HEIDENHAIN TNC 640 (34059x-05) User Manual
Page 453
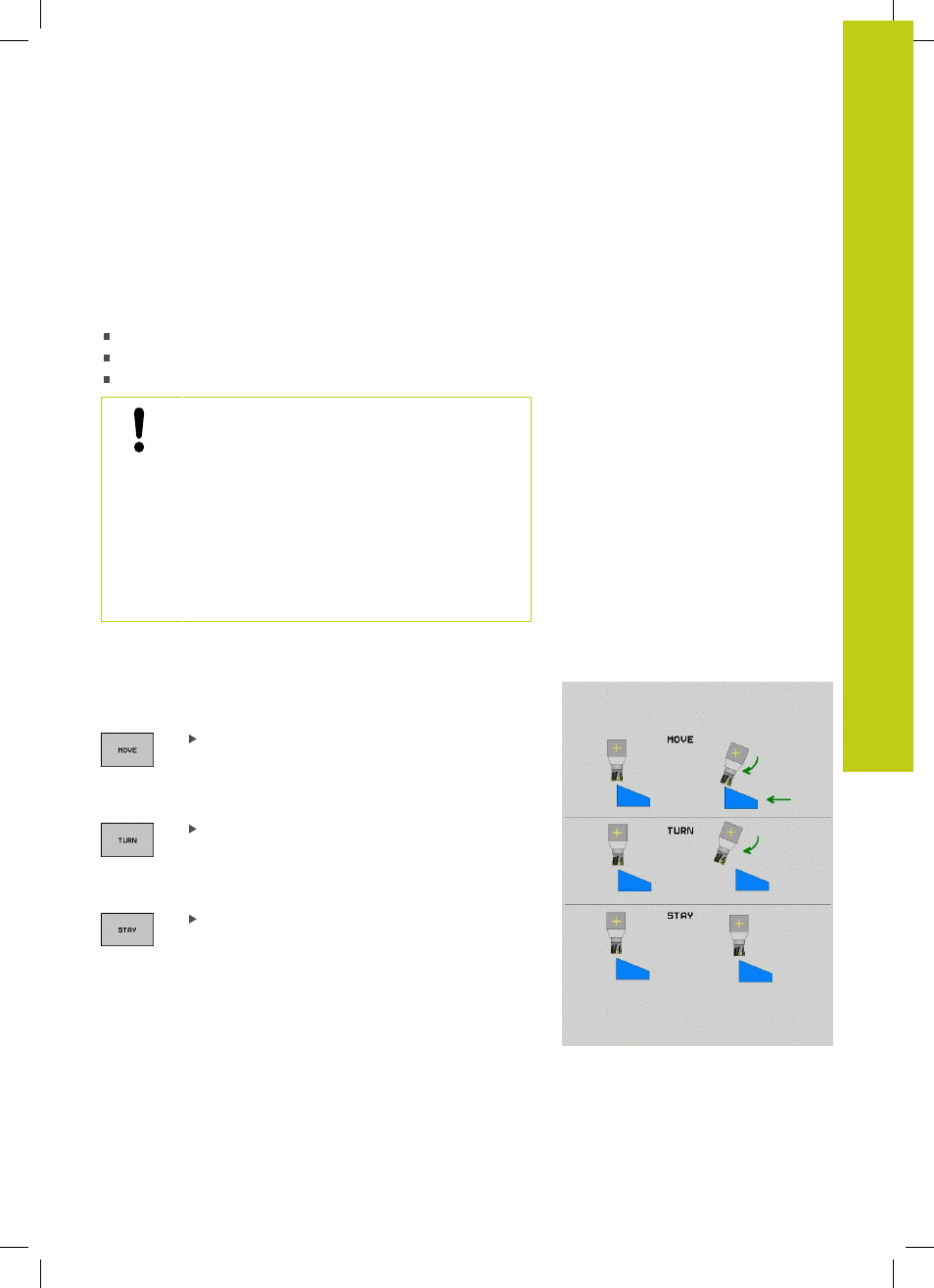
The PLANE Function: Tilting the working plane (Software Option 8) 12.2
12
TNC 640 | User's Manual
HEIDENHAIN Conversational Programming | 1/2015
453
Specifying the positioning behavior of the PLANE
function
Overview
Independently of which PLANE function you use to define the tilted
machining plane, the following functions are always available for
the positioning behavior:
Automatic positioning
Selection of alternate tilting possibilities (not with
PLANE AXIAL)
Selection of the type of transformation (not with
PLANE AXIAL)
Danger of collision!
If you work with Cycle 8
MIRROR IMAGE in a tilted
system, please note the following:
Program the tilting motion first and then define Cycle
8MIRROR IMAGE.
Mirroring a rotary axis with Cycle
8 only mirrors the
motions of the axis, but not the angles defined in the
PLANE functions. As a result, the positioning of the
axes changes.
Programs created on an iTNC 530 or on earlier TNCs
are not compatible.
Automatic positioning: MOVE/TURN/STAY (entry is
mandatory)
After you have entered all parameters for the plane definition,
you must specify how the rotary axes will be positioned to the
calculated axis values:
The PLANE function is to automatically position
the rotary axes to the calculated position values.
The position of the tool relative to the workpiece
is to remain the same. The TNC carries out a
compensation movement in the linear axes
The PLANE function is to automatically position
the rotary axes to the calculated position values,
but only the rotary axes are positioned. The TNC
does
not
carry out a compensation movement in
the linear axes
You will position the rotary axes later in a separate
positioning block
If you have selected the
MOVE option (PLANE function is to position
the axes automatically), the following two parameters must still be
defined:
Dist. tool tip – center of rot. and Feed rate? F=.
If you have selected the
TURN option (PLANE function is to position
the axes automatically without any compensating movement), the
following parameter must still be defined:
Feed rate? F=.
As an alternative to defining a feed rate
F directly by numerical
value, you can also position with
FMAX (rapid traverse) or FAUTO
(feed rate from the
TOOL CALLT block).