Top Flite Antares User Manual
Page 10
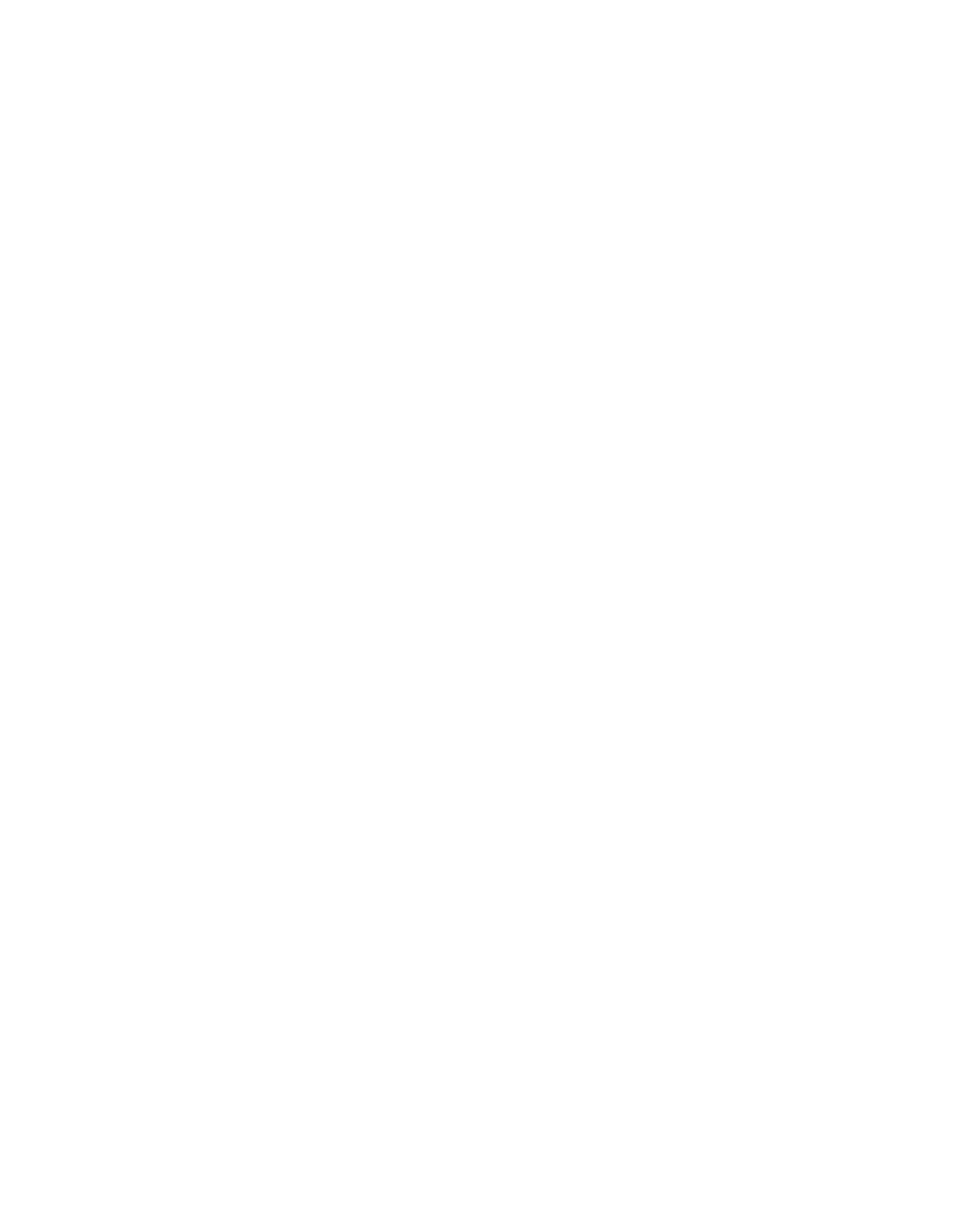
note that the "entry" or lead ing edges a re not particu-
larly sharp, but not just "rounded" either. Approach
thistaskwith care t o c r e a t e t h e intended shapes. Final
sand with light paper and set aside for covering.
BALLASTING
As we mentioned earlier in the Introduction to this
manual, having the capability to incrementally increase
your wing loading to match certain weather or contest
conditions is of great value and simply adds additional
scope to your flying abilities with the ANTARES If you
have opted to build-in the four ballast tubes into the
wings, you now need to develop the weights necessary to
fill them As mentioned earlier, we chose to use 2'lengths
of1/2"O.D. brass tubing ("off the shelf" K&S brand), filled
with poured lead These should weigh about 2.5 ounces
each. Each end of these "slugs" should be carefully
dressed so that they slip easily into and out of the wing's
ballast tubes. Since each wing tube has a capacity of
13-3/4", then each tube can hold up to a total of six (6) slugs
and therefore the total system can hold up to 24 slugs or
60 additional ounces of ballast.
