Nexen RPG25A-GE486T 966740 User Manual
Page 17
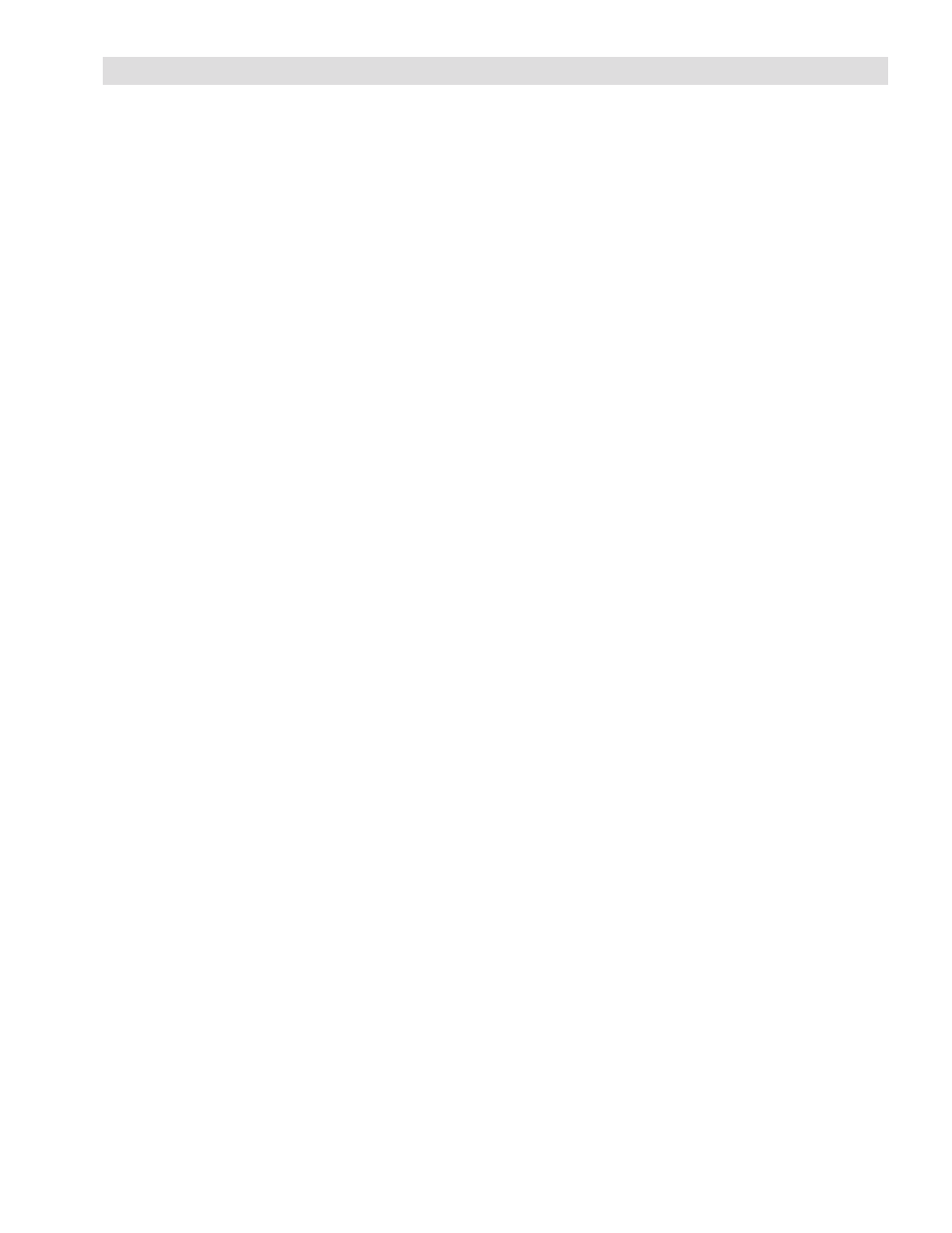
17
FORM NO. L-21235-G-0413
LUBRICATION
The pinion needle bearings are sealed and lubricated for
life and cannot be serviced.
Nexen recommends lubricating the rack or individual roller
contacts every 2 million pinion revolutions or 6 months,
which ever comes first, but it may need to be lubricated
more frequently based on the application conditions, and
observable tooth or roller wear.
When lubricating the RPS system inspect the pinion rollers
and rack teeth for any abnormal wear patterns and ensure
the pinion rollers are not seized or have excessive play.
Wear on the edges of the rack teeth (not uniform across
the tooth face) or rings on the rollers indicate an alignment
problem which should be corrected to obtain maximum
system performance and life.
The rollers in new pinions, especially larger sizes, can
seem difficult to turn due to seal drag. This improves as
the pinion breaks in.
THK AFC is the recommended grease for rack tooth
lubrication although THK AFA grease can also be
used. Both can be found on the RPS product pages of
Nexen’s website under accessories. Greases for special
applications such as food grade, vacuum, or others are
allowed if they use a synthetic base, a polyurea thickener,
and meet the following Kinematic Viscosity Levels:
CST@40C = 25; CST@100C = 5. Contact Nexen for
recommendations on alternative greases.
The RPS system can be lubricated in two ways:
1. Apply grease to the pinion rollers and roll the pinion
back and forth 5 times over one meter of rack,
repeating the process for each meter of rack.
2. Using a swab apply a very small dab of grease on the
middle of each tooth face and roll the pinion back and
forth over the entire length of the run 5 times.
Wipe excess grease from the sides of the rack and pinion
body to prevent grease being thrown off during operation
and for general cleanliness.
Maximum RPS system life will be obtained by following
the recommended lubrication intervals as stated above.
In some special applications the Premium and Endurance
models of RPS rack can be operated lubrication free if
the maximum speed does not exceed 0.5 m/s [1.64 ft/s].
Typically lubrication free applications involve:
•
Dirty environments where contaminates will be
attracted/stick to the lubricant on the rack creating
mechanical interference or an abrasive paste that can
accelerate wear.
• Food processing
• Clean rooms or applications where very low particle
emissions are desired
• Vacuum environments
• Applications where periodic servicing is problematic
If the RPS System is run lubrication free there will be some
reduction in life of the RPS system which will vary widely
depending on the application. The Standard and Universal
models of RPS rack cannot be run lubrication free under
any circumstances. Contact Nexen for more information.
- RPG20A-GE180T 966734 RPG20A-GE140T 966706 RPG32A-GE0450T 966685 RPG16A-GE400T 966656 RPG20A-GE150T 966615 RPG16A-GE150T 966557 RPG16A-GE936T 966556 RPG4014A-GE192T 966548 RPG4014A-GE072T 966547 RPS25 966679 RPS25 966678 RPS20 966707 RPG32A-GE0760T 966779 ISO9409-064-SS 960855 ISO9409-090 960850 ISO9409-064 960851 ISO9409-200 960854 ISO9409-140 960853 ISO9409-110 960852 RPS40 966543 RPS32 966533 RPS25 966523 RPS20 966513 RPS12 966508 RPS10 966507 RPS16 966503 RPS20 966618 RPS16 966715 RPS16 966687 RPS32 966677 RPS40 966697 RPS4014 966700 RPS25 966673 RPS20 966753 RPS20 966675 RPS20 966781 RPS16 966650 RPS32 966680 RPS4014 966693 RPS40 966690 RPS25 966670 RPS20 966660 RPS16 966850 RPS32 966853 RPS25 966852 RPS4014 966855 RPS40 966854 RPS20 966851 RPS16 966605 RPS16 966606 RPS16 966651 RPS32 966681 RPS16 966654 RPS32 966608 RPS4014 966695 RPS40 966692 RPS16 966652 RPS32 966682 RPS25 966672 RPS20 966662 RPS12 966769 RPS10 966768 RPS16 966777 RPS32 966609 RPS16 966709 RPS25 966671 RPS4014 966694 RPS40 966691 RPS20 966661 RPS16 966800 RPS32 966806 RPS4014 966811 RPS40 966809 RPS16 966801 RPS32 966807 RPS25 966805 RPS20 966803 RPS25 966804 RPS40 966810 RPS40 966808 RPS20 966802 RPS16 966741 RPS16 966742 RPS25 966755 RPS20 966619 RPS4014 966601 RPS40 966631 RPS4014 966647 RPS32 966642 RPS16 966602 RPS32 966632 RPS25 966622 RPS20 966612 RPS25 966621 RPS4014 966646 RPS40 966641 RPS20 966611