Section vi installatiqn, Exhaust duct fresh air supply, Uncrating – American Dryer Corp. AD-100 User Manual
Page 3: Location of d^er, Dryer enclosure, Electrical rover connectors
Attention! The text in this document has been recognized automatically. To view the original document, you can use the "Original mode".
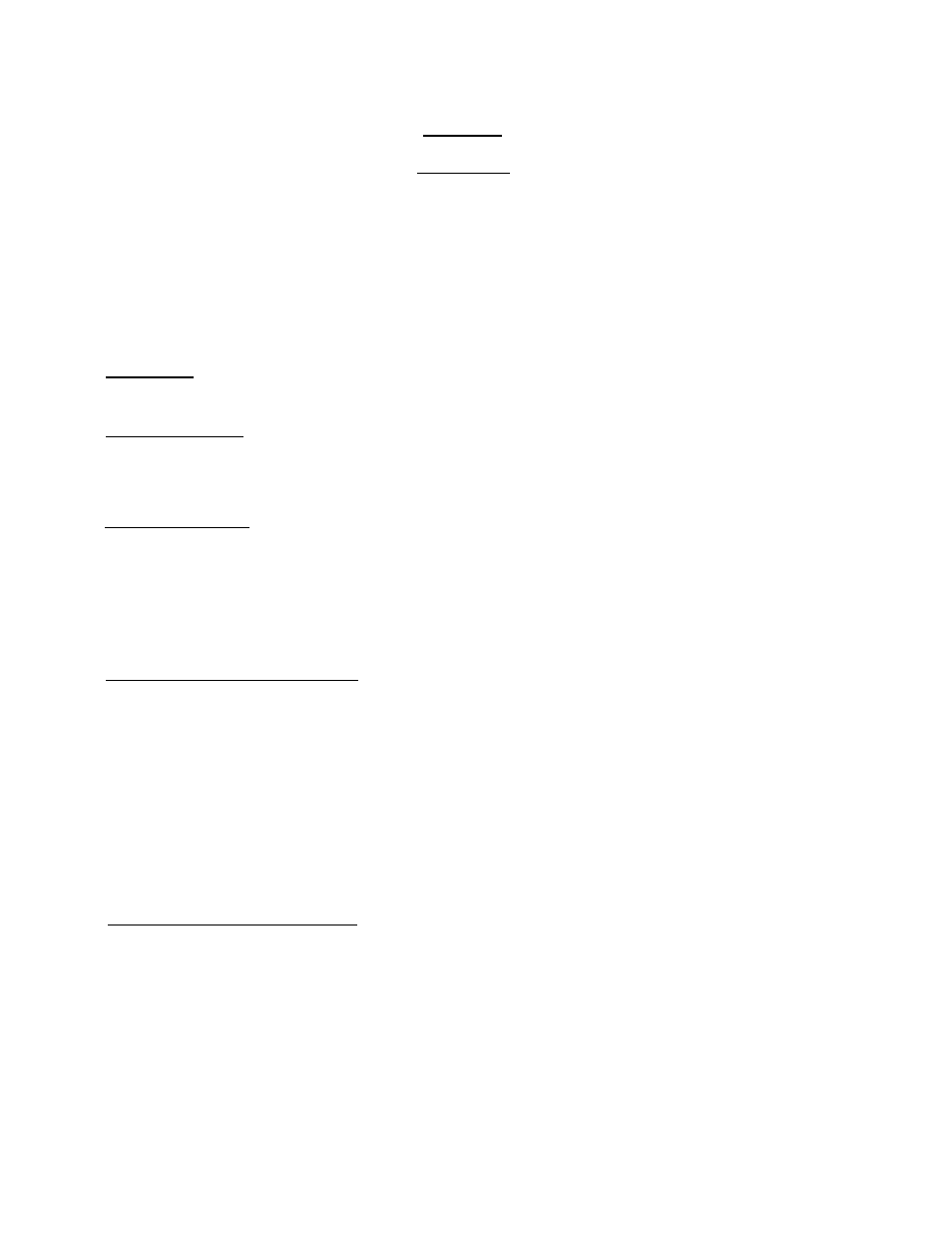
SECTION VI
INSTAllATIQN
Except where conditions do not allow, the dryer should be handled in an upright
position at all times. The console may be removed from the base after uncrating
(See Figure 3 and 4, Page 10-5) if headroom is limited. Installation should be
performed by competent technicians in accordance with local and state codes. In
the absence of these codes, installation must conform to applicable American
National Standards: ANSI Z223.1-1974 (National Fuel Gas Code) or ANSI Cl-1978
National Electric Code).
UNCRATING.
Remove slatted crating, sidewall sills, protective cover, and all
packing materials. Remove front and rear skid runners (2 bolts. . .each runner).
LOCATION OF D^ER.
to rear wall for e
IVbve the dryer into position. (Allow two feet of clearance
ease of installation and possible future servicing. Level the
dryer by using metal shims under the 4 support plates (See Figure 4, Page 10-5).
Shims should not be less than 4 inch squares.)
DRYER ENCLOSURE.
Adjacent structures should be made of non-combustible materials.
A minimum clearance of 5 inches is suggested between dryers or adjacent sidewall
structures. Head clearance should not be less than 15 inches, except along the
front of the console which may be closed in if desired. (Allowance must be made
for opening the control door.) Minimum clearances of 0 inches are permitted from
floor, sides, and rear of dryer, and 6 inches from top of dryer to nearest combustible
surfaces.
EXHAUST DUCT FRESH AIR SUPPLY.
on Page 10-2.
Exhaust duct requirements are discussed
Air supply must be given careful consideration to assure proper performance of each
dryer. An unrestricted source of air to provide for 1700 to 2100 cfm is proper for
all models except the super steam dryer which requires a 3000 cfm free air supply.
It is suggested that an air entrance of 3 to 4 square feet be provided for each dryer
requiring 1700 cfin supply air and an entrance of 5-6 square feet for each super
steam model. Allowance should be made for remote locations of air entrances or
constricting passageways, and also for register/louArre restrictions. Further allow
ance should be made where dryers are located at excessive altitudes or predominantly
low pressure areas. Additional detailed information is provided on Page 10-3.
ELECTRICAL ROVER CONNECTORS.
(30 power) extending out
m
the rear left of the dryer,
be #14 AWG minimum.
Steam and gas dryers are provided with 3 leads
the side of the console (upper) junction box located at
These leads are #16 AWG wires. The supply wiring should
Check data plate located on the upper rear for proper machine voltage and
amperage requirements.
Wire splicing and conduits should be in accordance with local or state reguJations
and all work should be performed by properly licensed and competent electricians.
6-1