Indoor-air fan motor removal, Sim oif artd lockout ouit power swply, Biotor î3ao«îî£&, place a pjece of i^wooá over – Carrier 50BK User Manual
Page 18: A caution
Attention! The text in this document has been recognized automatically. To view the original document, you can use the "Original mode".
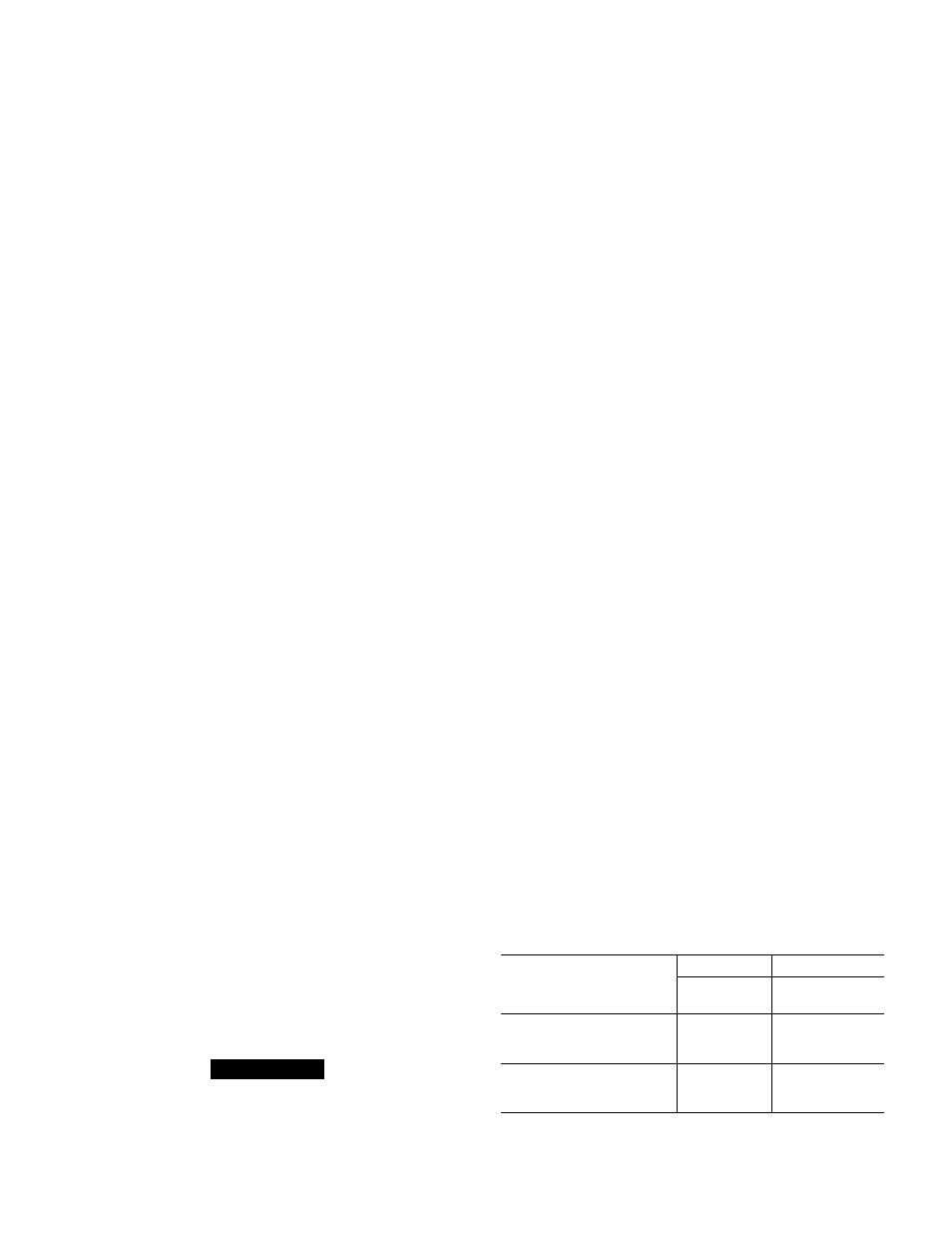
Evaporator
Coil — Protect coil when working
inside unit.
