HEIDENHAIN TNC 640 (34059x-05) User Manual
Page 478
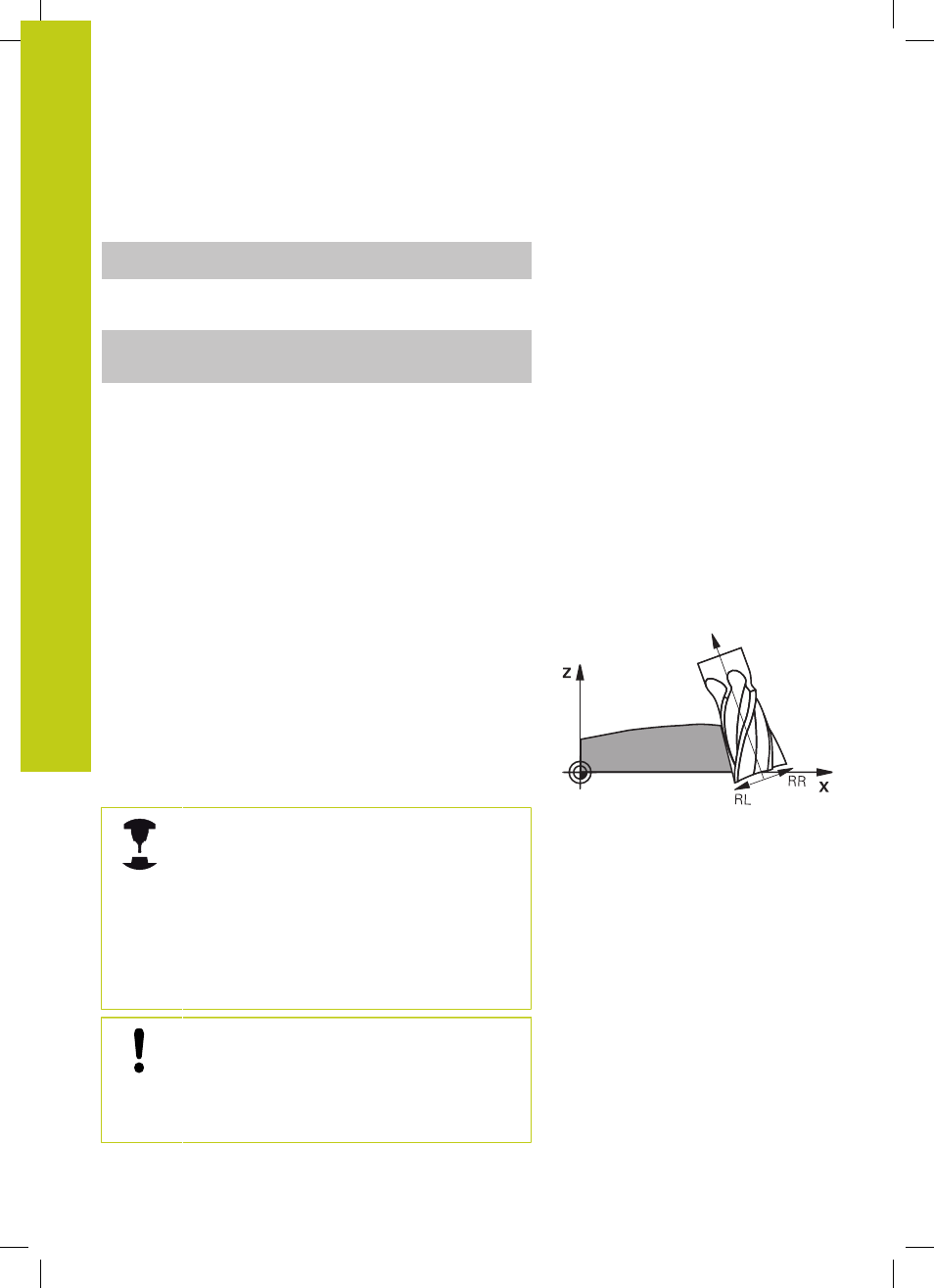
Programming: Multiple Axis Machining
12.6 Three-dimensional tool compensation (Option #9)
12
478
TNC 640 | User's Manual
HEIDENHAIN Conversational Programming | 1/2015
Example: Block format with surface normals without tool
orientation
LN X+31.737 Y+21.954 Z+33.165 NX+0.2637581 NY+0.0078922
NZ–0.8764339 F1000 M128
Example: Block format with surface normals and tool
orientation
LN X+31.737 Y+21.954 Z+33.165 NX+0.2637581 NY+0.0078922
NZ–0.8764339 TX+0.0078922 TY–0.8764339 TZ+0.2590319
F1000 M128
LN:
Straight line with 3-D compensation
X, Y, Z:
Compensated coordinates of the straight-line
end point
NX, NY, NZ:
Components of the surface-normal vector
TX, TY, TZ:
Components of the normalized vector for
workpiece orientation
F:
Feed rate
M:
Miscellaneous function
Peripheral Milling: 3-D radius compensation with
TCPM and radius compensation (RL/RR)
The TNC displaces the tool perpendicular to the direction of
movement and perpendicular to the tool direction by the sum of
the delta values
DR (tool table and TOOL CALL). Determine the
compensation direction with radius compensation
RL/RR (see
figure, traverse direction Y+). For the TNC to be able to reach the
set tool orientation, you need to activate the function
M128, see
"Maintaining the position of the tool tip when positioning with tilted
axes (TCPM): M128 (Option #9)", page 464. The TNC then positions
the rotary axes automatically so that the tool can reach the defined
orientation with the active compensation.
This function is possible only on machines for which
you can define spatial angles for the tilting axis
configuration. Refer to your machine manual.
The TNC is not able to automatically position the
rotary axes on all machines.
Refer to your machine manual.
Note that the TNC makes a compensating
movement by the defined
delta values
. The tool
radius R defined in the tool table has no effect on the
compensation.
Danger of collision!
On machines whose rotary axes only allow limited
traverse, sometimes automatic positioning can
require the table to be rotated by 180°. In this case,
make sure that the tool head does not collide with
the workpiece or the clamps.