Changing parameters during operation, Module data files, Configuration data – ProSoft Technology MVI71-MCM User Manual
Page 24
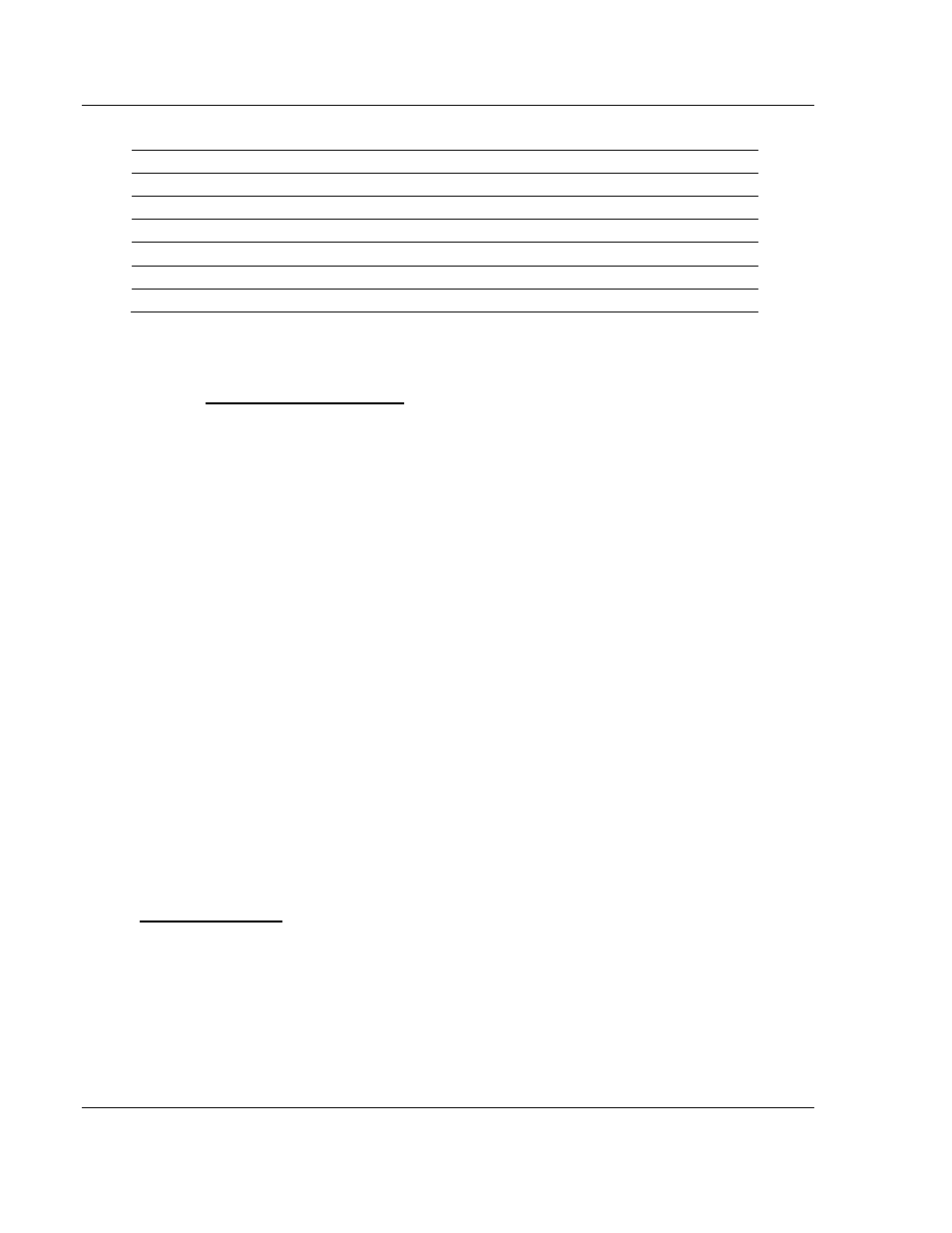
MVI71-MCM ♦ PLC Platform
Installing and Configuring the Module
Modbus Communication Module
Page 24 of 111
ProSoft Technology, Inc.
December 28, 2007
Read Block
Offset Description
Length
0 -2
1
1 9000
1
2
Module Configuration Errors
1
3
Port 1 Configuration Errors
1
4
Port 2 Configuration Errors
1
5 to 63
Spare
59
If there are any errors in the configuration, the bit associated with the error will be
set in one of the three configuration error words. The error must be corrected
before the module starts operating.
Refer to Configuration Error Codes (page 95) for a listing of error words
associated with invalid configuration blocks.
2.2.3 Changing Parameters During Operation
A copy of the module's configuration data is mapped in the module's database as
displayed in the table above. These values are initialized when the module first
receives its configuration from the PLC processor. Any node on the network can
change this data. A master port on the module may poll a slave for the data or a
slave port could receive the data from a remote master unit. The module will not
use this data until it is commanded. Ladder logic can be written to issue a Write
Configuration command block (9997) to the module. A remote device can set a
value of 9997 at address 6800 in the module to download the configuration to the
processor. Alternatively, the configuration/debug port on the module can be used
to issue the command directly to the module. All three of these methods will force
the module to download the configuration to the PLC processor. Ladder logic
must exist in the processor to accept the blocks sent by the module. If everything
is configured correctly, the module can receive its configuration from a remote
device.
2.2.4 Module Data Files
All data related to the MVI71-MCM is stored in user-defined data files. The user
is responsible for setting up the data areas to match the specific application for
the module. Each data area is discussed in the following topics.
Configuration Data
Configuration of the module is performed by filling in a user-defined data table. In
the example ladder logic (block transfer), file N10 stores the general module
configuration information. N11 stores the command list for Port 1. N12 stores the
command list for Port 2. Each register in the files has an associated symbol and
description to aid in filling in the data. The Reference chapter contains a list of
items that must be configured for the module and their associated location in the
file. When the side-connect interface is used, the file used for configuration must
match that set in the SC_DATA.TXT file using the setdnpsc.exe program.