Bryant COMMERCIAL SINGLE PACKAGE ROOFTOP GAS HEAT/ELECTRIC COOLING 581B User Manual
Page 60
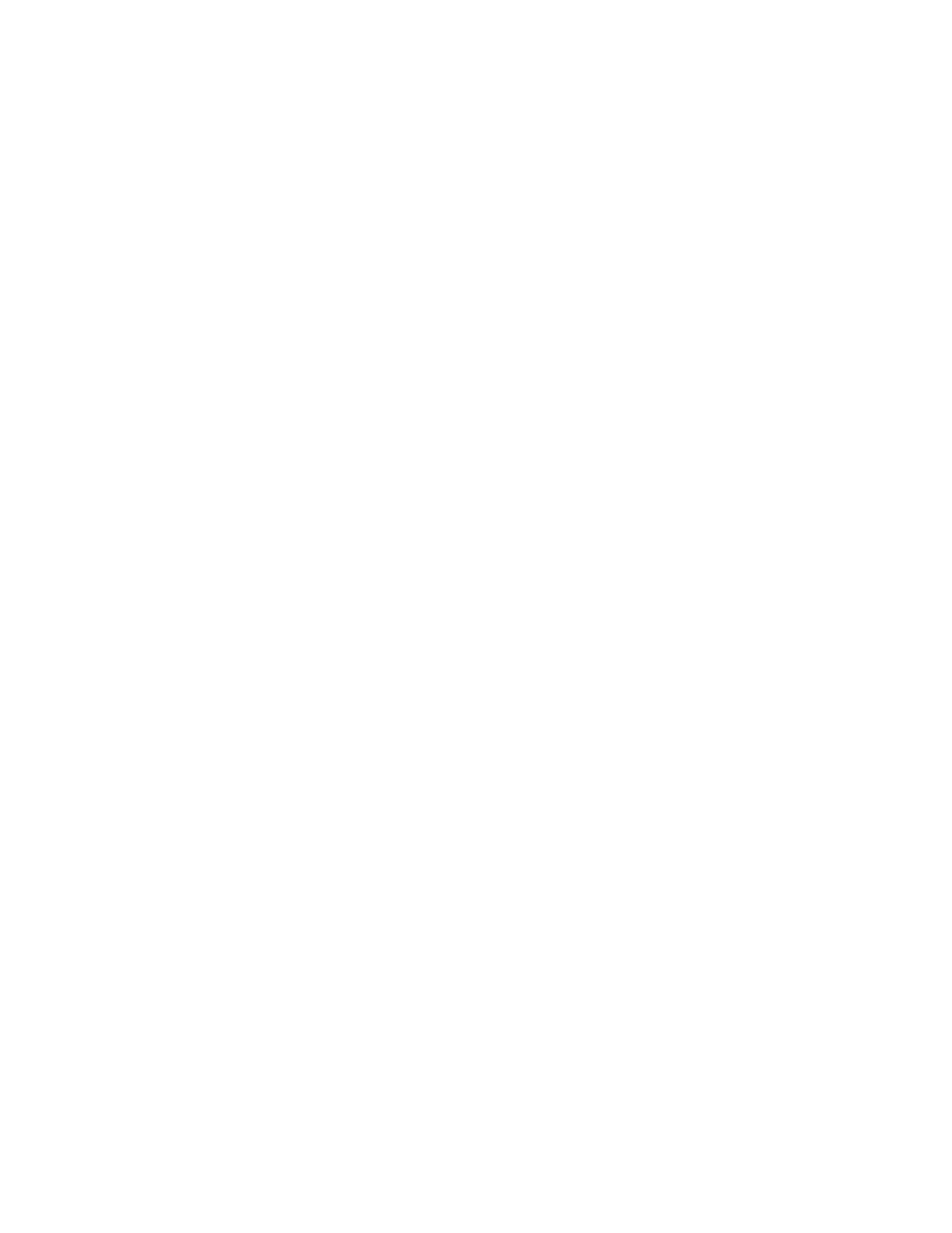
60
GUIDE SPECIFICATIONS
PACKAGED ROOFTOP COOLING UNIT WITH GAS HEAT —
CONSTANT VOLUME APPLICATION
HVAC GUIDE SPECIFICATIONS
SIZE RANGE: 3 TO 12
1
/
2
TONS, NOMINAL COOLING
72,000 TO 250,000 BTUH,
NOMINAL INPUT HEATING
BRYANT MODEL NUMBER: 581B
PART 1 — GENERAL
1.01 SYSTEM DESCRIPTION
Outdoor rooftop- or slab-mounted, electrically controlled
heating and cooling utilizing a scroll compressor for cool-
ing duty and gas combustion for heating duty. Unit shall
discharge supply air vertically or horizontally as shown on
contract drawings.
1.02 QUALITY ASSURANCE
A. Unit shall be rated in accordance with ARI Standards 210/
240 or 360 and 270.
B. Unit shall be designed to conform to ASHRAE 15, latest
revision, and in accordance with UL 1995.
