Guardian Technologies 5209 User Manual
Page 61
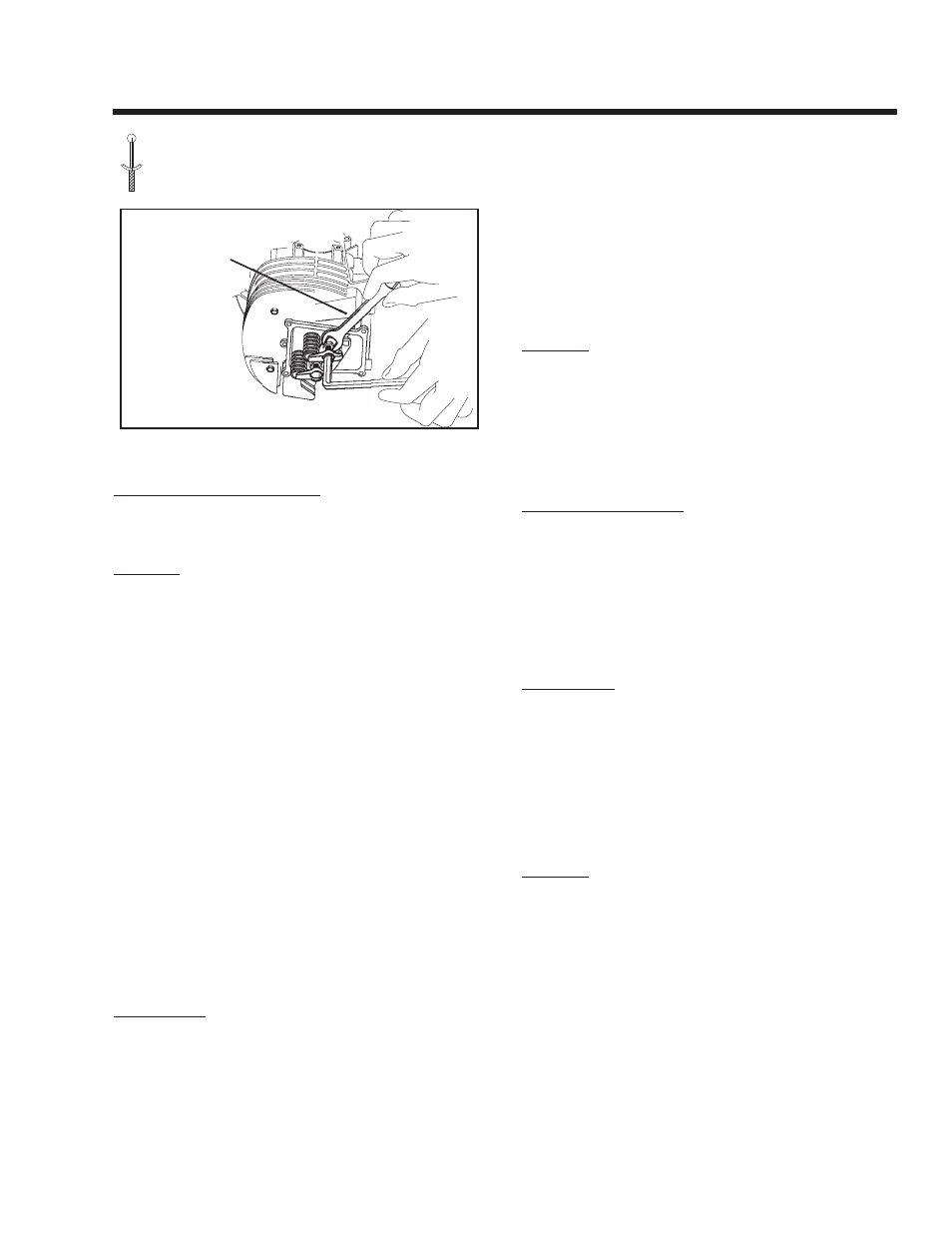
section 6
Diagnostic tests
Page 59
toRQue speciFication
RocKeR aRM JaM nut
168 inch-pounds (19 nm)
CROW'S FOOT
Figure 6-52 – Tightening the Jam Nut
INSTALL ROCKER ARM COVER
1. Use a new rocker arm cover gasket. Install the rocker arm
cover and retain with four screws.
RESULTS:
Adjust valves to specification and retest. If problem
continues, refer to Flow Chart.
TEST 41 - CHECk ENgINE / CYLINdER LEAk
dOWN TEST / COMPRESSION TEST
Most engine problems may be classified as one or a
combination of the following:
• Will not start.
• Starts hard.
• Lack of power.
• Runs rough.
• Vibration.
• Overheating.
• High oil consumption.
The Cylinder Leak Down Tester (Generac P/N
0F77000SRV) checks the sealing (compression) abil-
ity of the engine by measuring air leakage from the
combustion chamber. Compression loss can present
many different symptoms. This test is designed to
detect the section of the engine where the fault lies
before disassembling the engine.
PROCEDURE:
1. Remove a spark plug.
2. Gain access to the flywheel. Remove the valve cover.
3. Rotate the engine crankshaft until the piston reaches top dead
center (TDC). Both valves should be closed.
4. Lock the flywheel at top dead center.
5. Attach cylinder leak down tester adapter to spark plug hole.
6. Connect an air source of at least 90 psi to the leak down tester.
7. Adjust the regulated pressure on the gauge to 80 psi.
8. Read the right hand gauge on the tester for cylinder pressure. 20
percent leakage is normally acceptable. Use good judgement,
and listen for air escaping at the carburetor, the exhaust, and the
crankcase breather. This will determine where the fault lies.
9. Repeat Steps 1 through 8 on remaining cylinder.
RESULTS:
• Air escapes at the carburetor – check intake valve.
• Air escapes through the exhaust – check exhaust
valve.
• Air escapes through the breather – check piston
rings.
• Air escapes from the cylinder head – the head gas-
ket should be replaced.
CHECK COMPRESSION:
Lost or reduced engine compression can result in (a)
failure of the engine to start, or (b) rough operation.
One or more of the following will usually cause loss of
compression:
• Blown or leaking cylinder head gasket.
• Improperly seated or sticking-valves.
• Worn Piston rings or cylinder. (This will also result in
high oil consumption).
PROCEDURE:
1. Remove both spark plugs.
2. Insert a compression gauge into either cylinder.
3. Crank the engine until there is no further increase in pressure.
4. Record the highest reading obtained.
5. Repeat the procedure for the remaining cylinder and record the
highest reading.
RESULTS:
Normal compression is approximately 150 psi. The dif-
ference in pressure between the two cylinders should
not exceed 25 percent. If the difference is greater than
25 percent, loss of compression in the lowest reading
cylinder is indicated.
Example 1: If the pressure reading of cylinder #1 is
165 psi and of cylinder #2, 160 psi, the difference is 5
psi. Divide "5" by the highest reading (165) to obtain
the percentage of 3.0 percent.
Example 2: No. 1 cylinder reads 160 psi; No. 2 cylinder
reads 100 psi. The difference is 60 psi. Divide "60" by
"160" to obtain "37.5" percent. Loss of compression in
No. 2 cylinder is indicated.
If compression is poor, look for one or more of the fol-
lowing causes: