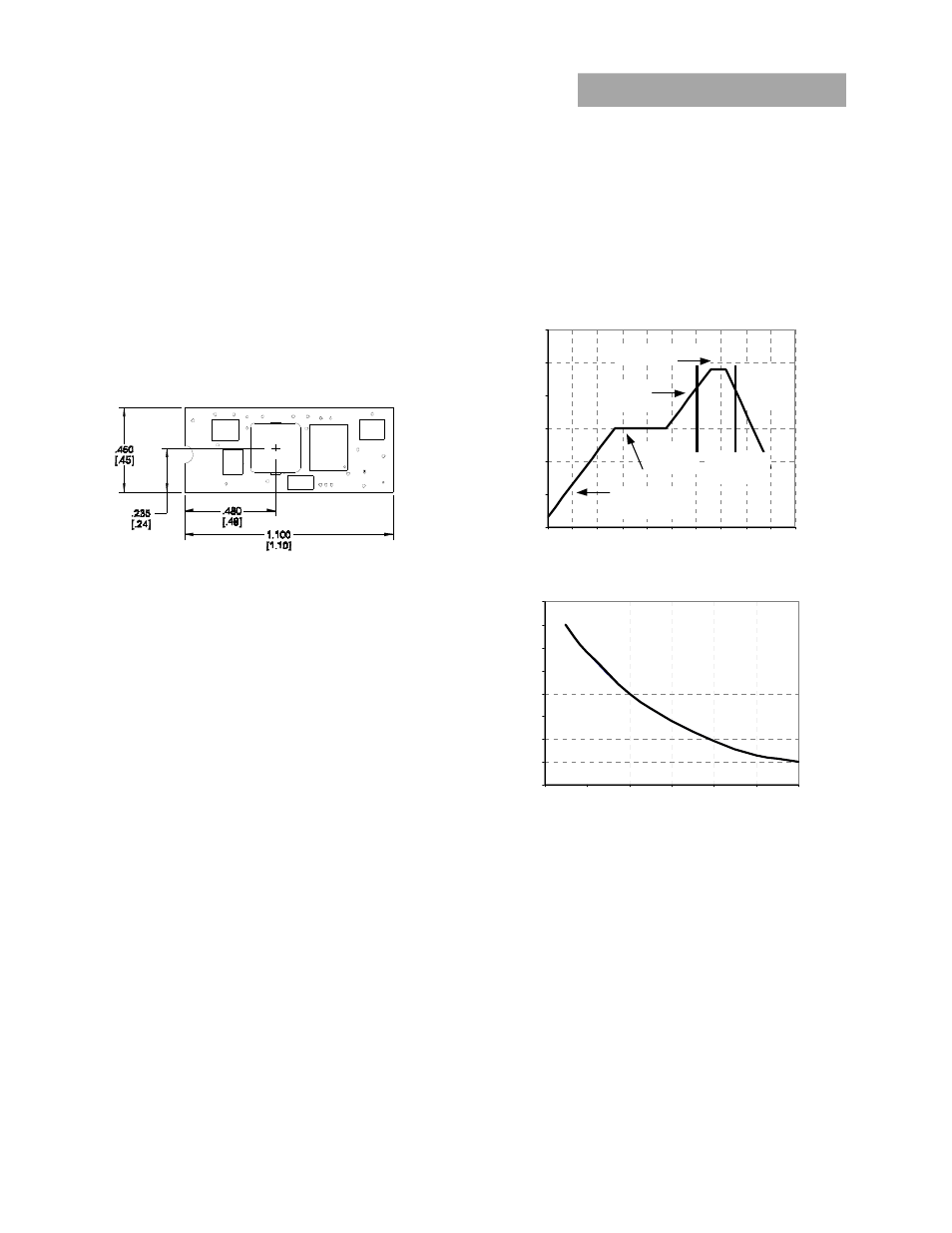
GE Energy
Data Sheet
6A Austin MicroLynx
TM
II: Non-Isolated DC-DC Power Modules
8.3Vdc –14Vdc input; 0.75Vdc to 5.5Vdc output; 6A Output Current
October 16, 2012
©2012 General Electric Company. All rights reserved.
Page 19
Surface Mount Information
Pick and Place
The Austin MicroLynx
TM
II 12V SMT modules use an open
frame construction and are designed for a fully automated
assembly process. The modules are fitted with a label
designed to provide a large surface area for pick and
placing. The label meets all the requirements for surface
mount processing, as well as safety standards and is able to
withstand maximum reflow temperature. The label also
carries product information such as product code, serial
number and location of manufacture.
Figure 34. Pick and Place Location.
Nozzle Recommendations
The module weight has been kept to a minimum by using
open frame construction. Even so, these modules have a
relatively large mass when compared to conventional SMT
components. Variables such as nozzle size, tip style,
vacuum pressure and pick & placement speed should be
considered to optimize this process. The minimum
recommended nozzle diameter for reliable operation is
3mm. The maximum nozzle outer diameter, which will safely
fit within the allowable component spacing, is 8 mm max.
Tin Lead Soldering
The Austin MicroLynx
TM
II 12V SMT power modules are lead
free modules and can be soldered either in a lead-free
solder process or in a conventional Tin/Lead (Sn/Pb) process.
It is recommended that the customer review data sheets in
order to customize the solder reflow profile for each
application board assembly. The following instructions must
be observed when soldering these units. Failure to observe
these instructions may result in the failure of or cause
damage to the modules, and can adversely affect long-term
reliability.
In a conventional Tin/Lead (Sn/Pb) solder process peak
reflow temperatures are limited to less than 235
o
C.
Typically, the eutectic solder melts at 183
o
C, wets the land,
and subsequently wicks the device connection. Sufficient
time must be allowed to fuse the plating on the connection
to ensure a reliable solder joint. There are several types of
SMT reflow technologies currently used in the industry.
These surface mount power modules can be reliably
soldered using natural forced convection, IR (radiant
infrared), or a combination of convection/IR. For reliable
soldering the solder reflow profile should be established by
accurately measuring the modules CP connector
temperatures.
REFL
O
W
TE
MP
(°
C)
REFLOW TIME (S)
Figure 35. Reflow Profile for Tin/Lead (Sn/Pb) process.
MAX TEM
P
SO
LD
ER
(°
C)
Figure 36. Time Limit Curve Above 205
o
C for Tin/Lead
(Sn/Pb) process.
0
50
100
150
200
250
300
Preheat zo ne
max 4
o
Cs
-1
Soak zo ne
30-240s
Heat zone
max 4
o
Cs
-1
Peak Temp 235
o
C
Co oling
zone
1-4
o
Cs
-1
T
lim
above
205
o
C
200
205
210
215
220
225
230
235
240
0
10
20
30
40
50
60