IMPORTANT:
When melting and pouring lead use extreme caution.
Always work with this material in a well ventilated area,
preferably outdoors Always wear heat resistant gloves
Always wear a protective mask over your mouth and
nostrils to avoid fumes (such as a painter's mask). Avoid
prolonged contact with the lead itself to your skin. Always
wear safety glasses or goggles'"
To make these slugs you will need to obtain four (4) stock
12" lengths of K&S Engineering's 1/2" O D. tubing, their
stock #139 and about 4 pounds of lead—we use large
sinkers obtained from the local tackle shop, while the
tubing itself is available from your local hobby shop The
lead was melted in an old iron pot over a hot plate The
tubing was prepared for filling by first using thick CA
adhesive to glue a small circle of 1/8" plywood over one
end The tube was then securely propped-up, on the
ground, sealed end down, with bricks The melted lead
(about 1 pound at a time) was then poured into the open
end of the tube until filled and allowed to cool on it's own
— d o not attempt to cool it with water or any other type of
coolant as this will cause shrinkage of the lead within the
tube. Once the tube has cooled and can be handled,
knock-off the 1/8" ply plug Repeat this process on the
remaining three tubes until you have four lead filled 12"
long slugs.
The slugs are now marked off in 2" increments and sawed
into individual slugs We used a hacksaw for this pur-
pose Now dress the ends of each of the slugs to remove
flash. When complete, you should have 24, 2" brass-
lined lead b a l l a s t i n g slugs Minor discrepancies in
weight between these slugs is not important while any-
thing over about 1/3rd of an ounce might be—check them
with a scale.
Obviously, the lead slugs are loaded into the wing tubes
from the wing roots but these slugs must be held in place,
as close to the fuselage as possible without having the
freedom to move outboard We use pre-measured and
cut lengths of common 1/2" dowel (found in most hard-
ware and I umber supply stores) to hold the slugs in place
These are sanded carefully to fit freely into the wing
tubes So, in order to load, say, four lead slugs into the
wings you will need four 11 3/4" long 1/2" dia dowel "fil-
lers" These fillers a re inserted into the wing ballast tubes
f i r s t , followed by four slugs This should render the slugs
im mobile a gainst the fuselage F-10 ply ribs and the dowel
fillers in the wing tubes In this particular instance, you
have now increased the weight of the airplane by 10
ounces (plus the weight of the dowels, about .064 ounces
per inch) and the wing loading accordingly.
If you are so inclined, as we were, you can now make up a
carrying case of s o r t s that will hold all of your ballast
slugs and dowel f i l l e r s We have gone as far as including
in this case a chart that shows all of the possible wing
loading configurations obtainable with ballast—this case
goes with us to all flying sessions and contests and has
proven itself to be a valuable tool in handling both condi-
tions (weather) and tasks
Remember, all ballast must be as close to the fuselage as
possible, never load the slugs first Also remember that
all ballasting must be symmetrical, the same amount in
the same location on each side of the fuselage Lastly,
remember that the dowel fillers are mandatory for this
ballasting system—a loose lead slug that weighs 2-1/2
ounces develops inertia quickly and can rearrange the
inside of your wing—be sure that it is immobilized by the
filler dowels
WING ASSEMBLY
Before starting this assembly sequence you must decide
whether to build-in the ballast tube option The option is
relatively easy, requiring only the four Estes #BT-5 rocket
tube bodies and the holes for them in the effected wing
ribs. Just make sure that when you make the required
holes and insert the tubes, that they don't bend in any
way—they must be straight
1. Start by removing all of the wing ri bs, not the trai ling-
edge "riblets", from their die-cut sheets Do this
carefully, use the X-acto knife if needed. We have
made it a practice of stacking all of the ribs together,
in the order that they are used and lightly sanding
them to uniform shape with the sanding block Also
be sure that the top and bottom spar notches line-up,
again using the X-acto knife if needed.
2 Next we are going to prepare all of the 1/16" wing
sheeting for use Note that the top and bottom lead-
ing-edge sheeting is 1/16" x 4" x 48", in other words, all
one piece The rest of the sheeting must be "scarfed"
together from the 36" and 18" lengths to produce the
required 48" sheets While the diagram shows you
how to do this, the Wing plan shows you exactly
where to cut and join these sheets (We prefer using
white glue or aliphatic resin type glues, such as
Titebond for these Joints ) This operation should be
done c a r e f u l l y to produce good joints and straight
edges When dry, l i g h t l y use a sanding block to
smooth the joints until they cannot be felt with your
fingers When complete, you should have the follow-
ing pieces of wing sheeting available for assembly:
4 pcs. 1/16" x 4" x 48" unscarfed, top and bottom
leading-edge
4 pcs. 1/16" x 4" x 48" scarfed from 36" and 18" lengths,
top and bottom T.E
10