Compressor removal — 50qt124, 130 – Carrier 50QT User Manual
Page 10
Attention! The text in this document has been recognized automatically. To view the original document, you can use the "Original mode".
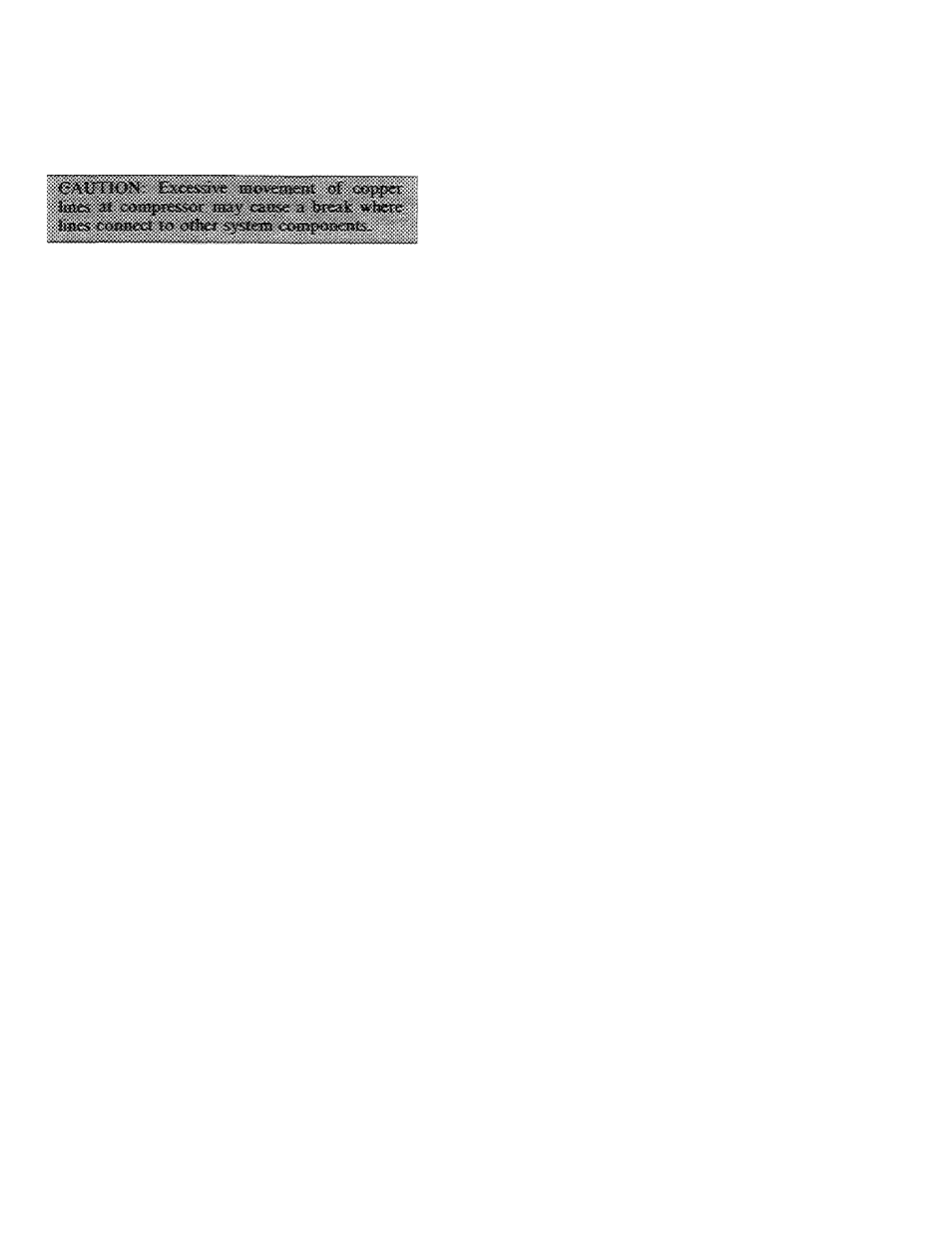
6.
Disconnect compressor wiring at compressor
terminal box.
7. Using a tubing cutter, cut suction and discharge
lines at convenient place near compressor for
easy reassembly to new eompressor with copper
slip couplings.
