Fig. 13—redundant automatic gas control valve, A warning, A caution – Carrier 58TUA User Manual
Page 17
Attention! The text in this document has been recognized automatically. To view the original document, you can use the "Original mode".
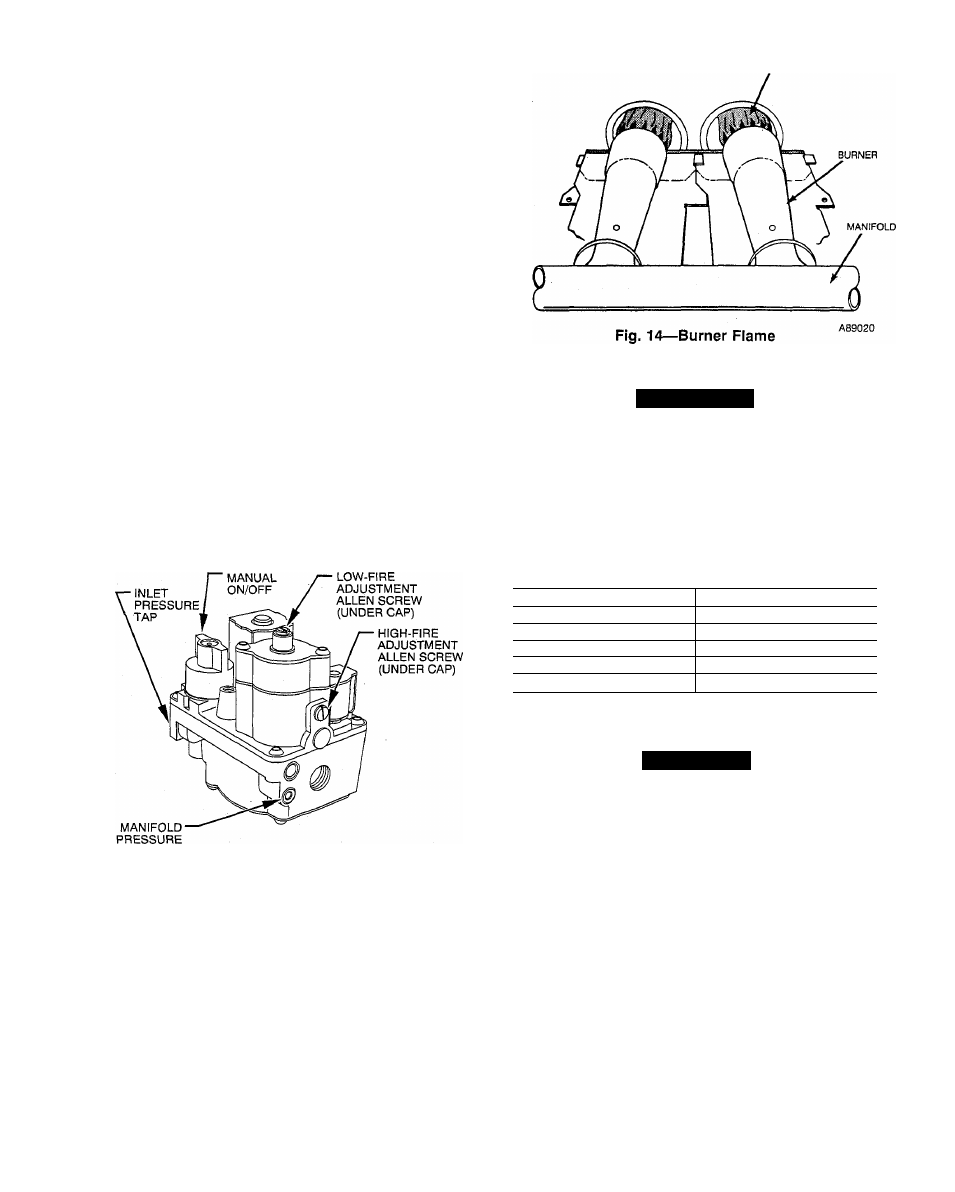
NOTE;
If orifice hole appears damaged or it is suspected to have
been redrilled, check the orifice size with a numbered drill bit of
the correct size. Never use a redrilled orifice. A burr-free and
squarely aligned orifice hole is essential for proper flame charac
teristics.
(7.) Remove jumper on R-W/W1-W2 after high-fire ad
justments.
(8.) Replace gas control regulator adjustment caps.
(9.) Remove regulator adjustment seal cap. (See Fig. 13.)
(10.) Turn adjusting screw counterclockwise to decrease
input. Turn screw clockwise to increase input. DO
NOT set manifold pressure less than 3.2 or more than
3.8-in. maximum wc for natural gas. Make any major
adjustments by changing main burner orifices.
(11.) When correct input is obtained, replace regulator seal
cap. Main burner flame should be clear blue, almost
transparent. (See Fig. 14.)
2. Set temperature rise.
Place SW2 in ON position; jumper R to W/Wl and W2 to
check high gas heat temperature rise. To check low gas heat
temperature rise, remove jumper to W2. Determine air tem
perature rise for both high- and low-fire. Do not exceed the
temperature rise ranges specified on the unit rating plate for
high and low fire.
a. Place duct thermometers in return and supply ducts as near
furnace as possible. Be sure thermometers do not see heat
exchangers so that radiant heat will not affect thermometer
readings. This is particularly important with straight run
ducts.
BURNER FLftME
TAP
A93376
Fig. 13—Redundant Automatic Gas Control Valve
b. When thermometer readings stabilize, subtract return-air
temperature from supply-air temperature to determine tem
perature rise.
NOTE:
If the temperature rise is outside this range, first check:
(1.) Gas input for low and high fire operation.
(2.) Derate for altitude if applicable.
(3.) Return and supply ducts for excessive restrictions
causing static pressures greater than 0.50-in. wc.
c. Adjust air temperature rise by adjusting blower speed.
Increase blower speed to reduce temperature rise. Decrease
blower speed to increase temperature rise. For high fire,
speed tap selection can be 2 or 3 (factory settings). For low
fire, speed tap selection can be 4, (factory setting) or 3 if
high fire speed selection is 2.
A WARNING
Disconnect the electrical power before changing the speed
tap. A failure to follow this warning can cause personal
injury.
d. To change motor speed taps, remove the motor tap lead and
relocate it on the desired terminal on the plug-in terminal
block/speed selector located on the blower housing. (See
Table 13.)
Table 13—Speed Selector
SPEED
TAP NO.*
Common
C
High
1
Med-High
2
Med-Low
3
Low
4
* White wire from control box to common; black wire from control box to high
cooling speed selection; blue wire from control to high heating speed selection;
and red wire from control to low heating/low cooling/continuous fan speed
selection.
A CAUTION
Recheck the temperature rise. It must be within the limits
specified on the unit rating plate. Recommended operation is
at mid point of rise or above.
3. Set thermostat heat anticipator.
The thermostat heat anticipation must be set to match the amp
draw of the electrical components in the R-W/Wl circuit.
Accurate amp draw readings can be obtained at thermostat
subbase terminals R and W. Fig. 15 illustrates an easy method
of obtaining the actual amp draw. The amp reading should be
taken after the blower motor has started and the furnace is
operating in low fire. To operate the furnace in low fire, first
move SW2 to ON position, THEN close R-W/Wl, with
ammeter leads connected across thermostat subbase R-WAVl.
Return SW2 to final desired location after completing the
reading.
NOTE:
When using an electronic thermostat, set the cycle rate for
3 cycles per hr.
CHECK SAFETY CONTROLS
The flame sensor, gas valve, and pressure switches were all
checked in the Start-up section as part of normal operation.
17