3 flow‐bus protocol description – Bronkhorst RS232 interface User Manual
Page 10
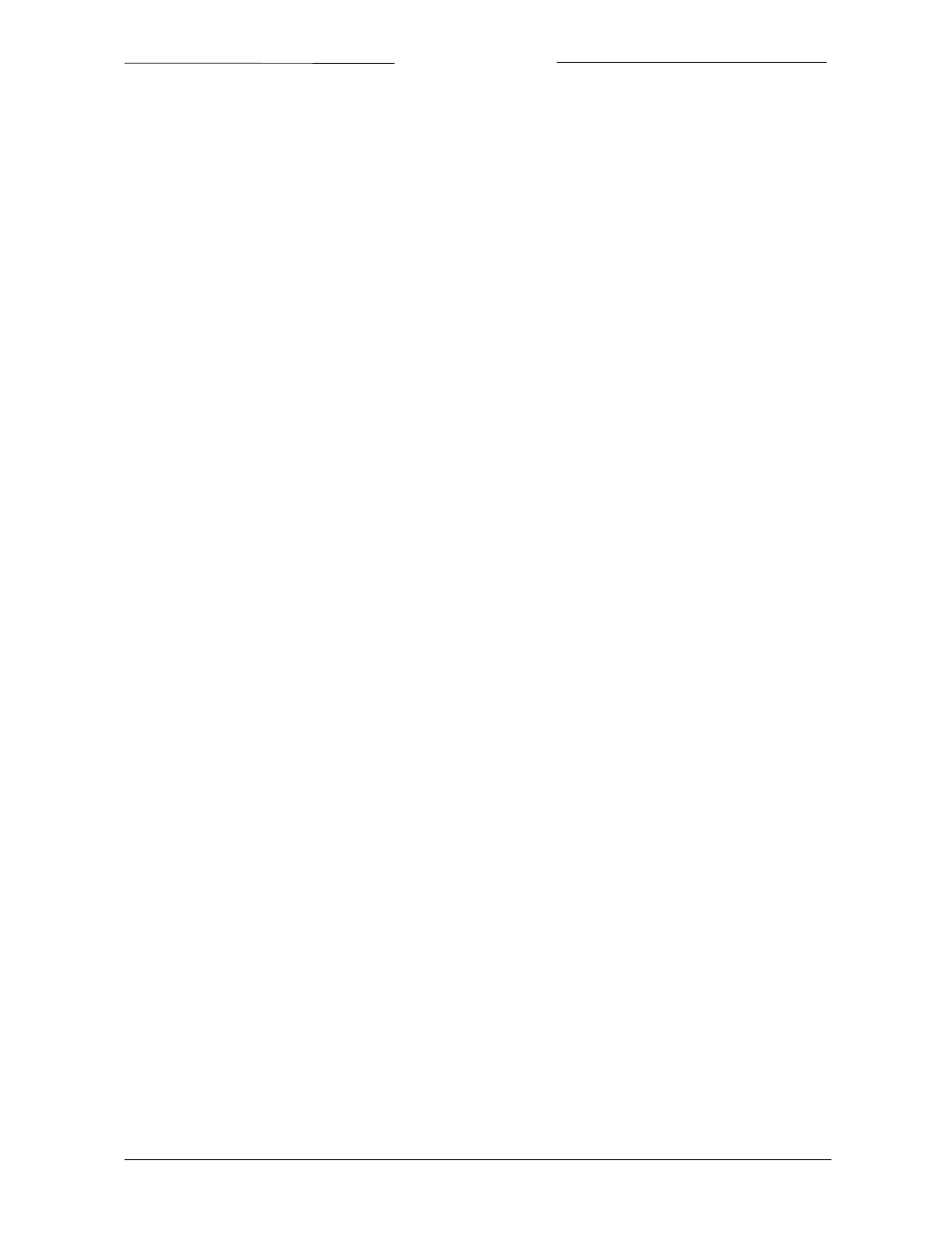
BRONKHORST
®
Page 10
RS232 interface
9.17.027
3 FLOW‐BUS PROTOCOL DESCRIPTION
3.1
G
ENERAL
On the highest supported communication level, you may use DDE‐channels for Windows application‐programs with
this facility. On a lower communication level, you can use the FLOWB32.DLL, for changing parameter values.
To read and write parameter values from or to FLOW‐BUS devices directly through the available interfaces there is a
special protocol for messages between these devices. When operating a FLOW‐BUS system with a HOST computer,
you need to know this message protocol if you choose to drive the interfaces directly.
When you use a type of RS232/FLOW‐BUS interface (baud rate up to 38K4) you may first have to initialise the
interface. This can be done by means of sending some ASCII‐strings to the interface through RS232.
See also paragraph “Initialising RS232/FLOW‐BUS interface”
There are two different communication protocols for the PC and the RS232 HOST:
an ASCII protocol for communication that is compatible with existing FLOW‐BUS applications.
This protocol serves only one master/slave dialog at a time.
an enhanced binary protocol that supports concurrent sending of messages to different nodes. This protocol
contains a message‐sequence number and serves more than one master/slave dialogs at a time.
The RS232‐HOST module automatically recognises the protocol used by the PC and adapts its behaviour to the
protocol in use. The type of protocol is determined by the first character of a message.
The first character is ‘:’
(0x3A) existing type of message.
The first character is DLE
(0x10) enhanced type of message.
Via the FLOW‐BUS DLL (FLOWB32.DLL) the PC determines which protocol is in use.
The communication relation is always master (PC) and slave (HOST). The HOST will always respond on a request from
the PC.
3.2
I
NITIALISATION OF LOCAL HOST INTERFACES ON
M
ULTIBUS INSTRUMENTS
When you use a digital instrument with RS232 interface, baud rate is fixed on 38K4 baud and no special initialisation is
needed. Through the serial line connected to a COM‐port of your computer or to a PLC you have to communicate with
the instrument using the FLOW‐BUS protocol. Each instrument has its own node address (3...120). If you want to send
a message to the instrument you have to know this node address. However, if you send a message to node address
128 the instrument will always respond to your message. On a point‐to‐point connection like RS232 it is the easiest
way to make the communication work under all circumstances (it is independent of the real node address of the
instrument).