Operation – Sealey TA302 User Manual
Page 3
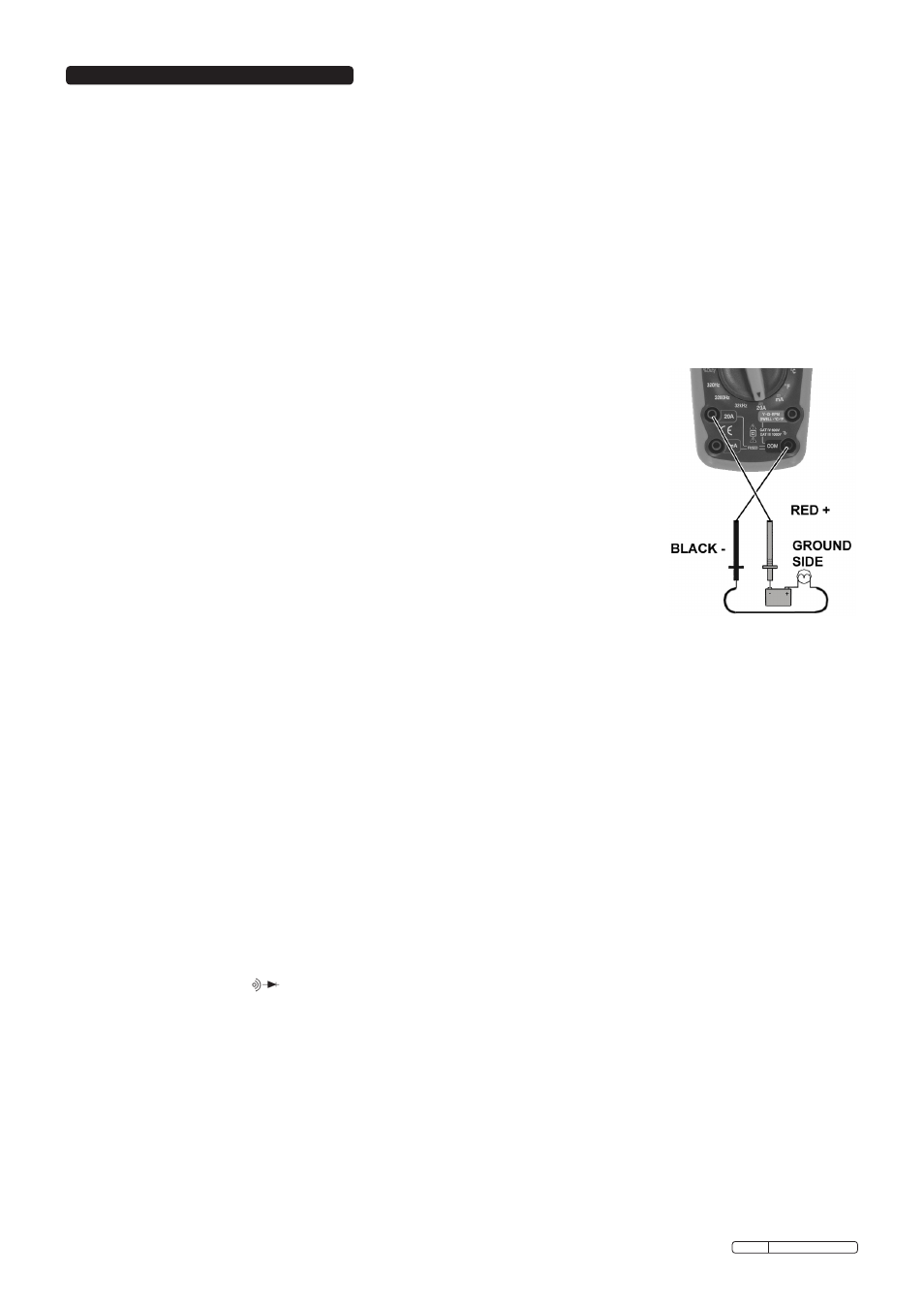
4. oPerAtion
WArning! Ensure that you read, understand and apply the safety and operational instructions before connecting the meter. Only when you are sure that
you understand the procedures is it safe to proceed with testing.
WArning! Risk of electrocution. High voltage circuits, both AC and DC are very dangerous and should be measured with great care.
Operating temperature range 0
°C to 40°C.
remember to turn on meter before use and to turn it off when measurement is completed.
note: IF “OL” appears in the display during a measurement, the value exceeds the range you have selected. Change to a higher range.
note: On some low AC and DC ranges, with the test probes not connected to a device, the reading may show a random fluctuating reading. This is
normal and is caused by the high input sensitivity. The reading will stabilise and give a proper measurement when connected to a circuit.
4.1.
Alternate function Button (fig.1.2)
4.1.1. Press the Alternate Function button to toggle between AC and DC in the voltage & current measurements.
Press the Alternate Function button to toggle between Continuity and Diode Test.
