Fig.9, Fig.10 – Sealey SM35CE User Manual
Page 5
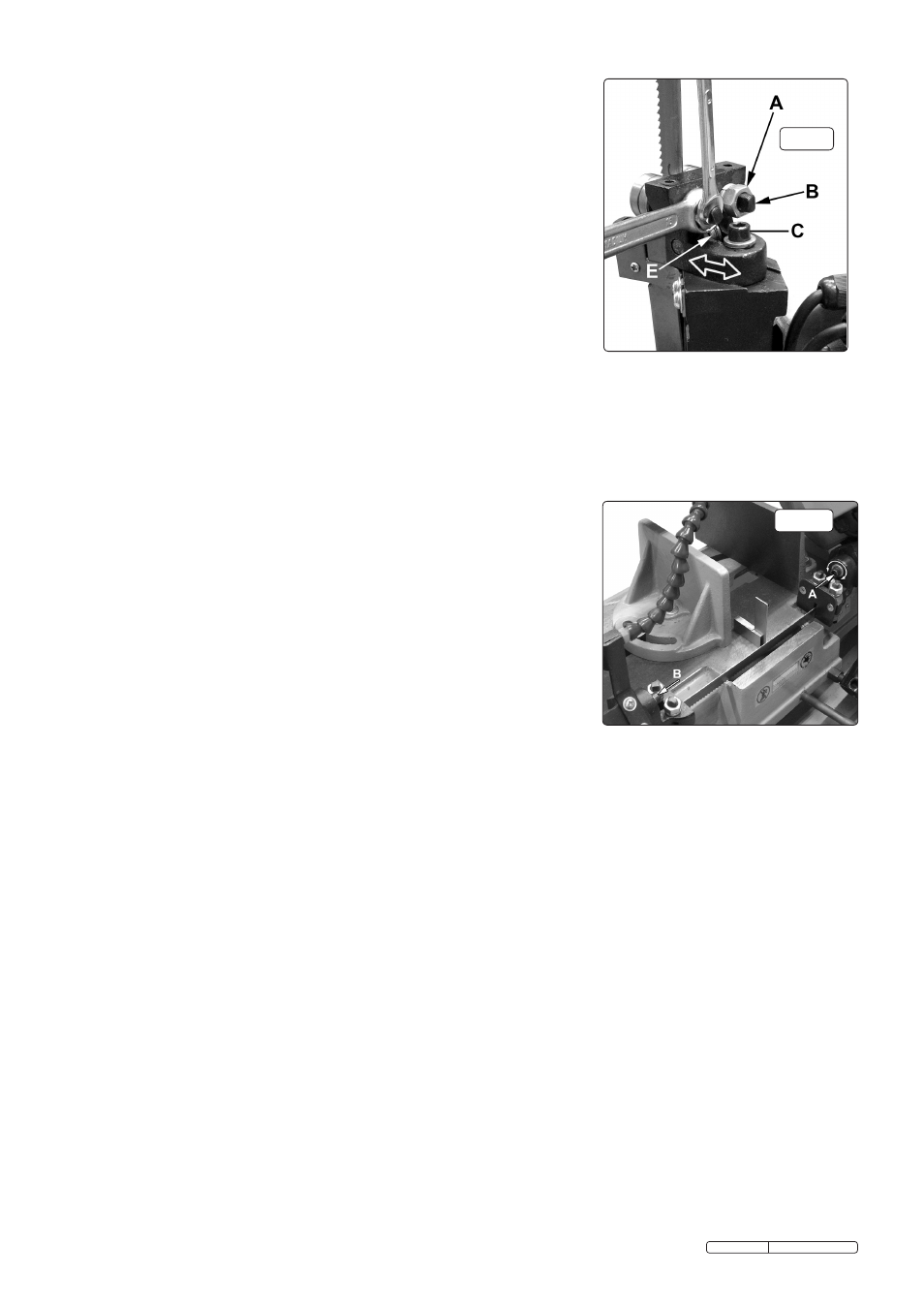
fig.9
Original Language Version
SM35CE.V4 Issue: 4 - 14/12/11
fig.10
4.9.