(See screened CAUTION note, page 15.)
Remove dirt and debris from evaporator coil as
required. Clean with a stiff brush, vacuum cleaner
or compressed air. Straighten mashed or bent coil
fins with a fin comb of the correct spacing. Table 1
lists the fins per inch for each coil.
Water-Cooled Condenser(s) may require clean
ing of scale (water deposits). Contact local water
treatment company for best results.
Air-Cooled
Condensers
—
Periodically
inspect
and
clean
depending
on
operating
conditions.
Follow the service instructions provided with the
air-cooled condenser used.
Sight Glasses are provided at the inlet of each
expansion valve. Units may be field charged by
using the sight glass (see Charging the System).
'Charging the System
UNITS
WITH
WATER-COOLED
CONDENSER
(50BJ) — Units are shipped with a full operating
charge of refrigerant. If recharging is necessary
(complete charge lost) weigh in amount of refrig
erant indicated on unit nameplate and Table 1.
If unit has a partial charge, unit may be charged
with sight glass using standard charging techniques.
See Carrier Standard Service Techniques Manual
entitled
Chapter
1,
Refrigerants
for
applicable
procedures.
Adjust
the
water
regulating
valve
to
proper
saturated condensing temperature (168 to 226 psig).
UNITS
WITH
AIR-COOLED
CONDENSER
(50BK) — Units are shipped with a holding charge
only. To charge:
1. Open suction and discharge line service valves.
2.
Blow holding charge, evacuate and leaktest
system.
3.
Add sufficient refrigerant vapor to permit con
tinuous operation after starting unit.
4.
Start unit per Start-Up Section; then, using
standard charging techniques, add refrigerant as
required
to
maintain
normal
operating
conditions.
Use charging chart supplied with condenser. If
information is not available, block off enough of
condenser coil to maintain 220 psig discharge
pressure and charge to a clear sight glass.
Indoor-Air Fan Motor Removal
Sim oif artd lockout ouit power swply.
A CAUTION
ALL 50BJ,BK UNITS — Remove motor as follows:
1. Remove unit access panel and cover of motor
junction box.
2. Disconnect motor wires and remove conduit
connection.
3. Remove motor bolts and slide motor over so
that fan belt can be removed.
4. Disconnect motor ground wire (if present) and
remove motor.
TO REINSTALL MOTORS — Reverse the above
procedures. Align pulleys and adjust belt tension as
described
in
the
section,
Indoor-Air
Ean
Adjustment.
Pressure Relief Devices — The 50BK (condenser
less) and 50BJ,BK044-064 units are equipped with
a fusible-plug type safety relief device on the com
pressor. The relief setting is 197 or 203 E on all units.
All 50BJ (water-cooled) units have a frangible
disc on each condenser. Disc setting is 385 ± 5% psig.
^Crankcase
Heaters
are
supplied
on
all
50BK
(condenserless) units and on 50BJ044-064 water-
cooled units.
The heater reduces the possibility of liquid refrig
erant from accumulating in the compressor crank
case during extended shutdown periods. Heater is
automatically energized whenever unit main power
is on and compressor is stopped. Heater is de
energized when compressor starts.
Do not shut off unit main power supply for an
extended period except for servicing unit. After an
extended shutdown period, turn power supply on at
least 24 hours prior to starting compressor.
If 50BJ units are installed in unheated rooms,
they should be equipped with crankcase heaters. All
units equipped with crankcase heaters require 24
hours warm up time.
High-and Low-Pressure Switches — The high-
pressure switch is located in the electrical panel.
The
low-pressure
switch
is
located
on
top
of
compressor.
Time
Guard®
Control
Circuit
provides
auto
matic
reset
protection
(except
circuit
breaker),
time delay in starting and controlled cycling. If
compressor shuts down for any reason, the control
circuit prevents restart for time periods as follows:
Biotor î3ao«îî£&, place a pjece of i^wooá over
UNIT
50BJ.BK
CIRCUIT
NO.
A
B
Full Cycle
(minutes)
Delayed Start
(seconds)
016
1
5
15
024,028,
1
64
19
034
1 2
5
15
044,054
1
2
5
15
064
1 1 and 2
64
19
Column B shows time delay between compressor
starts under normal thermostat cycling.
17