Fig.2 fig.3 fig.4, Operation, Asymmetrical dipped beam – Sealey HBS2010 User Manual
Page 2: Symmetrical dipped beam
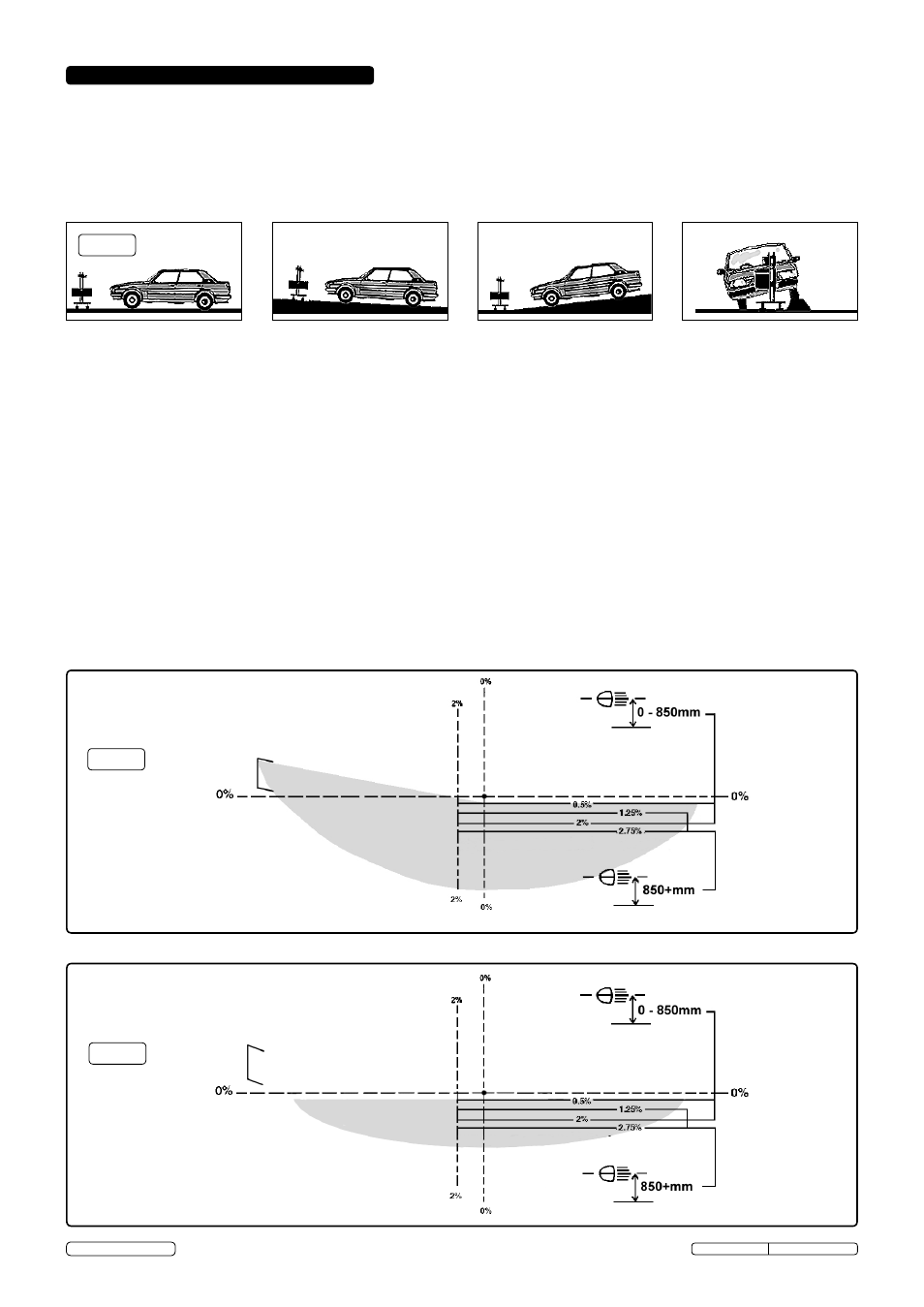
4.2. CHECKING BEAM SETTING
4.2.1. Position the Beam Setter approximately 200 to 500mm from one of the vehicle's headlamps.
4.2.2. Stand behind the Beam Setter and looking through the aligner, align with two symmetrical points on the vehicle i.e. the
bonnet lip or the bottom of the windscreen.
4.2.3. Ensure the line is parallel with the horizontal, or symmetrical selection, by rotating the Beam Setter. This will ensure that it is
square with the vehicle.
4.2.4. Measure the height of the centre of the headlamp from the floor.
4.2.5. Squeeze the release lever whilst supporting the light box and move the light box up or down the column as required until the centre
of the lens is at the same height as the headlamp. Release the release lever.
4.2.6. use the white central sighting line on top of the light box housing to align the Beam Setter with the centre of the headlamp.
4.2.7. If necessary, start the vehicle's engine so that the battery is not drained during the procedure.
Note: When checking headlamp aim on vehicles with hydropneumatic suspension systems, it is necessary to have the engine
idling.
4.2.8. Switch the headlamps on to dip beam.
4.2.9. Determine the appropriate dip beam image and the aim (see figs.3 and 4). Headlamps of older vehicles (approx. pre 1950)
may have beam images which do not conform. In such cases check:
a)
DIp BEAM headlamps are aimed so that they do not dazzle, i.e. the brightest part of the beam image is aimed at least 0.5%
below
the horizontal (fig.5), or for headlamps which cannot be checked on dip beam, check:
b)
MAIN BEAM headlamps are aimed so that the beam image centre is on or slightly below the horizontal (fig.5).
OK
NO
NO
3.0° MAX
4.1. SET-Up
4.1.1. Position the vehicle on the designated headlamp aim standing area, when positioning the Beam Setter, ensure that the floor is even
and level, if this is not possible the vehicle and Beam Setter
must be on the same slope, which must not exceed 3.0°. Headlights must
not be checked where surface angle exceeds 3.0° (fig.2).
4.1.2. Straighten the vehicle's wheels and check that the tyre pressures are correct.
4.1.3. Ensure the headlights are clean and dry.
4.1.4. If the vehicle is fitted with manual or electric headlamp levelling device, ensure that it is set for the vehicle with a normal load.
4.1.5. Remove anything which could alter the attitude of the vehicle, i.e. a heavy load in the boot.
4. OpERATION
Correct projection on panel.
ASYMMETRICAL DIppED BEAM
When testing symmetrical dipped beams, the
correct light projection on the plate should be
on the line 0.5%
SYMMETRICAL DIppED BEAM
fig.2
fig.3
fig.4
Original Language Version
HBS2010.V2 Issue: 1 - 14/02/13
© Jack Sealey Limited