Service, Fig. 23 — fan belt alignment – Carrier 50BK User Manual
Page 16
Attention! The text in this document has been recognized automatically. To view the original document, you can use the "Original mode".
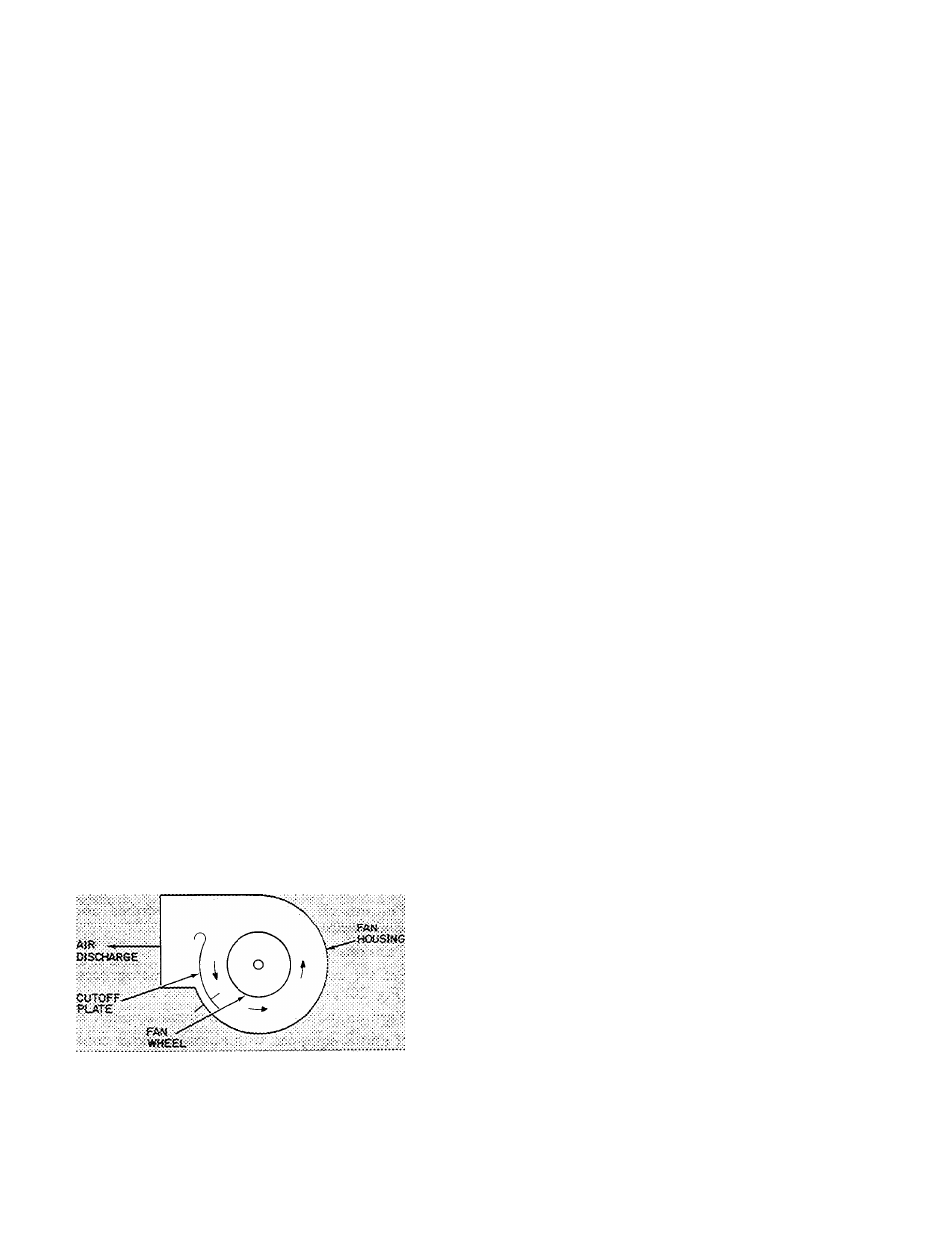
(LEDs) should glow as corresponding cooling
stages come on. In addition, indicating lights on
cover of aecessory timer eontrol panel should
light.
