Nexen RPG25A-GE486T 966740 User Manual
Page 5
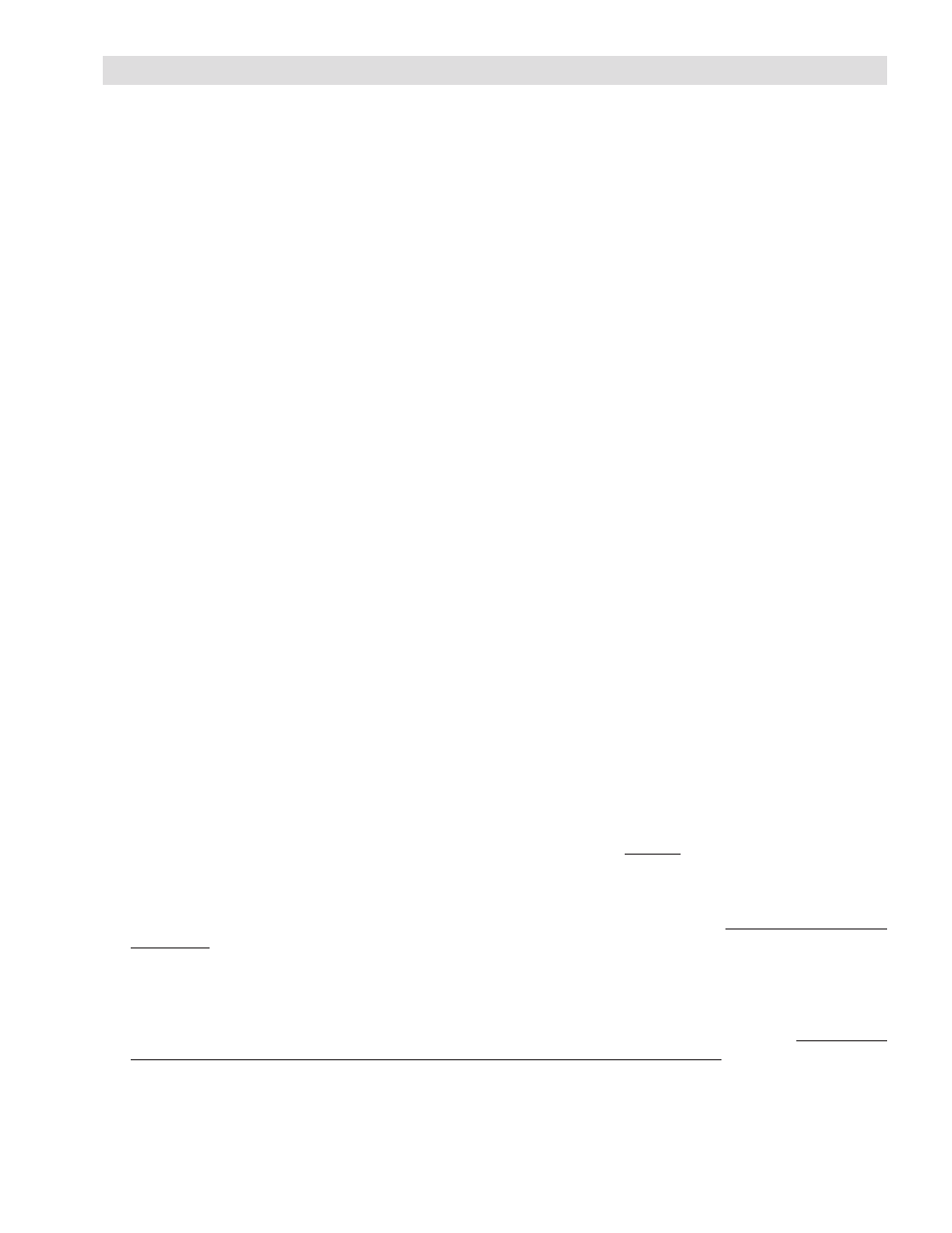
5
FORM NO. L-21235-G-0413
SYSTEM DESIGN OVERVIEW
The machine design guidelines, installation procedures, specifications, and tolerances, listed in this document
are designed to obtain Nexen’s published RPS performance ratings with reasonable effort. In some cases
some of these requirements can be deviated from with a reduction in the RPS system performance.
Contact Nexen to determine if the desired deviation is possible and its effect on system performance.
G
eneral
S
yStem
r
equirementS
• Unlike traditional rack and pinion drives, the RPS system has zero mechanical clearance and requires a system
preload for proper operation. This preload must remain relatively consistent over the entire run to obtain optimal
system performance and life. To achieve this it is crucial that the guiding system be as parallel as possible to the RPS
system and not converge or diverge at any point. If the system converges, the pinion preload will become excessive
and increase noise, reduce pinion roller bearing life, and potentially bind the system. If the system diverges, pinion
preload will be lost causing backlash, a loss of positional accuracy, increase in noise, and reduction in system life.
