Nexen RPG25A-GE486T 966740 User Manual
Page 6
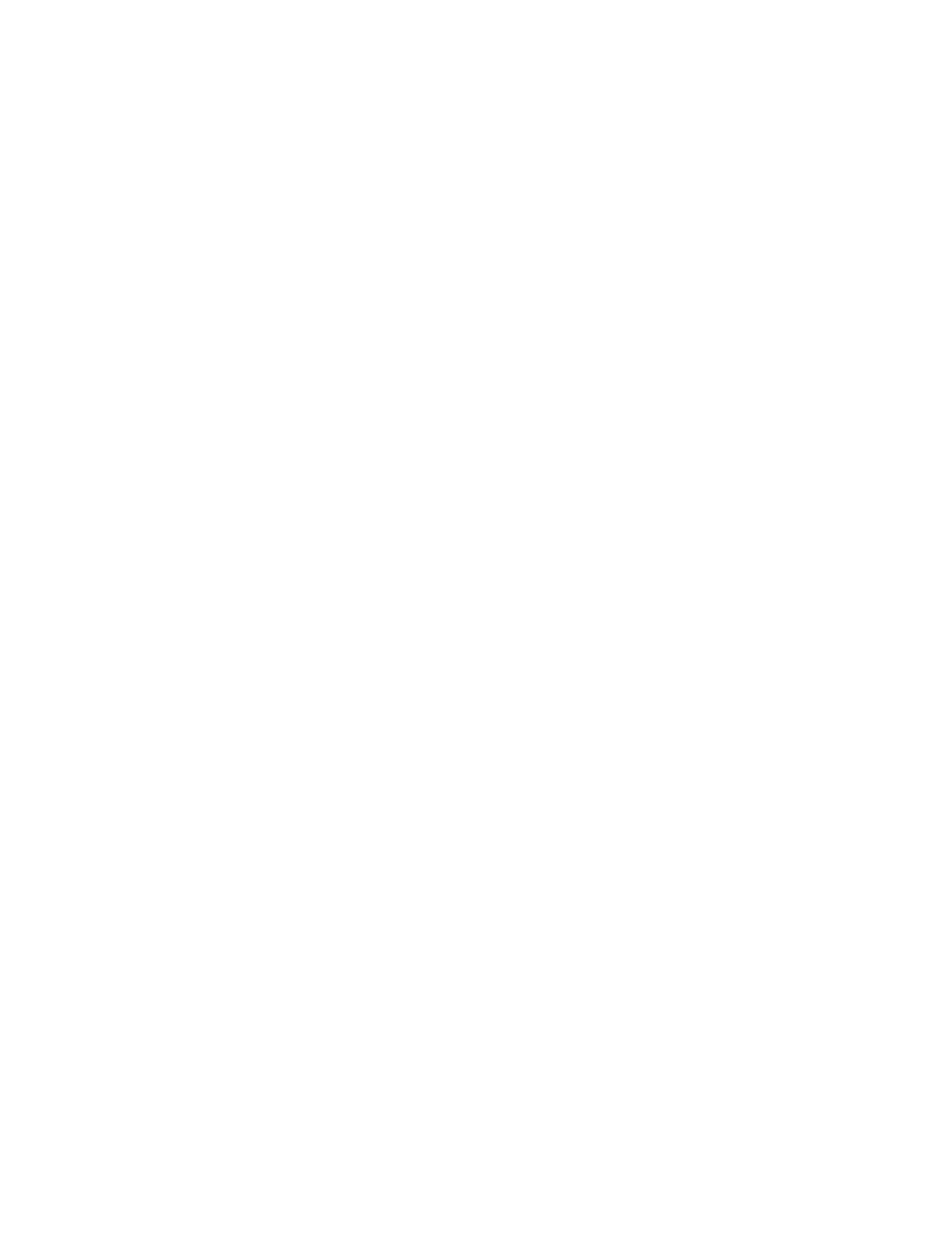
FORM NO. L-21235-G-0413
6
• RPS systems are surface treated with various products depending on the model. All standard pinion product offerings
include uncoated, bearing grade steel rollers. Pinion roller corrosion will lead to pinion needle bearing damage and
then system failure. Always protect the pinion from adverse conditions. As the surface treatments vary depending
on RPS model, review surface treatment specifications carefully to determine whether the RPS system is suitable
for your application based on your familiarity with the corrosion resistant surface treatment or through testing. Nexen
makes no claims for RPS corrosion resistance in any application.
• Nexen can provide additional tapped, untapped or countersunk holes in the side or bottom of the rack or cut the rack
to a specific length for an additional charge.
r
ack
r
equirementS
•
CAUTION
Handle the rack with care; it is a high precision product. Do not drop it, allow anything to fall on it, or place
it on non-flat surfaces that could effect rack straightness. Doing so may negatively effect RPS system performance.
