Rainbow Electronics MAX1717 User Manual
Page 29
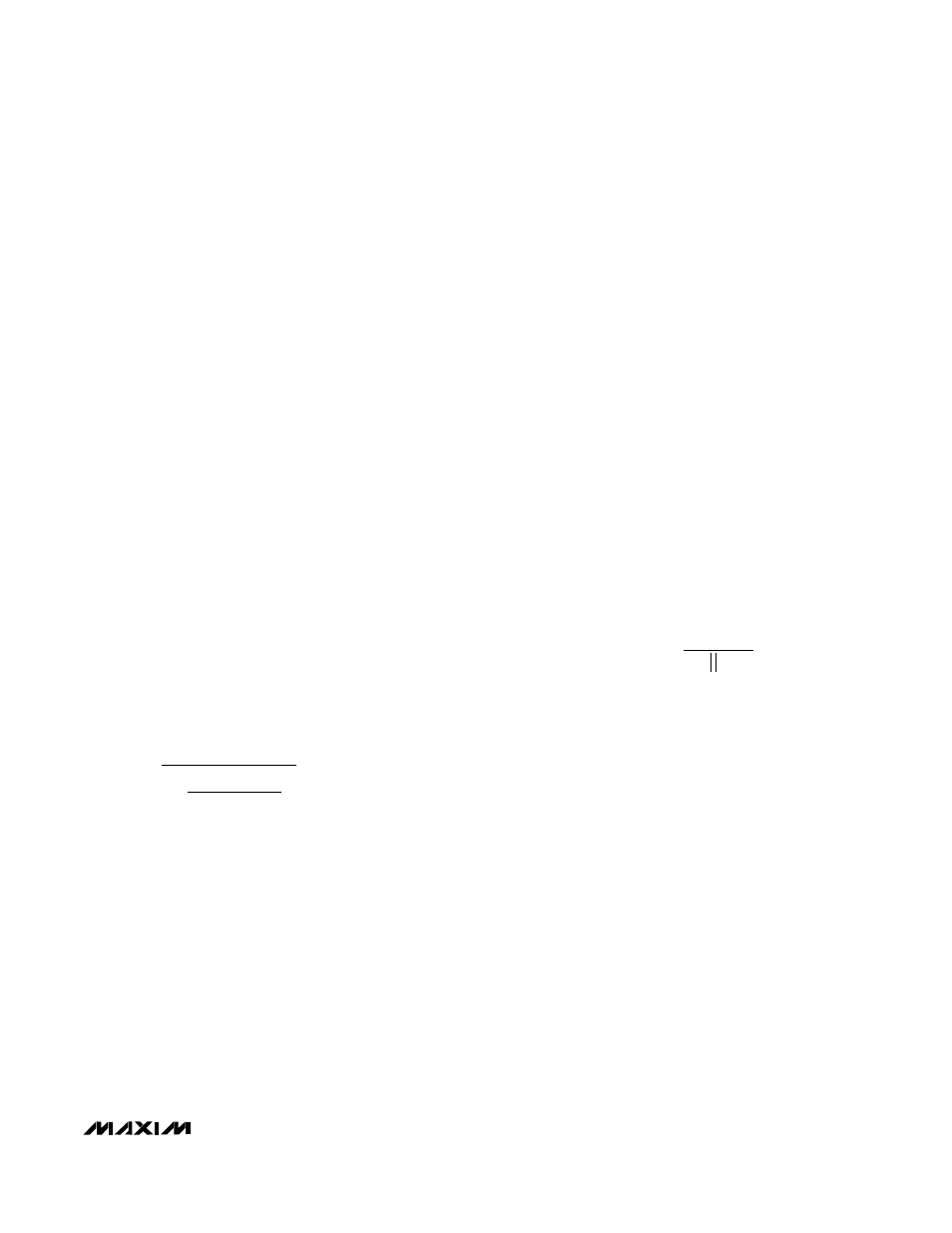
MAX1717
Dynamically Adjustable, Synchronous
Step-Down Controller for Notebook CPUs
______________________________________________________________________________________
29
Dropout Performance
The output voltage adjust range for continuous-conduc-
tion operation is restricted by the nonadjustable 500ns
(max) minimum off-time one-shot (375ns max at
1000kHz). For best dropout performance, use the slower
(200kHz) on-time settings. When working with low input
voltages, the duty-factor limit must be calculated using
worst-case values for on- and off-times. Manufacturing
tolerances and internal propagation delays introduce
an error to the TON K-factor. This error is greater at
higher frequencies (Table 3). Also, keep in mind that
transient response performance of buck regulators
operated close to dropout is poor, and bulk output
capacitance must often be added (see the VSAG equa-
tion in the Design Procedure section).