The main consideration is that the guiding system and the RPS system are rising or falling at the same place in the
run so the pinion preload remains within specifications. The best way to minimize the variance between the guiding
system and the Roller Pinion system is to machine their mounting locations in a single machining operation. See
Figures 1 and 2 for more details.
• Make sure that the machine bed and guiding system are rigid enough to prevent deflection that will affect RPS system
preload and pinion alignment.
• The rack and guiding system installation parallelism tolerances shown in Figure 2 are greater than the system preload.
The RPS system has been designed to provide its rated performance under these conditions.
• The bottom of the rack and one side must be supported by a step in the machine bed at least half the rack thickness.
The rack should not be supported only by fasteners or pins. See Figure 3 for specifications.
• Over long distances a single piece machine bed will become impractical requiring a segmented bed. When installing
the guiding system and the RPS rack, their joints should not be located near the machine bed joints but span them
as much as possible.
• The RPS system generates a separation force between the pinion and rack. Make sure this is accounted for when
selecting the guiding system or evaluating reducer or motor overhung load ratings. See product data for maximum
pressure angle specifications.
• The RPS system requires a mechanism to achieve proper system preload. It is recommended that the pinion be
moved into the rack not vice versa. The recommended method is to mount the servo drive system on a sliding bracket
that has an adjustment to push it into and pull it away from the rack. Another possible preloading method utilizes a
bracket with eccentric mounting slot pattern. Nexen offers a preloading mechanism that is easy to integrate into your
application as shown in Figure 18. Spring loaded preloading mechanisms shall not be used since the spring force
required to counteract the separation forces are much higher than the allowed preloading force and would cause a
reduction in pinion needle bearing life and increase system noise. See Figure 3 for more details.
• Under most circumstances, the RPS system requires periodic lubrication. In special cases, Premium and Endurance
Grade RPS can be operated lubrication free if the maximum speed does not exceed 0.5 m/s [1.64 ft/s]. Typically
this will involve dirty environments where contaminates will be attracted/stick to the lubricant on the rack creating
mechanical interference or an abrasive paste that can accelerate wear. Other applications where no rack lubrication
may be beneficial include food processing, clean rooms, coating, and others where low particle emissions are desirable.
If the RPS system is operated lubrication free there may be some reduction in life which could vary depending on
the application. Do not run the RPS system lubrication free unless there is a strong reason to do so. The Standard
and Universal Grades of RPS shall not be run lubrication free under any circumstances. Consult Nexen for more
information regarding alternative lubrication options or lubrication-free applications.
• Do not use the RPS system in environments with temperatures outside of a -5 - 40º C (23 - 104º F) range‚ or with
wide temperature variations since thermal expansion can effect the preload and meshing of the system. If you have
an application with any of these characteristics consult Nexen.
- RPG20A-GE180T 966734 RPG20A-GE140T 966706 RPG32A-GE0450T 966685 RPG16A-GE400T 966656 RPG20A-GE150T 966615 RPG16A-GE150T 966557 RPG16A-GE936T 966556 RPG4014A-GE192T 966548 RPG4014A-GE072T 966547 RPS25 966679 RPS25 966678 RPS20 966707 RPG32A-GE0760T 966779 ISO9409-064-SS 960855 ISO9409-090 960850 ISO9409-064 960851 ISO9409-200 960854 ISO9409-140 960853 ISO9409-110 960852 RPS40 966543 RPS32 966533 RPS25 966523 RPS20 966513 RPS12 966508 RPS10 966507 RPS16 966503 RPS20 966618 RPS16 966715 RPS16 966687 RPS32 966677 RPS40 966697 RPS4014 966700 RPS25 966673 RPS20 966753 RPS20 966675 RPS20 966781 RPS16 966650 RPS32 966680 RPS4014 966693 RPS40 966690 RPS25 966670 RPS20 966660 RPS16 966850 RPS32 966853 RPS25 966852 RPS4014 966855 RPS40 966854 RPS20 966851 RPS16 966605 RPS16 966606 RPS16 966651 RPS32 966681 RPS16 966654 RPS32 966608 RPS4014 966695 RPS40 966692 RPS16 966652 RPS32 966682 RPS25 966672 RPS20 966662 RPS12 966769 RPS10 966768 RPS16 966777 RPS32 966609 RPS16 966709 RPS25 966671 RPS4014 966694 RPS40 966691 RPS20 966661 RPS16 966800 RPS32 966806 RPS4014 966811 RPS40 966809 RPS16 966801 RPS32 966807 RPS25 966805 RPS20 966803 RPS25 966804 RPS40 966810 RPS40 966808 RPS20 966802 RPS16 966741 RPS16 966742 RPS25 966755 RPS20 966619 RPS4014 966601 RPS40 966631 RPS4014 966647 RPS32 966642 RPS16 966602 RPS32 966632 RPS25 966622 RPS20 966612 RPS25 966621 RPS4014 966646 RPS40 966641 RPS20 966611