TENSIONING THE BLADE.
WARNING! DO NOT over tighten the blade as this may cause the blade to stretch
and warp.
Note:
Blade tension is important for the correct operation of the saw. The correct blade
tension is 700 to 900kg as measured on a blade tension guage. To set the blade
tension without the use of a gauge do the following.Tension the blade slightly to remove
any sag in the blade between the two wheels by turning the knob (fig.8E) clockwise but
as you do so make sure that the back edge of the blade is close to the rim of both
pulleys. Check that the blade is seating properly by turning the pulleys by hand until you
have observed a full rotation of the blade.
4.9.1. Once the blade is properly aligned increase the tension by turning the knob one and
three quarter to two revolutions clockwise. This equals approximately 800kg blade
tension.
4.9.2. Replace the upper and lower blade guards.
4.9.3. Close the blade protection safety cover and secure it with the two screws.
4.9.4. Loosen the two screws on the lower blade wheel protection cover and slide it
downwards so that the lower blade wheel is completely covered. Tighten the screws.
4.9.5. Reconnect the saw to the power source and run it for two to three minutes to seat the
blade.
4.9.6. Disconnect the saw from the mains power supply and open the safety covers again.
4.9.7. Loosen the blade until it just begins to sag.
4.9.8. Tighten blade again until it just becomes straight between the blade wheel with all sag
eliminated.
4.9.9. Further tighten the blade by turning the tension knob two full revolutions. The blade is
now properly tensioned and ready for use.
4.9.10. Close and secure safety covers.
4.9.11. After fitting a new blade the tracking should be checked as described in section 4.7.1
4.10. BLADE GUIDE BEARING ADJUSTMENT
WARNING! This machine is designed and intended for use with blades that are
0.8/0.9mm thick by 19mm wide by 2362mm long. Use of blades with a different
specification may cause inferior performance.
4.10.1. Correct guide bearing adjustment is important so that the blade runs smoothly and
evenly without twisting or snagging anywhere along its path.
4.10.2. Raise arm to vertical position and lock in place by turning off the hydraulic cylinder
valve.
4.10.3. For greater visibility and ease of adjustment the protective plate directly over the
guide bearings can be temporarily removed.
4.10.4 Loosen the hex socket cap screw (see fig.9C) in order to adjust the position of the
back roller bearing (see fig.9E). The bearing should be 0.08mm to 0.12mm from
the back of the blade.
4.10.5. Each of the outer guide bearings is mounted on an adjustable eccentric bushing.
Loosen the lock nut (see fig.9A) with a 16mm ring spanner whilst holding the adjuster
‘B’ with an 6mm open ended spanner.
4.10.6. Turn the adjuster to adjust the bearing. The bearing should barely touch the blade
(0.001”). This clearance can be measured with a piece of thin paper which should
just fit into the gap between the bearing and the blade. Tighten the lock nut when
satisfied with the bearing adjustment.
4.10.7. Adjust both outer guide bearings. When satisfied that the adjustment is accurate,
carefully turn the blade wheels by hand to see if the blade snags or rubs at any
point. Re-adjust bearing(s) if necessary.
4.11. ADJUSTING BLADE TO BE 90° TO THE BED.
4.11.1. Disconnect the machine from the power supply.
4.11.2. Place an engineer’s set square onto the bed touching the blade as shown in fig10.
The blade should make contact with the square across its entire width.
4.11.3. If adjustment is necessary loosen the socket cap screws as shown in fig.10A&B and
rotate both blade guide assemblies slightly in the same direction until the blade makes
contact with the square across its entire width.
4.11.4. Tighten bolts A & B.
4.11.5. Having made this adjustment the blade guide bearing adjustments should be
checked again as detailed in section 4.10.