^ NOTE: Depending on job eonditions and dif
ferential between setpoint and discharge tem
peratures, minimum time for all stages to eome
on is 22 minutes.
8.
Turn mieroprocessor SETPOINT knob to 90 F.
The
LEDs
on
mieroproeessor
and
indieating
lights on aceessory timer control panel should
go off as corresponding cooling stages drop out.
Ambient temperature must be less than 90 F for
this test.
9.
When checkout and unit operation are satis
factory, turn off manual bypass switch (step 5),
position
microprocessor
SETPOINT
knob
at
desired temperature (approximately 55 F) and
replace all unit panels.
SERVICE
WARNING; Lock open and tag unit disconnect
before servicing equipment.
CAUTION: Before serv'icing fan compartment.
L Sharp edge.s of evaporator coil fms are ex
posed. To prevent arm inj ury., cover top edge
of evaporator with strip of cardboard or a
few layers of heavy tape.
2. To avoid coil damage, cover coil face with a
piece of plywood or other suitable rigid sheet
material. If any coil fms are mashed or bent,
straighten with a coil fin comb. Check for
refrigerant leaks.
Fan Rotation — Correct fan rotation in respect to
fan outlet is shown in Fig. 22. To check for proper
fan rotation, remove service access panels and jog
fan motor switch. If fan rotation is incorrect, it must
be reversed.
Fig. 22 — Fan Rotation
To reverse the direction of rotation of a 3-phase
fan motor reverse any 2 of the power leads. Refer to
the connection diagram on the inside of motor
terminal box cover for proper reversing procedure
of single-phase motor.
1.
Pulleys and fan belts should be aligned and
adjusted as shown in Fig. 23-25.
2. Tighten motor holddown bolts.
3. Replace service access panels.
Indoor-Air Fan Adjustment — Fan motor pulley
is factory set for speed shown in Table 1. Unit sizes
028-064 have fixed pulleys. A second pulley is
shipped with drive package.
Increasing fan speed increases load on motor;
Do not exceed maximtim allowable fan speed
(Table I) or motor fuB load amps shown on
motor nameplate and in Table 7.
TO CHANGE FAN SPEED
1. Shut off power supply.
2.
Loosen fan belt by loosening fan motor on
mounting
bracket.
Do
not
loosen
mounting
bracket from unit.
3.
Loosen movable pulley flange setscrew (016,024).
See Fig. 25.
4. Select motor pulley diameter. See Table 1.
5.
To increase fan speed, screw movable flange
towards fixed flange; to decrease speed, screw
movable flange away from fixed flange. Use
values shown in Table 1 (016,024).
6.
Set movable flange setscrew at nearest pulley
hub flat and tighten (016,024).
7.
Check pulley alignment and adjust belt tension
as described below.
8.
Check fan operation. Repeat above procedure
as required.
V-BELT INSTALLATION AND TENSIONING
(See Fig. 23, 24, 25 and 26) — Use the following
steps when installing drive belts:
CORRECT
ALIGNMENT
OFF SET
(INCORRECT)
PIGEON TOED
(INCORRECT)
n
ANGLE
(INCORRECT)
Fig. 23 — Fan Belt Alignment
Step 1 — Sheave Conditions — Check condition of
all new and old sheaves. Sheave must have smooth
finish and no sharp edges or burrs. Check for groove
uniformity.
Excessively worn sheaves or improperly
machined grooves can lead to early belt failure.
Non-uniformity of grooves will create an unequal
load distribution in matched set of belts.
Step 2 — Mounting Sheaves — Mount sheaves as
close to bearing as possible.
Excessive overlap may
cause bearing failure.
15