Instructions for use, Starting situation, Fabricating the framework – Ivoclar Vivadent IPS Classic User Manual
Page 11: Oxide firing
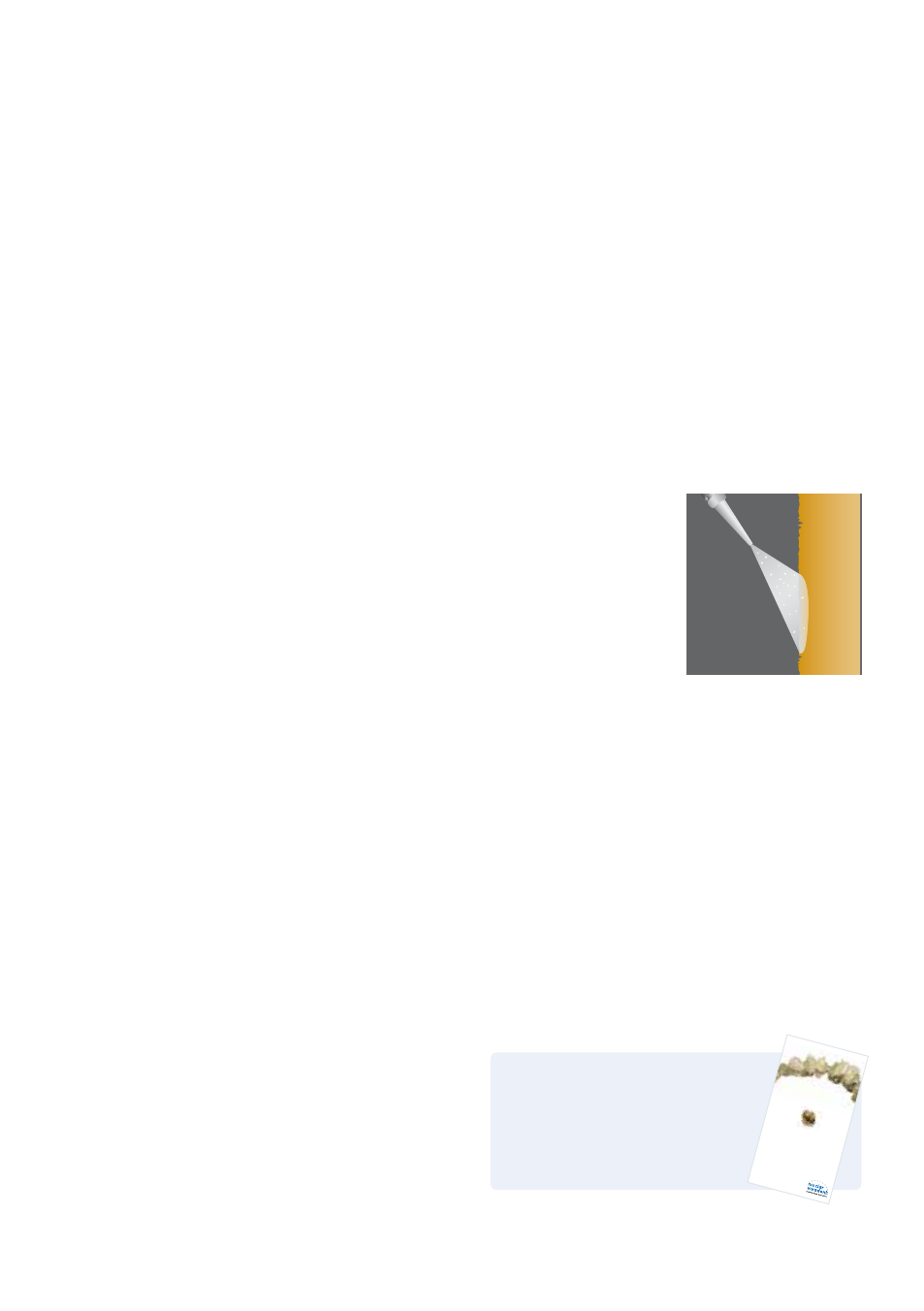
11
Instructions for Use
Starting situation
Fabricate a master model or a model with detachable segments
on the basis of the impression in the usual manner. It is advisable
to apply a sealer to harden the surface and to protect the die.
The application of a sealer must not cause any changes in the
dimensions of the die. After that, a spacer may be applied in the
usual manner.
Fabricating the framework
When fabricating the framework, make sure that the minimum
wall thickness after finishing is 0.3 mm for single crowns and 0.5
mm for bridge abutments. These dimensions are the prerequisite
for the stability of the metal framework and the durable bond
between the metal and ceramic material. If the stipulated
framework and connector dimensions are not observed, the
resulting stress within the material will lead to delamination of
the ceramic material and distortion of the framework.
Recommended procedure
1. Complete modelling of the anatomical tooth shape
2. Reduce to make room for the veneering materials
3. Waxing of the contact points and connector areas
4. Checking the occlusal and proximal contact points
Contouring
The framework reflects the reduced anatomical tooth shape
(functional support of the veneering ceramic). In this way, the
ceramic material may be applied in even layers and is adequately
supported. For that purpose, the properties of the different alloys
(e.g. firing stability) must be taken into consideration.
– Undersized metal frameworks result in increased shrinkage of
the veneering ceramic and require additional corrective firings.
– If the metal framework is too small, the
veneering ceramic is not adequately supported, which may
lead to cracks and delamination,
particularly in very thick ceramic layers.
Finishing the metal framework
The cast metal framework is finished using tungsten carbide
metal burs or ceramic-bonded grinding instruments. The marginal
area of the framework is reduced up to the inner edge of the
chamfer or shoulder preparation (labial or circular) to make room
for the ceramic shoulder.
– Use reduced pressure when working with softer alloys.
– Work in one direction only to avoid overlapping and inclusions
in the metal surface.
– Do not use diamond grinding instruments. Diamond particles
may be trapped in the alloy and cause bubbles in the ceramic
material during firing.
Oxide firing
After grinding, carefully blast the framework with Al
2
O
3
50 – 100 μm. The required pressure is 1.5 – 2.0 bar.
– Use only disposable, pure Al
2
O
3
to blast the alloy surface.
– Observe the Instructions for Use of the alloy manufacturer.
Blasting improves the mechanical bond. It results in the object
surface being roughened and considerably enlarged. In order to
prevent inclusions of blasting medium residue in the ceramic, we
recommend blasting the alloys with the indicated pressure while
keeping the nozzle at a flat angle to the object surface. A
contaminated metal surface may result in the formation of
bubbles during ceramic firing. When finishing the frameworks,
the instructions of the alloy manufacturer must be observed at all
times. Oxidation is carried out according to the instructions of the
alloy manufacturer.
Schematic diagram of the
blasting direction
Correct angle
for blasting the alloy
surface
Before the oxidation firing, clean the metal framework using a
brush under running water. Then, thoroughly clean it with steam
or in the ultrasonic cleaner. Allow the framework to dry after
cleaning. Oxidize the framework according to the instructions
given by the alloy manufacturer. Provide ample support for the
framework on the firing tray. This is particularly important for
long-span bridges. After oxidation, carefully check the framework
for porosity or irregular oxide layer. Refinish and reoxidize if
necessary.
Please refer to the “Framework Design
Guidelines for Metal-Ceramic
Restorations” for additional
information on framework design.
They can be ordered from your
Ivoclar Vivadent contact address.
F R A M
E W O
R K D
E S I G
N
f o r
m e t a l
-
c e r a m
i c
r e s t o
r a t i o
n s
Manual