8.
Remove crankcase heater from compressor
base.
9. Remove clamp holding accumulator to shell.
10.
Remove compressor holddown bolts and lift
compressor out, sliding and tipping it towards
the outside.
11.
Carefully unbraze suction and discharge line
piping stubs from compressor. If oil vapor in
piping stubs ignites, use quenching cloth.
12. Braze piping stubs (removed in step 11) on new
compressor, in .same position as before.
13.
Install new compressor in unit. Braze suction
and discharge lines to compressor piping using
field-supplied copper couplings. Ensure com
pressor holddown bolts are in place. Reinstall
crankcase heater. Connect wiring.
14.
Triple-evacuate to 5000 microns and recharge
unit. See Refrigerant Charging section.
15. Refer to NOTE at the end of this section for
important information.
Compressor Removal — 50QT124, 130
1. Shut off power to unit. Remove chassis indoor
cover. Fig. 1.
2. Remove chassis to truck or shop.
3.
Remove refrigerant from unit using refrigerant
removal methods described in Carrier Standard
Service
Techniques
Manual,
Chapter
1,
Refrigerants.
4.
Remove core from suction and discharge line
Schrader valves.
5. Remove outdoor fan guard.
6. Remove outdoor compressor guard.
7. Remove outdoor propeller fan.
8. Remove outdoor fan orifice ring by removing 4
screws
attaching
it
to
outdoor
fan
motor
bracket.
9. Remove 3 of 4 outdoor fan motor bolts, leaving
bolt at upper right of fan motor in place. Rotate
motor up and out of the way by hinging it on
remaining bolt. Use wire or solder to tie outdoor
fan motor to outdoor coil support on top side
of coil.
10. Using a miniature tubing cutter, cut compressor
suction tube on short vertical run as tube enters
compressor.
11.
Cut compressor discharge tube on horizontal
tubing run approximately 6 to 12 in. from where
it leaves the compressor. Keep crankcase heater
thermostat on right side of cut so it stays in
place when compressor is removed.
12.
Disconnect compressor wiring at compressor
terminal box. Remove compressor wires and
crankcase heater splice from box.
13.
Using an 18-in. long extension on ratchet
wrench, remove 4 compressor holddown bolts.
14. Slide compressor out to edge of pan. Remove
erankcase
heater
by
loosening
worm
drive
clamp and sliding over top of compressor.
15. Remove compressor from pan.
16.
Carefully unbraze suction and discharge line
piping stubs from compressor. If oil vapor in
piping stubs ignites, use quenching cloth.
17. Braze piping stubs (removed in step 11) on new
compressor, in same direction as before.
18.
Using field-supplied copper couplings, install
new compressor in unit.
19. Reassembly is reverse of above procedure.
20.
Triple-evacuate to 5000 microns and recharge
unit. See Refrigerant Charging section.
NOTE: If a compressor failure was caused by
motor winding burnout, the by-products of the
burnout must be separated from the circulating
refrigerant. This must be done before the by
products enter the reversing valve or aceumu-
lator and render parts inoperative. Burnout
by-products can cause future system operating
problems if left in the system.
Clean the system by installing a suetion line
drier in the refrigerant line where the suction gas
enters the reversing valve. During the cooling
cycle, this is the line from the indoor eoil run
ning to the compressor compartment; during
heating cycle, install drier in line between
outdoor eoil and reversing valve. If possible,
run unit in cooling mode when cleaning system
as no defrosting occurs.
To provide protection for the 4-way valve,
do not place filter drier between 4-way valve
and accumulator. Since the suction drier works
on one mode only, temporarily wire the unit in
the seleeted mode (heating or cooling, based on
suction drier location). To insure cooling opera
tion only, install a jumper between terminals
no. 1 and no. 4 on receptaele no. 3. For heating
operation only, remove and insulate one of the
reversing valve solenoid leads. Run unit for
48 hours and check oil for acidity. If satis
factory, remove suction line drier. Refer to
and
follow
procedure
under
AccuRater™
Servicing for cleaning of AccuRater. Rewire
unit to normal condition.
Lubrication — Compressor contains factory oil
charge. Replace oil when lost. See Table 3 for oil
#
10