• Five sides of the RPS rack are reference surfaces. The side displaying the part number, or ends that have been
cut (not factory full or half sections) are non-reference surfaces. The side displaying the part number should not be
mounted against the machine bed and cut rack ends must be at the end of the run.
• Secure the rack using all of the available mounting holes to a precision step in the machine bed. Refer to Table 2
for proper fastener tightening torque. This will ensure the highest degree of rack stability.
• Install the RPS system at the temperature at which it will be used to minimize thermal expansion or contraction
effecting the positional accuracy of the RPS system.
• The RPS rack is hardened on the tooth faces only.
• If joining multiple rack segments a special alignment tool is required and is available from Nexen. The alignment tool
ensures proper pinion meshing and system accuracy when the pinion crosses rack joints. When the adjacent racks
are properly positioned, there will be a 0.1 - 0.2 mm gap between their ends. See Figures 4 and 8 for details.
• Avoid mounting the rack teeth up since debris could collect on the rack and interfere with the meshing of the RPS
system. If the teeth must be mounted up, shield the RPS system from debris or install an air knife just ahead of the
pinion.
P
inion
r
equirementS
• Verify shaft runout and diameter tolerances meet Nexen specifications before mounting the pinion. See Figure 11.
• For shaft mounted pinions the shaft length must meet the minimum shaft insertion requirements for proper support and
torque transmission. See the pinion dimensional drawings in the RPS Application and Selection Guide for minimum
shaft insertion values.
•
If using a flange mount pinion verify the dimensions and tolerances of the gearhead flange meet the specifications of
the ISO 9409 standard.
• Mount the pinion as close to a support bearing as possible to minimize shaft deflection.
• The pinion roller bearings are sealed, however it is still recommended that the pinion be shielded from liquids, dust,
and debris.
• Multiple pinions may be used on a single axis to drive a common load. When sizing the RPS system, it is important to
carefully evaluate the loading that is to be seen by each pinion. Perfect load sharing between multiple pinions driving
a common load is difficult to achieve in practice and therefore additional service factors are typically recommended.
Contact Nexen for more information on sizing the RPS system under these conditions.
• The RPS system can be operated such that the pinion remains stationary while the rack moves. In this scenario,
a supporting structure and guiding system is still required for the rack such that the pinion preload and alignment
remains within specifications.
- RPG20A-GE180T 966734 RPG20A-GE140T 966706 RPG32A-GE0450T 966685 RPG16A-GE400T 966656 RPG20A-GE150T 966615 RPG16A-GE150T 966557 RPG16A-GE936T 966556 RPG4014A-GE192T 966548 RPG4014A-GE072T 966547 RPS25 966679 RPS25 966678 RPS20 966707 RPG32A-GE0760T 966779 ISO9409-064-SS 960855 ISO9409-090 960850 ISO9409-064 960851 ISO9409-200 960854 ISO9409-140 960853 ISO9409-110 960852 RPS40 966543 RPS32 966533 RPS25 966523 RPS20 966513 RPS12 966508 RPS10 966507 RPS16 966503 RPS20 966618 RPS16 966715 RPS16 966687 RPS32 966677 RPS40 966697 RPS4014 966700 RPS25 966673 RPS20 966753 RPS20 966675 RPS20 966781 RPS16 966650 RPS32 966680 RPS4014 966693 RPS40 966690 RPS25 966670 RPS20 966660 RPS16 966850 RPS32 966853 RPS25 966852 RPS4014 966855 RPS40 966854 RPS20 966851 RPS16 966605 RPS16 966606 RPS16 966651 RPS32 966681 RPS16 966654 RPS32 966608 RPS4014 966695 RPS40 966692 RPS16 966652 RPS32 966682 RPS25 966672 RPS20 966662 RPS12 966769 RPS10 966768 RPS16 966777 RPS32 966609 RPS16 966709 RPS25 966671 RPS4014 966694 RPS40 966691 RPS20 966661 RPS16 966800 RPS32 966806 RPS4014 966811 RPS40 966809 RPS16 966801 RPS32 966807 RPS25 966805 RPS20 966803 RPS25 966804 RPS40 966810 RPS40 966808 RPS20 966802 RPS16 966741 RPS16 966742 RPS25 966755 RPS20 966619 RPS4014 966601 RPS40 966631 RPS4014 966647 RPS32 966642 RPS16 966602 RPS32 966632 RPS25 966622 RPS20 966612 RPS25 966621 RPS4014 966646 RPS40 966641 RPS20 966611