C. Unit shall be UL tested and certified in accordance with
ANSI Z21.47 Standard and UL listed and certified under
Canadian Standards as a total package for safety
requirements.
D. Roof curb shall be designed to conform to NRCA
Standards.
E. Insulation and adhesive shall meet NFPA 90A require-
ments for flame spread and smoke generation.
F. Unit casing shall be capable of exceeding Federal Test
Method Standard No. 141 (Method 6061) 500-hour Salt
Spray Test.
G. Each 581B unit is subjected to completely automated run
testing on the assembly line. Each unit contains a factory-
supplied printout indicating tested pressures, amperages,
data, and inspectors; providing certification of the unit
status at the time of manufacture.
1.03 DELIVERY, STORAGE, AND HANDLING
Unit(s) shall be stored and handled per manufacturer’s
recommendations.
PART 2 — PRODUCTS
2.01 EQUIPMENT (STANDARD)
A. General:
Factory-assembled, single-piece heating and cooling unit.
Contained within the unit enclosure shall be all factory
wiring, piping, controls, refrigerant charge (R-22), and
special features required prior to field start-up.
B. Unit Cabinet:
1. Unit cabinet shall be constructed of galvanized steel,
bonderized and coated with a baked enamel finish
on all externally exposed surfaces, and have primer-
coated interior surfaces on all panels.
2. Evaporator-fan cabinet interior shall be insulated with
a minimum
1
/
2
-in. thick flexible fiberglass insulation
coated on the air side. Aluminum foil-faced fiberglass
insulation shall be used in the heating compartment.
3. Cabinet panels shall be easily removable for
servicing.
4. Holes shall be provided in the base rails for rigging
shackles to facilitate overhead rigging, and forklift
slots shall be provided to facilitate maneuvering.
5. Unit shall have a factory-installed, sloped conden-
sate drain pan made of a non-corrosive material, pro-
viding a minimum
3
/
4
-in. connection with both vertical
and horizontal drains and shall comply with
ASHRAE 62.
6. Unit shall have factory-installed filter access panel to
provide filter access with tool-less removal.
7. Unit shall have standard thru-the-bottom power con-
nection capability.
C. Fans:
1. Indoor blower (evaporator fan) shall be of the
belt-driven, double inlet, forward-curved centrifugal
type. Belt drive shall include an adjustable-pitch
motor pulley.
2. Indoor blower (evaporator fan) shall be made from
steel with a corrosion-resistant finish and shall be
dynamically balanced.
3. Bearings shall be of the sealed, permanently lubri-
cated, ball-bearing type for longer life and lower
maintenance.
4. Condenser fan shall be of the direct-driven propeller
type and shall discharge air vertically upward.
5. Condenser fan shall have aluminum blades riveted to
corrosion-resistant steel spiders and shall be dynam-
ically balanced.
6. Condenser-fan motor shall be totally enclosed.
7. Induced draft blower shall be of the direct-driven, sin-
gle inlet, forward curved, centrifugal type, shall be
made from steel with a corrosion-resistant finish, and
shall be dynamically balanced.
D. Compressor(s):
1. Fully hermetic scroll type, internally protected.
2. Factory rubber-shock mounted and internally spring
mounted for vibration isolation.
3. On independent circuits (sizes 090-150).
E. Coils:
1. Evaporator and condenser coils shall have aluminum
plate fins mechanically bonded to enhanced copper
tubes with all joints brazed.
2. Tube sheet openings shall be belled to prevent tube
wear.
3. Evaporator coil shall be of the face-split design.
F. Heating Section:
1. Induced draft combustion type with energy saving
direct spark ignition system, redundant main gas
valve.
2. The heat exchanger shall be of the tubular section
type constructed of a minimum of 20 gage steel
coated with a nominal 1.2 mil aluminum-silicone alloy
for corrosion resistance.
3. Burners shall be of the in-shot type constructed of
aluminum coated steel.
4. All gas piping shall enter the unit cabinet at a single
location.
5. The Integrated Gas Control (IGC) board shall provide
timed control of evaporator fan functioning and
burner ignition. An LED (light-emitting diode) shall
provide diagnostic information. The LED shall be vis-
ible without removing the control box access panel.
6. IGC board contains anti-cycle protection for gas heat
operation (after 4 continuous cycles on high temper-
ature limit switch and one cycle on the flame rollout
switch).
G. Refrigerant Components:
Refrigerant circuit components shall include:
1. Fixed-orifice type feed system.
2. Refrigerant strainer.
3. Service gage connections on suction, discharge, and
liquid lines.
4. Filter drier.
5. Ability to route gage hoses through unit top cover
(unit sizes 036-072 only).
H. Filter Section:
1. Standard filter section shall consist of factory-
installed low-velocity, throwaway 2-in. thick fiberglass
filters of commercially available sizes.
2. Filter face velocity shall not exceed 300 fpm at nomi-
nal airflows.
3. Filter section shall use only one size filter.
4. Filters shall be accessible through an access panel
with ‘‘no-tool’’ removal.