The absolute point of dropout is when the inductor cur-
rent ramps down during the minimum off-time (
∆I
DOWN
)
as much as it ramps up during the on-time (
∆I
UP
). The
ratio h =
∆I
UP
/
∆I
DOWN
is an indicator of ability to slew
the inductor current higher in response to increased
load, and must always be greater than 1. As h
approaches 1, the absolute minimum dropout point, the
inductor current will be less able to increase during
each switching cycle and V
SAG
will greatly increase
unless additional output capacitance is used.
A reasonable minimum value for h is 1.5, but this may
be adjusted up or down to allow tradeoffs between
V
SAG
, output capacitance, and minimum operating
voltage. For a given value of h, the minimum operating
voltage can be calculated as:
where V
DROP1
and V
DROP2
are the parasitic voltage
drops in the discharge and charge paths (see On-Time
One-Shot), T
OFF(MIN)
is from the Electrical Character-
istics, and K is taken from Table 3. The absolute minimum
input voltage is calculated with h = 1.
If the calculated V
IN(MIN)
is greater than the required
minimum input voltage, then operating frequency must
be reduced or output capacitance added to obtain an
acceptable V
SAG
. If operation near dropout is anticipat-
ed, calculate V
SAG
to be sure of adequate transient
response.
Dropout Design Example:
V
OUT
= 1.6V
f
SW
= 550kHz
K = 1.8µs, worst-case K = 1.58µs
T
OFF(MIN)
= 500ns
V
DROP1
= V
DROP2
= 100mV
h = 1.5
V
IN(MIN)
= (1.6V + 0.1V) / (1-0.5µs x 1.5/1.58µs) + 0.1V
- 0.1V = 3.2V
Calculating again with h = 1 gives the absolute limit of
dropout:
V
IN(MIN)
= (1.6V + 0.1V) / (1-1.0
✕
0.5µs/1.58µs) - 0.1V
+ 0.1V = 2.5V
Therefore, V
IN
must be greater than 2.5V, even with very
large output capacitance, and a practical input voltage
with reasonable output capacitance would be 3.2V.
Adjusting V
OUT
with a Resistor-Divider
The output voltage can be adjusted with a resistor-
divider rather than the DAC if desired (Figure 11). The
drawback is that the on-time doesn’t automatically
receive correct compensation for changing output voltage
levels. This can result in variable switching frequency
as the resistor ratio is changed, and/or excessive
switching frequency. The equation for adjusting the output
voltage is:
where V
FB
is the currently selected DAC value, and
R
INT
is the FB input resistance. When using external
resistors, FBS remote sensing is not recommended, but
GNDS remote sensing is still possible. Connect FBS to
FB, and GNDS to a remote ground location. In resistor-
adjusted circuits, the DAC code should be set as close
as possible to the actual output voltage in order to mini-
mize the shift in switching frequency.
Adjusting V
OUT
Above 2V
The feed-forward circuit that makes the on-time depen-
dent on battery voltage maintains a nearly constant
switching frequency as V
IN
, I
LOAD
, and the DAC code
are changed. This works extremely well as long as FB
is connected directly to the output. When the output is
adjusted with a resistor divider, the switching frequency
is increased by the inverse of the divider ratio.
This change in frequency can be compensated with the
addition of a resistor-divider to the battery-sense input
(V+). Attach a resistor-divider from the battery voltage
to V+ on the MAX1717, with the same attenuation factor
as the output divider. The V+ input has a nominal input
impedance of 600k
Ω, which should be considered
when selecting resistor values.
V
V
R
R
R
OUT
FB
INT
=
+
1
1
2
V
V
V
T
x h
K
V
V
IN MIN
OUT
DROP
OFF MIN
DROP
DROP
(
)
(
)
=
+
(
)
−
+
−
1
2
1
1