4.2.
dwell Button (fig.1.3)
4.2.1. To manually scroll through to the correct number of cylinders press the Dwell button.
4.3.
data hold, (fig.1.10)
4.3.1. The data hold function allows the meter to freeze a measurement reading for later reference.
4.3.2. Press the data hold button once to freeze the reading in the display. The indicator “hold” will appear in the display.
4.3.3. Press the data hold button again to return to normal operation.
4.4.
range Button (fig.1.8)
4.4.1. The range is automatically selected by the meter.
4.4.2. To manually select a range within a function, press the range button.
4.4.3. To exit the range mode and return to autoranging, press and hold the range button for two seconds.
note: If the range is too high, the meter will be less accurate.
If the range is too low, the meter displays ‘OL’ (Over Limit).
4.5.
rPm mode Button (fig.1.4)
4.5.1. Press RPM Mode button to toggle between 4 stroke and 2 stroke / DIS (Distributerless Ignition System).
4.5.2. Press and hold for two seconds to toggle between negative (-) and Positive (+) Trigger slope.
4.5.3. Press the button repeatedly to adjust the trigger level if the meter reading is to high or unstable.
note: The Trigger level has five steps and is different for each function combination.
4.6
Backlight button (fig.1.9)
4.6.1
To turn the backlight on press the Backlight button, to turn off press the backlight button again.
4.7.
AC or dC voltage measurements
4.7.1.
Insert the black test probe into the negative “COM” terminal and the red test probe into the positive main positive
terminal (fig.1.10) terminal.
4.7.2. Turn the rotary switch to the ‘V’ position.
4.7.3. Press the Alternate Function button to select AC or DC voltage.
4.7.4. Touch the test probes to the circuit under test and read the voltage display.
4.8.
AC or dC Current measurements
WArning! do not make current measurements between 1A and 20A for longer than 30 seconds in every 15 minutes. exceeding 30 seconds
may cause damage to the meter and test probes.
4.8.1. Insert the black test probe into the into the negative “COM” terminal and the red test probe into the:
a) Positive 20A terminal for currents to 20A (fig.1.6).
b) Positive mA terminal for currents to 320mA (fig.1.7).
note: If you are unsure of the current draw select the 20A terminal.
4.8.2. Turn the rotary switch to the 20A or mA position.
4.8.3. Press the Alternate Function button to select AC or DC current.
4.8.4. Touch the test probes in series (fig.2) with the circuit under test and read the current on the display.
4.9.
resistance
WArning! to avoid electric shock, disconnect power to unit under test and discharge all capacitors before taking any resistance
measurements.
WArning! ohms cannot be measured if a voltage is present. only measure in non powered circuits.
4.9.1. Insert the black test probe into the negative “COM” terminal and the red test probe into the positive main positive terminal (fig.1.10) terminal.
4.9.2. Turn the rotary switch to the Ω position.
4.9.3. Connect the test probes to the two ends of the Resistance circuit to be measured.
4.9.4. Read the measured value from the display.
4.9.5. In resistance measurements, if greater accuracy is required press the Range button.
4.10.
diode / Continuity measurements
WArning! to avoid electric shock, disconnect power to unit under test and discharge all capacitors before taking any resistance
measurements.
4.10.1. Insert the black test probe into the negative “COM” terminal and the red test probe into the positive main positive terminal (fig.1.10) terminal.
4.10.2. Turn the rotary switch to the position.
4.10.3. Press the Alternate Function button (fig.1.2) to select Diode or Continuity.
4.10.4. Connect the test probes to the two ends of the Diode or Continuity circuit to be measured.
4.10.5. Read the measured value from the display.
4.10.6. When measuring the forward voltage across a good Diode, it will indicate 0.4V or 0.7V and the reverse voltage will indicate “OL” (same as on open
condition). For a short circuit diode, a value of 0mV will be displayed.
4.10.7. In continuity mode a complete circuit will beep continuously, if open circuit, there will be no beep.
4.11.
frequency (Hz)
4.11.1. Insert the black test probe into the negative “COM” terminal and the red test probe into the positive main positive terminal (fig.1.10) terminal.
4.11.2. Turn the rotary switch to either of the “Hz” positions (320Hz, 3200Hz, 32kHz).
4.11.3. Connect the negative “COM” test probe to ground.
4.11.4. Connect the positive main positive terminal (fig.1.10) test probe to the “signal out” wire of the sensor to be tested.
4.12.
duty Cycle (%)
4.12.1 Insert the black test probe into the negative “COM” terminal and the red test probe into the positive main positive terminal (fig.1.10) terminal.
4.12.2. Select the %DuTY range with the rotary switch.
4.12.3. Connect the negative test probe to ground.
4.12.4. Connect the positive test probe to the signal wire circuit.
fig.2.
Original Language Version
TA302 Issue: 2 - 20/12/11