American Dryer Corp. AD-100 User Manual
Page 51
Attention! The text in this document has been recognized automatically. To view the original document, you can use the "Original mode".
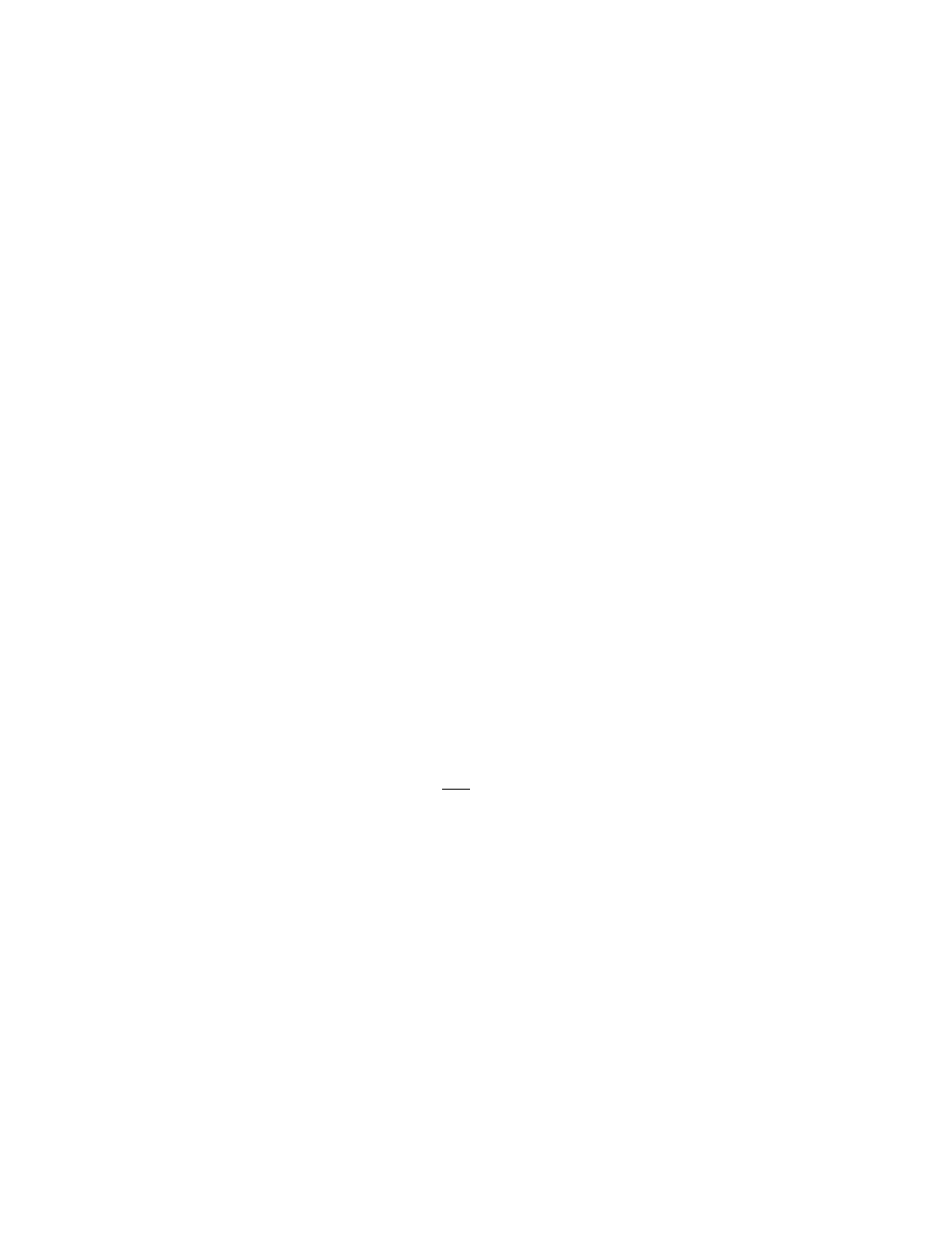
doors for periodic clean-out of lint from the main duct.
If it is not feasible to provide separate exhaust ducts for each dryer, ducts
from the individual dryers may be channeled into a common main duct. The
individual ducts should enter the bottom or side of the main duct at an angle
not more than 45 degrees and should be spaced at least 4 6 " apart. The main
duct should be tapered, with the diameter increasing before each individual
duct is added. The minimum increase in cross-section area sliould be 115 square
inches for each 12" duct added and 205 square inches for each 16" duct added.
I'Jhere rectangular main ducting is used the areas shown should be increased 10
square inches, and the ratio of duct width to depth should not be greater than
3 1/2 to 1. Figure 1 shows the minimum cross-section areas of the main duct for
either 12" or 16" dryer ducts. These figures should be increased if the main duct
is unusually long (20' or over) or has numerous elbows in it.
Openings from the outside air to the room in which the dryers are operating should
be provided for make-up air and located as near to each dryer as possible. These
openings should be 3 to 4 times the cross-section area of the exhaust ducts.
Inadequate exhaust facilities may cause high temperature limit switches or air flow
switches to shut off the dryers. Do not disable the switches, which are provided
for your safety. Instead, investigate the exhaust ducting. Any obstruction or
air friction due to numerous elbows/fittings in the ducting will slo\v7 the passage
of air through the system with resulting inefficiency and potential fire hazard.
10-3